Welcome to My Blog! 🌟
Before we dive into the content, I’d love for you to join me on my social media platforms. It’s where I share more insights, engage with our vibrant community, and post regular updates. Here’s how you can stay connected:
📘 Facebook: Connect with me on Facebook
Now, let’s embark on this journey together. I hope you find the content here insightful, engaging, and most importantly, valuable. Let’s explore, learn, and grow together! 🚀
Table of Contents
Introduction
M2 steel is a highly regarded material in the tool-making industry, particularly for high-precision applications. Renowned for its exceptional properties, M2 steel has become the go-to choice for manufacturing cutting tools and dies that require superior wear resistance, high-temperature stability, and toughness. This blog post will explore the features of M2 steel and why it is the ultimate solution for high-precision tools, with a focus on its composition, benefits, and applications. Additionally, we will take a closer look at the role of Shandong Qilu Industrial Co., Ltd. in providing this high-performance material to customers worldwide.
What is M2 Steel?
M2 steel, also known as AISI M2, is a molybdenum-based high-speed steel (HSS) in the tungsten–molybdenum series. It is widely recognized for its versatility in cutting applications, including twist drills, taps, milling cutters, and saw blades. The material’s balanced combination of toughness, wear resistance, and red hardness makes it ideal for high-speed and light cutting operations. M2 steel is commonly used in applications requiring precision and durability, such as cold work punches, dies, and cutting tools.
Key Properties of M2 Steel
M2 steel’s chemical composition and physical properties make it an exceptional choice for high-precision tool manufacturing. Let’s dive into the specific properties that make M2 steel stand out in the market.
Chemical Composition
The chemical composition of M2 steel is a critical factor in its performance. M2 contains:
Element | Content |
---|---|
Carbon (C) | 0.78% – 0.88% |
Manganese (Mn) | 0.15% – 0.40% |
Silicon (Si) | 0.20% – 0.45% |
Sulfur (S) | ≤ 0.030% |
Phosphorus (P) | ≤ 0.030% |
Chromium (Cr) | 3.75% – 4.50% |
Molybdenum (Mo) | 4.50% – 5.50% |
Vanadium (V) | 1.75% – 2.20% |
Tungsten (W) | 5.50% – 6.75% |
Nickel (Ni) | ≤ 0.30% |
The combination of these elements gives M2 steel its remarkable properties, including excellent hardness, wear resistance, and the ability to maintain its hardness at high temperatures.
Mechanical Properties
The mechanical properties of M2 steel are a key reason why it is highly suitable for use in high-precision tools. These properties include a balanced combination of hardness, strength, toughness, wear resistance, and thermal stability, all of which contribute to the material’s excellent performance under demanding conditions.
- Hardness: One of the standout features of this material is its remarkable hardness. After undergoing the quenching process, M2 achieves a hardness range between 62-66 HRC. This makes it incredibly durable and capable of maintaining its sharpness even in high-stress environments.
- Strength: M2 boasts impressive tensile strength, with a value of around 1800 MPa. This high tensile strength ensures that the material is strong enough to withstand significant stress and pressure, making it ideal for demanding applications that require reliable and consistent performance.
- Toughness: M2 exhibits superior impact toughness, with values ranging from 0.18 to 0.32 MJ/m². Compared to many other high-speed steels, it offers enhanced toughness, enabling it to absorb and withstand impacts without cracking or failing. This quality makes it highly effective for tools that need to endure frequent impact loads.
- Wear Performance: The material’s ability to resist wear is one of the factors that sets it apart from other tool steels. M2 ’s wear resistance is exceptional, allowing it to perform well in tools and dies that experience constant abrasion. Whether used in cutting operations or high-stress mechanical environments, its wear resistance ensures longevity and reliability.
- Thermal Stability: Another critical advantage of M2 is its thermal stability. The material can maintain its hardness at elevated temperatures of up to 600°C, making it an excellent choice for high-temperature cutting operations. This characteristic ensures that tools made from M2 can continue to perform effectively, even in extreme heat environments.
These properties make M2 steel one of the best choices for precision tooling, especially where durability and performance are critical.
Applications of M2 Steel in High-Precision Tools
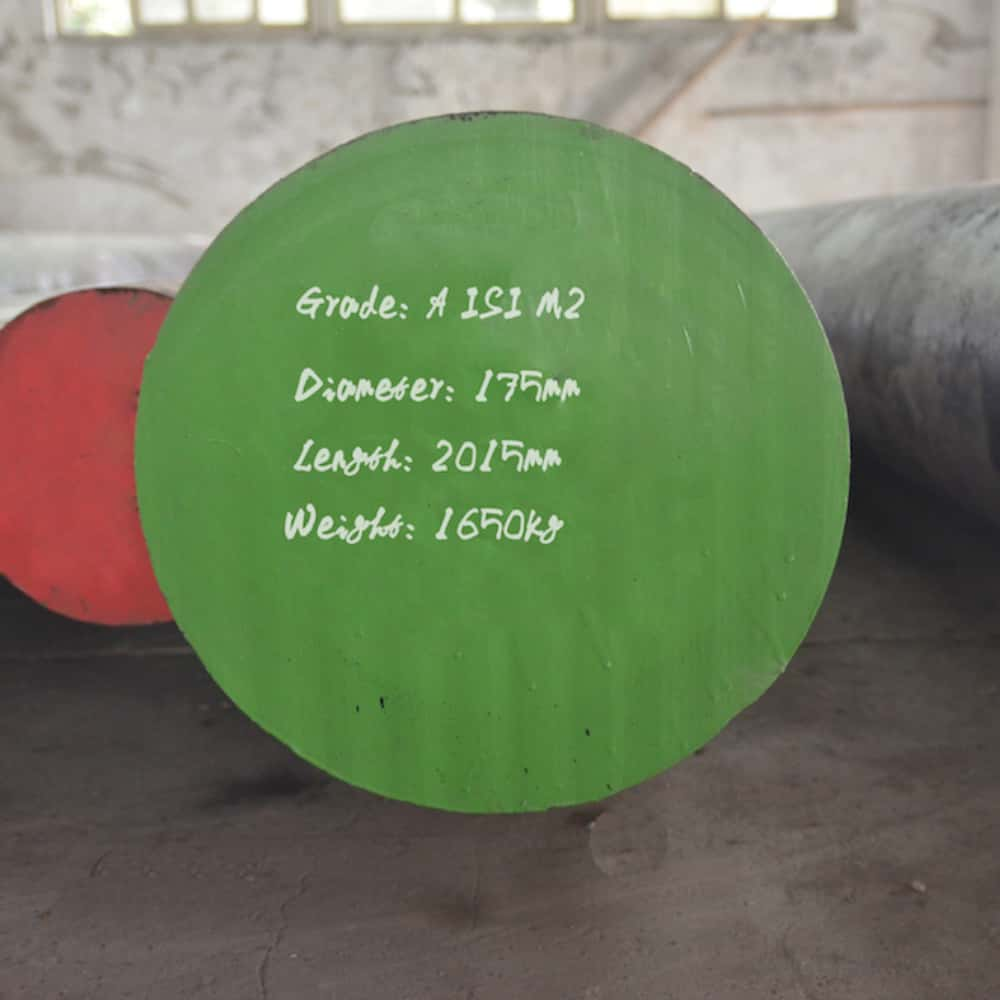
The versatility of this material is clearly demonstrated in its wide array of applications, especially in high-precision tools that demand exceptional performance in various challenging environments. Below are some of the most common uses:
Cutting Tools
M2 is widely used in the manufacturing of cutting tools, including twist drills, milling cutters, and saw blades. These tools require a material that can endure high-speed cutting operations without compromising performance. The exceptional wear resistance of M2 ensures that tools remain sharp and effective even after prolonged use. Its ability to maintain cutting performance over time is critical in industries such as manufacturing and construction.
Punches and Dies
The material is also frequently employed in the production of cold work punches and dies. These tools must be capable of withstanding intense wear and impact, making M2 an ideal choice. Its high toughness and excellent thermal stability allow punches and dies to endure extreme pressure and temperature fluctuations. This capability is particularly beneficial in precision applications such as stamping, molding, and cutting in heavy machinery industries.
Knives and Blades
M2 is used extensively for manufacturing knives and blades, where both sharpness and wear resistance are essential qualities. Whether in industrial settings, where precision and reliability are critical, or in consumer products, M2 ensures that knives and blades maintain their cutting edge for extended periods. The material’s resistance to wear guarantees that these tools perform efficiently even after repeated use.
Why Choose M2 Steel for Your Precision Tooling Needs?
M2 stands out as an ideal material for high-precision tools, offering a combination of toughness, wear resistance, and thermal stability that makes it unparalleled in many demanding applications. Compared to other tool steels, it offers a unique balance of durability, cost-effectiveness, and performance, making it the preferred choice for a wide range of industries that require tools capable of enduring extreme conditions.
- Long-Lasting Durability: One of the key reasons this material is favored in the production of precision tools is its exceptional durability. Thanks to its high hardness, this steel provides outstanding resistance to wear and tear, ensuring that tools maintain their performance over extended periods. The durability of these tools reduces the frequency of replacements, ultimately lowering operational costs for industries reliant on cutting-edge technology and heavy-duty machinery.
- High-Temperature Performance: This steel’s impressive ability to retain its hardness even at elevated temperatures makes it an excellent choice for high-speed cutting and machining operations. In industries where tools are exposed to intense heat, such as metalworking or automotive manufacturing, this property allows for reliable, consistent performance. The material’s thermal stability ensures that tools do not lose their hardness under high operational temperatures, making it a trusted choice in environments where heat resistance is critical.
- Superior Toughness: When compared to many other high-speed steels, this material offers superior toughness. It is designed to withstand significant impact forces, making it ideal for applications that require tools to absorb shocks or resist sudden stresses. Whether used in cold working tools or heavy-duty machinery, its impact toughness ensures that tools made from this material can endure harsh environments without compromising performance.
- Cost-Effectiveness: While many high-speed steels offer impressive properties, they often come at a high price. In contrast, M2 steel delivers comparable performance to premium materials like T1 steel but at a more affordable cost. This cost-effectiveness makes it an appealing choice for businesses looking to balance quality with budget. By choosing this material, manufacturers can provide durable, high-performing tools without incurring the steep costs associated with other premium tool steels.
About Shandong Qilu Industrial Co., Ltd.
Shandong Qilu Industrial Co., Ltd. is a leading manufacturer specializing in the production of high-quality tool steels, including M2, P20, H13, D2, and S7. As a wholly-owned subsidiary of Qilu Steel Group, we have accumulated extensive industry experience in the tool and die steel sector. Our team of experienced specialists focuses on the design, development, and manufacturing of tool steels tailored to meet the evolving needs of the market.
Qilu Tool Steel is committed to providing premium products that meet the highest standards of performance and reliability. We pride ourselves on driving innovation and optimizing our products to ensure the best results for our customers.
Conclusion
M2 steel is undeniably the ultimate solution for high-precision tools, offering a perfect balance of toughness, wear resistance, and thermal stability. Whether used in cutting tools, punches, dies, or knives, M2 steel delivers exceptional performance that ensures your tools last longer and work more efficiently. With Shandong Qilu Industrial Co., Ltd.’s extensive expertise and commitment to quality, you can trust us to provide the highest grade M2 steel for all your precision tooling needs.
FAQ
What is M2 steel best used for?
M2 steel is commonly used for cutting tools, punches, dies, and blades due to its excellent wear resistance, toughness, and high-temperature performance.
How does M2 steel compare to other tool steels?
M2 steel offers superior performance in terms of wear resistance, toughness, and thermal stability compared to other tool steels like T1.
Can M2 steel be used for high-temperature applications?
Yes, M2 steel maintains its hardness at temperatures up to 600°C, making it ideal for high-temperature cutting operations.
What is the hardness of M2 steel after quenching?
After quenching, M2 steel can achieve a hardness of 62-66 HRC.
Where can I purchase high-quality M2 steel?
High-quality M2 steel can be purchased from reputable manufacturers like Shandong Qilu Industrial Co., Ltd., which specializes in producing premium tool steels.