Welcome to My Blog!
Before we dive into the content, I’d love for you to join me on my social media platforms where I share more insights, engage with the community, and post updates. Here’s how you can connect with me:
Facebook:https://www.facebook.com/profile.php?id=100087990137347
LinkedIn:https://www.linkedin.com/company/89825762/admin/dashboard/
YouTube:www.youtube.com/@carbonsteelsupply-kj9lw
TikTok:www.tiktok.com/@carbonsteelsupply
Now, let’s get started on our journey together. I hope you find the content here insightful, engaging, and valuable.
Introduction
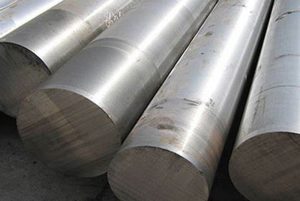
M2 tool steel is a popular choice in the manufacturing industry, especially for high-speed tools. Known for its excellent hardness, wear resistance, and versatility, M2 tool steel is ideal for applications that demand durability and high performance. In this blog, we will delve into why M2 tool steel is perfect for high-speed tools, covering its properties, benefits, and practical applications. We will also provide a comprehensive guide on how to work with and maintain M2 tool steel to achieve optimal results.
What Is M2 Tool Steel?
M2 tool steel, also known as molybdenum high-speed steel, is a type of tool steel alloy primarily used for high-speed cutting tools like drills, saw blades, and end mills. It comprises tungsten, molybdenum, chromium, and vanadium, which provide it with a unique combination of properties:
- High Hardness: M2 tool steel can achieve a hardness of up to 65-67 HRC, making it suitable for heavy-duty applications.
- Excellent Wear Resistance: It has a high resistance to abrasion, which extends the life of tools made from M2 tool steel.
- Toughness and Flexibility: Despite its hardness, M2 tool steel maintains sufficient toughness, reducing the risk of tool breakage.
Understanding these properties helps illustrate why M2 tool steel is the preferred choice for high-speed machining tools.
Key Benefits of M2 Tool Steel for High-Speed Tools
M2 tool steel offers several benefits that make it ideal for high-speed applications. These include:
- Temperature Resistance: M2 tool steel retains its hardness even at high temperatures, which is crucial for high-speed operations where heat buildup is common.
- Versatility: Suitable for various cutting tools like drills, taps, and milling cutters, M2 tool steel provides flexibility in machining applications.
- Extended Tool Life: Due to its wear resistance, M2 tool steel tools have a longer lifespan, which helps in reducing replacement costs.
This section underscores why industries favor M2 tool steel for high-speed tools.
Properties of M2 Tool Steel: A Detailed Analysis
The properties of M2 tool steel make it stand out among other high-speed steels. Here, we present these properties in a table for clarity:
Property | Description |
---|---|
Hardness | Up to 65-67 HRC |
Wear Resistance | High, due to the presence of vanadium carbides |
Toughness | Retains toughness while being hard, suitable for impact |
Thermal Stability | Maintains hardness up to 600°C (1112°F) |
Machinability | Moderate; suitable for shaping and regrinding |
These properties enable M2 tool steel to withstand the demanding conditions of high-speed machining.
Applications of M2 Tool Steel in High-Speed Tools
M2 tool steel is utilized across various industries for high-speed cutting tools. Common applications include:
- Drills and Drill Bits: Due to its hardness and thermal resistance, M2 tool steel is ideal for making drills used in machining metal, wood, and plastic.
- End Mills: In milling operations, M2 tool steel end mills deliver precision and durability, even under high-speed conditions.
- Saw Blades: For cutting through different materials, M2 tool steel saw blades offer efficiency and longevity.
- Lathe Tools: M2 tool steel is also used for lathe cutting tools, providing excellent edge retention.
These applications demonstrate how M2 tool steel’s properties are put into practice in various high-speed operations.
Best Practices for Working with M2 Tool Steel
To maximize the performance of M2 tool steel in high-speed applications, follow these best practices:
- Heat Treatment: Proper heat treatment is essential for achieving the desired hardness and wear resistance in M2 tool steel tools.
- Cutting Fluids: Using the right cutting fluids helps maintain tool temperature and improves tool life.
- Regrinding and Maintenance: Regular regrinding of M2 tool steel tools can extend their life, ensuring consistent performance over time.
By adhering to these practices, users can get the most out of M2 tool steel and enhance their machining efficiency.
Heat Treatment of M2 Tool Steel: A Comprehensive Guide
Heat treatment is crucial for M2 tool steel, as it determines its hardness, toughness, and overall performance. The process includes several steps:
- Preheating: Heat the tool slowly to 450-500°C to reduce stress before reaching higher temperatures.
- Austenitizing: Heat the tool to 1200-1230°C for 20 minutes. This allows for the steel to transform into austenite.
- Quenching: Cool rapidly using air, oil, or salt bath to achieve maximum hardness.
- Tempering: Heat again to 560-600°C to reduce brittleness and improve toughness.
Heat Treatment Stage | Temperature Range (°C) | Purpose |
---|---|---|
Preheating | 450-500 | Reduces stress in the material |
Austenitizing | 1200-1230 | Transforms structure to austenite |
Quenching | Varies (air/oil/salt) | Rapid cooling for hardness |
Tempering | 560-600 | Reduces brittleness, adds toughness |
Proper heat treatment helps achieve optimal results when using M2 tool steel in high-speed tools, ensuring both hardness and durability.
Frequently Asked Questions (FAQ)
Q1: What makes M2 tool steel suitable for high-speed applications?
A1: M2 tool steel’s combination of high hardness, thermal stability, and wear resistance makes it ideal for high-speed tools that encounter intense heat and friction.
Q2: Can M2 tool steel be used for woodworking tools?
A2: Yes, M2 tool steel is versatile and can be used for woodworking tools like saw blades and router bits due to its toughness and wear resistance.
Q3: How can I increase the lifespan of M2 tool steel tools?
A3: Regular maintenance, regrinding, and using appropriate cutting fluids are key to extending the lifespan of M2 tool steel tools.
Q4: Is M2 tool steel easy to machine?
A4: M2 tool steel has moderate machinability. Using suitable cutting techniques and fluids can improve efficiency when working with it.
Conclusion
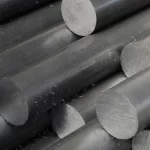
M2 tool steel is a premier choice for high-speed tools, providing a blend of hardness, toughness, and thermal stability. By understanding its properties, applications, and best practices for use, industries can leverage its strengths to enhance machining processes. From drills to saw blades, M2 tool steel’s versatility ensures it remains a top option for high-speed operations. When treated and maintained correctly, tools made from M2 tool steel offer longevity, efficiency, and reliability.