Welcome to My Blog! 🌟
Before we dive into the content, I’d love for you to join me on my social media platforms. It’s where I share more insights, engage with our vibrant community, and post regular updates. Here’s how you can stay connected:
📘 Facebook: Connect with me on Facebook
Now, let’s embark on this journey together. I hope you find the content here insightful, engaging, and most importantly, valuable. Let’s explore, learn, and grow together! 🚀
Table of Contents
Introduction
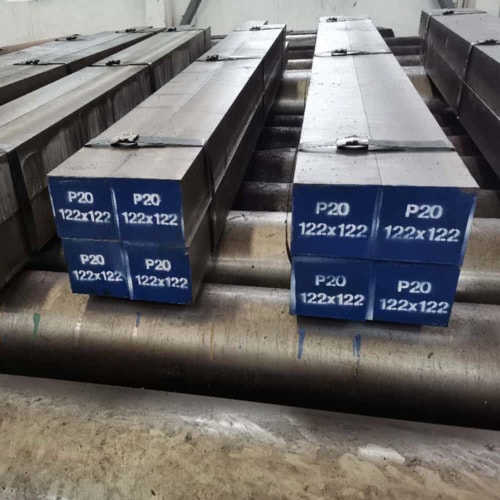
P20 mold steel has long been a preferred material in the tooling industry due to its excellent machinability, durability, and cost-effectiveness. Widely used in plastic injection molds, die-casting tools, and other precision tooling applications, p20 mold steel offers a balanced combination of hardness, toughness, and polishability. This blog explores the key reasons why p20 mold steel remains a dominant choice for manufacturers and toolmakers worldwide.
Key Characteristics of This Versatile Tooling Material
This widely-used tool steel grade offers an exceptional combination of properties that make it indispensable in modern manufacturing. As a low-alloy steel variant, it provides manufacturers with an optimal balance between performance and cost-efficiency. Let’s examine its defining characteristics in greater detail:
Superior Machining Performance
In its pre-hardened condition, this material demonstrates excellent machinability that significantly enhances production efficiency. The relatively low cutting forces required enable:
- Faster machining speeds compared to higher alloy steels
- Reduced tool wear during operations
- Ability to maintain tight tolerances
- Lower power consumption during processing
This machining advantage becomes particularly valuable when producing complex mold geometries or when working with intricate details that require precision tool paths.
Optimal Hardness Characteristics
Supplied with a hardness range typically between 28-32 HRC, this steel provides:
- Adequate rigidity for most common tooling applications
- Sufficient toughness to withstand operational stresses
- Good resistance to plastic deformation
- Balanced performance in both impact and wear scenarios
The moderate hardness level makes it particularly suitable for applications where extreme wear resistance isn’t the primary requirement, while still offering enough durability for extended production runs.
Exceptional Surface Finishing Capabilities
The material’s fine-grained microstructure contributes to several finishing advantages:
- Capability to achieve mirror-like surface finishes (Ra < 0.05 μm)
- Consistent results across large surface areas
- Excellent response to polishing and texturing processes
- Stable performance through multiple production cycles
These characteristics prove especially valuable in plastic injection molding applications where part appearance and surface quality are critical to product success.
Welding and Repair Flexibility
The material’s composition provides several benefits regarding maintenance and modification:
- Good weldability without requiring complex preheating procedures
- Minimal risk of cracking in repair situations
- Ability to accept various welding methods (TIG, MIG, laser)
- Relatively straightforward post-weld heat treatment requirements
This repair flexibility helps reduce downtime and extends the service life of expensive tooling components.
Consistent Performance Throughout
The uniform material properties ensure:
- Predictable behavior during machining operations
- Even wear characteristics across tool surfaces
- Stable dimensional accuracy under thermal cycling
- Reliable performance in production environments
This consistency becomes increasingly important as tool complexity grows and production volumes increase, helping manufacturers maintain quality standards throughout the product lifecycle.
Additional Notable Properties
Beyond these primary characteristics, the material also offers:
- Good thermal conductivity for temperature management
- Moderate corrosion resistance (enhanced in modified versions)
- Favorable strength-to-weight ratio
- Compatibility with various surface treatments
These combined attributes explain why this particular steel grade has become so prevalent across multiple industries and applications. The balanced property profile allows toolmakers to address diverse manufacturing challenges while maintaining cost-effectiveness in both production and maintenance phases.
Applications of P20 Mold Steel
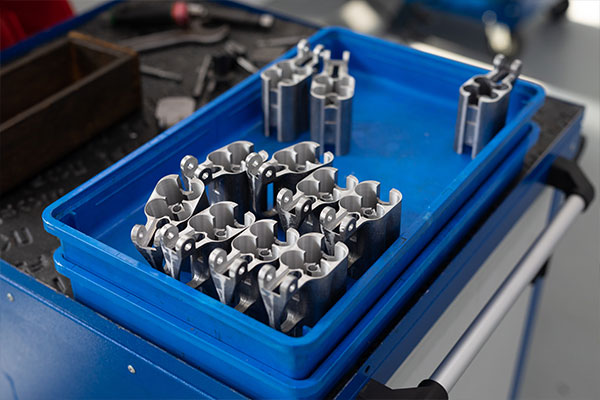
P20 mold steel is widely used across multiple industries due to its adaptability and performance. Some common applications include:
Plastic Injection Molding
P20 mold steel is a top choice for plastic injection molds because of its ability to withstand high pressures and temperatures while maintaining dimensional stability. Its polishability ensures smooth mold surfaces, which is crucial for producing high-quality plastic parts.
Die Casting
While not as hard as some high-alloy steels, p20 mold steel is still used in die-casting applications where moderate wear resistance is sufficient. Its machinability allows for faster production of complex die shapes.
Stamping and Forming Tools
For stamping and forming operations, p20 mold steel provides a good balance between toughness and wear resistance. Its pre-hardened state reduces the need for additional heat treatment, saving time and costs.
Advantages Over Other Tool Steels
P20 mold steel offers several advantages compared to other tool steels, such as H13, S7, or D2:
Property | P20 Mold Steel | H13 Tool Steel | D2 Tool Steel |
---|---|---|---|
Machinability | Excellent | Good | Moderate |
Hardness (HRC) | 28-32 | 48-52 | 58-62 |
Polishability | Excellent | Good | Moderate |
Cost | Lower | Higher | Higher |
As seen in the table, p20 mold steel provides a more cost-effective solution for applications that do not require extreme hardness or wear resistance.
Heat Treatment and Processing
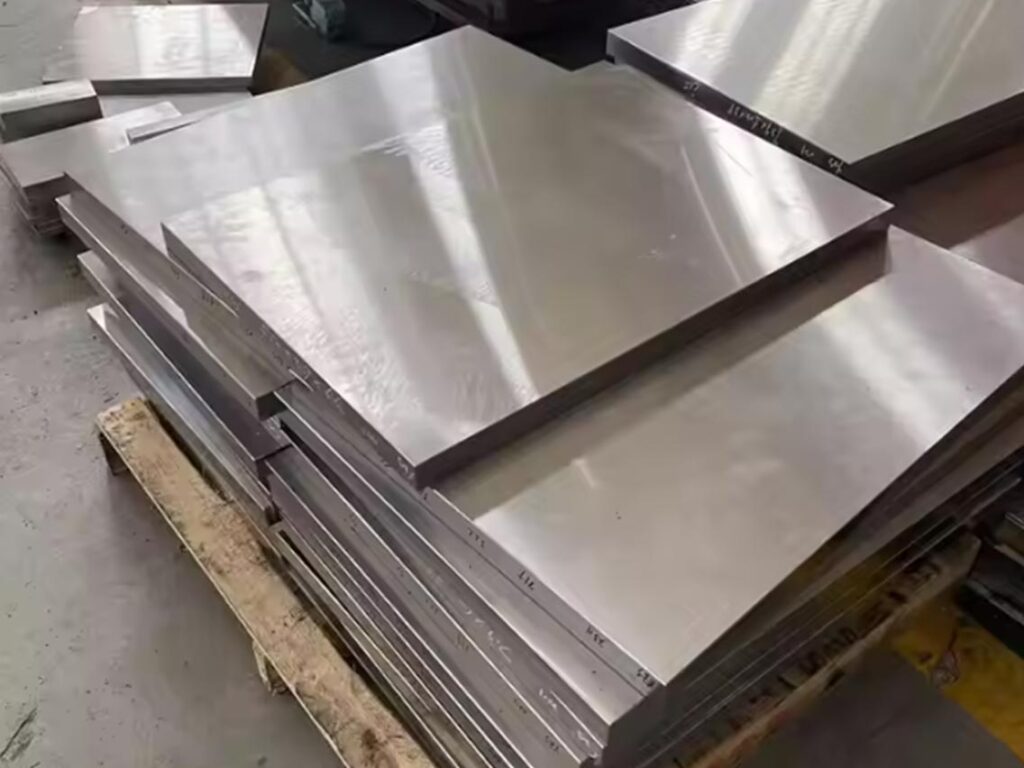
Although p20 mold steel is often used in its pre-hardened state, it can undergo further heat treatment to enhance its properties:
- Annealing: Improves machinability before hardening.
- Hardening: Can be hardened to 50-52 HRC for increased wear resistance.
- Tempering: Reduces brittleness after hardening.
However, many manufacturers prefer using p20 mold steel as-supplied to avoid additional processing costs.
Common Challenges and Solutions
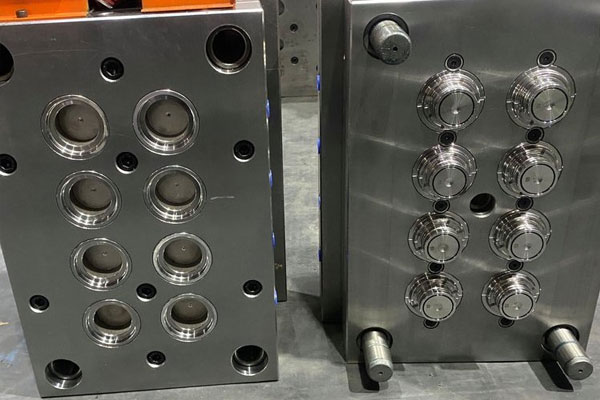
While p20 mold steel is highly reliable, certain challenges may arise:
Wear in High-Volume Production
For high-volume applications, p20 mold steel may experience wear over time. Solutions include:
- Applying surface treatments like nitriding.
- Using higher-hardness inserts in critical areas.
Corrosion in Humid Environments
P20 mold steel is not inherently corrosion-resistant. To mitigate this:
- Apply protective coatings.
- Use stainless steel variants like P20+Ni.
Conclusion
P20 mold steel remains a dominant material in tooling due to its excellent machinability, polishability, and cost-effectiveness. While it may not be the hardest or most wear-resistant steel available, its balanced properties make it ideal for a wide range of applications. By understanding its strengths and limitations, manufacturers can maximize the benefits of p20 mold steel in their tooling processes.
FAQ
What is p20 mold steel used for?
P20 mold steel is primarily used for plastic injection molds, die-casting tools, and stamping dies due to its machinability and polishability.
Can p20 mold steel be welded?
Yes, p20 mold steel has good weldability, though proper preheating and post-weld heat treatment may be necessary.
How does p20 mold steel compare to H13?
P20 mold steel is softer and more machinable than H13, making it better suited for less abrasive applications.
Is p20 mold steel corrosion-resistant?
No, it is not corrosion-resistant, but corrosion-resistant variants like P20+Ni are available.