Welcome to My Blog!
Before we dive into the content, I’d love for you to join me on my social media platforms where I share more insights, engage with the community, and post updates. Here’s how you can connect with me:
Facebook:https://www.facebook.com/profile.php?id=100090797846538
Now, let’s get started on our journey together. I hope you find the content here insightful, engaging, and valuable.
Table of Contents
Introduction
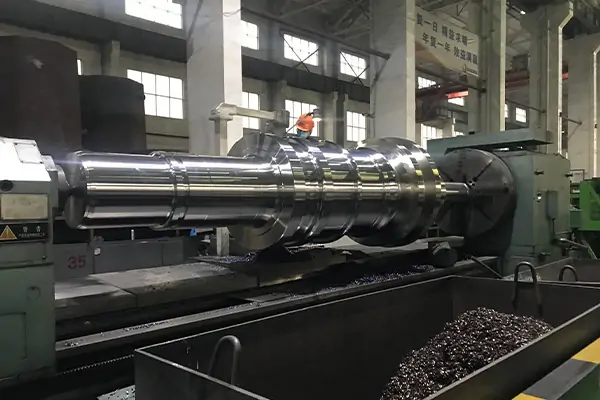
Tool steels are essential materials in manufacturing and engineering, known for their hardness, durability, and resistance to wear. They are widely used in tools, dies, molds, and other high-stress applications. However, despite their impressive properties, tool steels can sometimes fail, leading to costly downtime and inefficiencies. In this blog, we will explore seven common mistakes that contribute to the failure of tool steels and how to avoid them. By understanding these pitfalls, you can maximize the performance and lifespan of your tool steels.
Understanding Tool Steels
Tool steels are a category of carbon and alloy steels specifically designed for toolmaking. They are characterized by their high hardness, wear resistance, and ability to retain their shape under extreme conditions. Common types of tool steels include water-hardening, oil-hardening, air-hardening, and high-speed steels. Each type has unique properties tailored to specific applications, such as cutting, shaping, or stamping.
Despite their robustness, tool steels are not immune to failure. The following sections will delve into the most common reasons why tool steels fail and how to mitigate these issues.
7 Common Mistakes That Lead to Tool Steel Failure
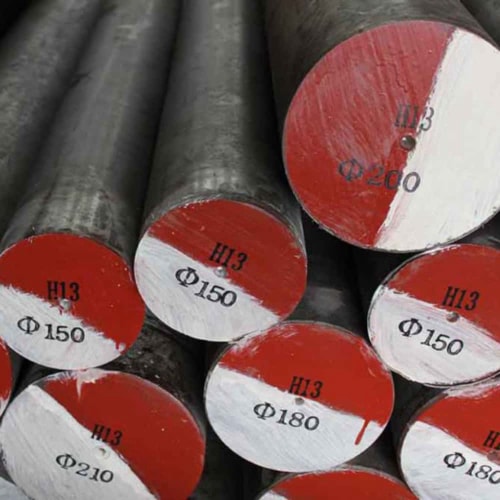
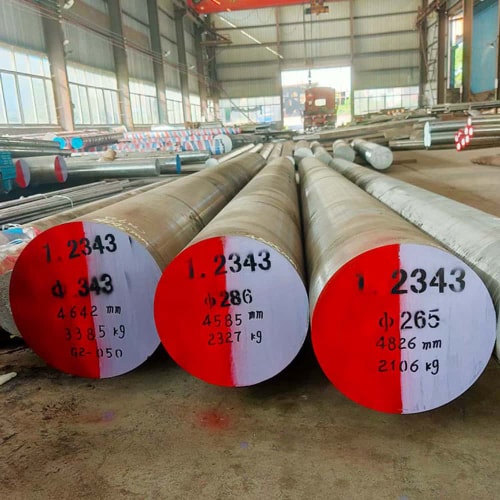
1. Improper Material Selection
One of the most common mistakes is choosing the wrong type of tool steel for a specific application. Each tool steel variant is designed to excel under certain conditions, and using the wrong type can lead to premature failure. For example, using a water-hardening tool steel in a high-temperature environment can cause it to lose its hardness and wear resistance.
2. Inadequate Heat Treatment
Heat treatment is a critical process that enhances the properties of tool steels, such as hardness and toughness. However, improper heat treatment techniques, such as incorrect temperature settings or insufficient cooling rates, can result in brittleness, cracking, or reduced wear resistance.
3. Poor Machining Practices
Machining tool steels requires precision and expertise. Poor machining practices, such as using incorrect cutting speeds or inadequate lubrication, can introduce stress concentrations, micro-cracks, or surface defects, all of which can lead to failure under operational stress.
4. Overlooking Surface Finish
The surface finish of tool steels plays a significant role in their performance. Rough or uneven surfaces can become initiation points for cracks or wear. Proper polishing and finishing techniques are essential to ensure the longevity of tool steels.
5. Ignoring Corrosion Resistance
While tool steels are known for their hardness, some variants are less resistant to corrosion. Using tool steels in corrosive environments without proper protective measures can lead to rust, pitting, and eventual failure.
6. Excessive Load or Stress
Tool steels are designed to withstand high stress, but exceeding their load-bearing capacity can cause deformation or fracture. It is crucial to understand the operational limits of the tool steel being used and avoid overloading.
7. Lack of Maintenance
Regular maintenance is essential to keep tool steels in optimal condition. Neglecting maintenance, such as failing to inspect for wear or address minor damages, can result in unexpected failures during critical operations.
How to Avoid Tool Steel Failure
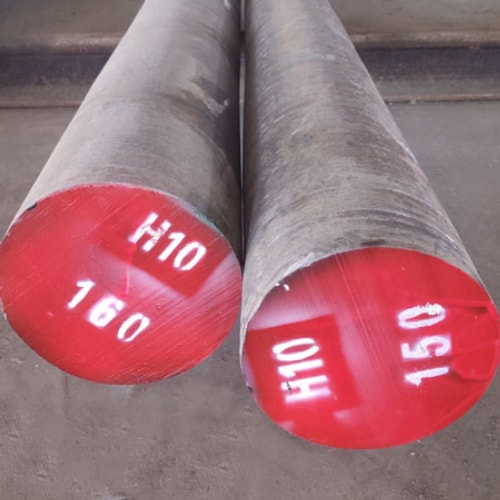
To prevent the mistakes mentioned above, follow these best practices:
- Choose the Right Material: Select the appropriate type of tool steel based on the specific application and operating conditions.
- Follow Proper Heat Treatment Procedures: Adhere to recommended heat treatment guidelines to achieve the desired properties.
- Use Precision Machining Techniques: Employ correct cutting speeds, tools, and lubrication during machining.
- Ensure a Smooth Surface Finish: Polish and finish tool steels to minimize stress concentrations and wear.
- Protect Against Corrosion: Apply protective coatings or use corrosion-resistant tool steels in harsh environments.
- Operate Within Load Limits: Avoid exceeding the designed load capacity of the tool steel.
- Perform Regular Maintenance: Inspect tool steels regularly and address any signs of wear or damage promptly.
Comparison
The table below provides an overview of the most common types of tool steels and their key properties:
Type of Tool Steel | Hardness | Wear Resistance | Toughness | Application |
---|---|---|---|---|
Water-Hardening | High | Moderate | Low | Cutting tools, drills |
Oil-Hardening | High | High | Moderate | Dies, molds |
Air-Hardening | Very High | Very High | High | Punches, shear blades |
High-Speed | Extremely High | Extremely High | Moderate | Cutting tools, milling machines |
Hot-Work | Moderate | High | High | Forging dies, extrusion tools |
Conclusion
Tool steels are indispensable in many industries, but their failure can lead to significant disruptions and costs. By understanding the common mistakes that contribute to tool steel failure—such as improper material selection, inadequate heat treatment, and poor machining practices—you can take proactive steps to avoid these pitfalls. Following best practices in material selection, processing, and maintenance will ensure that your tool steels perform reliably and efficiently, even under the most demanding conditions.
Whether you’re working with water-hardening, oil-hardening, or high-speed tool steels, the key to success lies in careful planning and execution. By doing so, you can maximize the potential of these remarkable materials and achieve long-lasting results in your applications.
FAQ
What are tool steels used for?
Tool steels are primarily used in the manufacturing of tools, dies, molds, and other components that require high hardness, wear resistance, and durability.
How does heat treatment affect tool steels?
Heat treatment enhances the hardness, toughness, and wear resistance of tool steels. Improper heat treatment can lead to brittleness or reduced performance.
Can tool steels corrode?
Some tool steels are less resistant to corrosion and may require protective coatings or treatments when used in corrosive environments.
What is the difference between water-hardening and oil-hardening tool steels?
Water-hardening tool steels are quenched in water for rapid cooling, resulting in high hardness but lower toughness. Oil-hardening tool steels are quenched in oil, providing a balance of hardness and toughness.
How can I extend the lifespan of my tool steels?
Regular maintenance, proper material selection, and adherence to operational limits can significantly extend the lifespan of tool steels.