Introduction
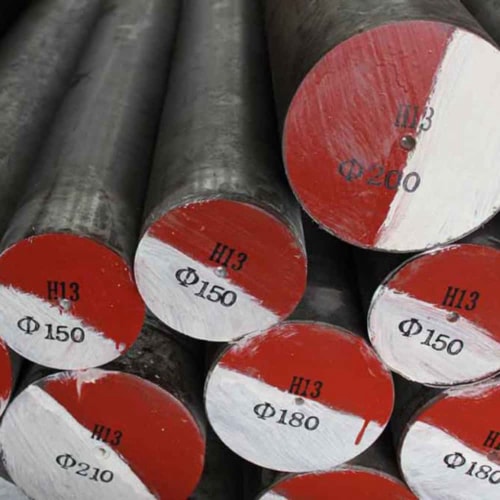
In the realm of tooling, material selection plays a pivotal role in determining the performance, durability, and cost-effectiveness of tools. Among the plethora of materials available, H13 round bar stands out as a paramount choice for various tooling applications. This article delves into the reasons why H13 round bar is indispensable in the tooling industry.
Understanding H13 Round Bar
H13 round bar, a type of hot-work tool steel, possesses exceptional properties that make it highly suitable for tooling applications. This section elucidates the key characteristics of H13 tool steel round bar, including its composition, mechanical properties, and heat treatment.
Applications of H13 Round Bar
H13 round bar’s versatility and exceptional properties make it a go-to choice across numerous sectors within the tooling industry. Let’s delve deeper into its extensive applications:
- Die Casting Dies: H13 round bar is widely utilized in the manufacturing of die casting dies due to its high heat resistance, thermal conductivity, and excellent hot strength. Die casting processes, which involve injecting molten metal into molds under high pressure, subject dies to extreme temperatures and mechanical stresses. H13 tool steel round bar’s ability to withstand these conditions while maintaining dimensional stability and wear resistance makes it an ideal material for die casting dies in various industries, including automotive, aerospace, and consumer electronics.
- Forging Tools: In forging operations, where metal is shaped through the application of localized compressive forces, the tooling must withstand significant impact and thermal shock. H13 tool steel round bar’s combination of high hardness, toughness, and heat resistance makes it well-suited for forging tools such as dies, punches, and hammers. Whether in closed-die forging, open-die forging, or hot forging processes, H13 round bar’s durability and machinability ensure optimal performance and longevity of forging tools.
- Extrusion Tooling: Extrusion is a manufacturing process that involves forcing material through a shaped die to create continuous profiles, such as pipes, rods, and tubes. H13 round tool steel bar’s superior thermal conductivity, wear resistance, and surface finish make it a preferred choice for extrusion tooling. Whether in hot extrusion of metals or cold extrusion of plastics, H13 round tool steel bar’s ability to withstand high temperatures and resist wear ensures precise shaping and consistent quality of extruded products.
- Plastic Molding Components: Plastic molding processes, including injection molding and blow molding, rely on precision molds to shape molten plastic into desired forms. H13 tool steel round bar’s excellent machinability, corrosion resistance, and thermal stability make it an ideal material for manufacturing injection molds, extrusion dies, and other plastic molding components. Its ability to maintain dimensional accuracy and withstand prolonged use under high temperatures and pressures ensures the production of high-quality plastic parts across various industries, including packaging, automotive, and consumer goods.
- Cutting and Forming Tools: Beyond specialized tooling applications, H13 tool steel round bar is also employed in the fabrication of cutting and forming tools used in machining, stamping, and shearing operations. Its high hardness, abrasion resistance, and edge retention make it suitable for producing tool bits, blades, and inserts that withstand the rigors of metalworking processes. Whether in CNC machining, sheet metal stamping, or metal forming, H13 round bar’s reliability and performance contribute to improved efficiency and precision in manufacturing operations.
In essence, H13 round bar’s versatility and adaptability make it an indispensable material across a wide spectrum of tooling applications, enabling manufacturers to achieve superior performance, efficiency, and quality in their processes.
Case Studies: Performance in Real-world Scenarios
Illustrating the efficacy of H13 round bar in real-world scenarios through case studies further underscores its significance in the tooling industry. This section presents notable case studies highlighting the exceptional performance and reliability of H13 round bar in different tooling applications.
Advantages of H13 Round Bar
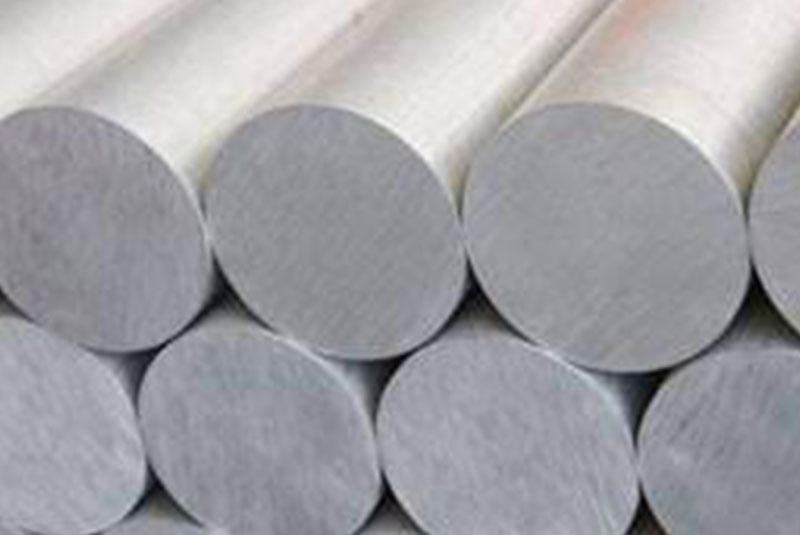
The advantages offered by H13 round bar are manifold, ranging from high hardness and wear resistance to excellent thermal conductivity and machinability. This section explores in detail the advantages that make H13 round bar a preferred choice for tooling purposes.
Properties | Description |
---|---|
Hardness | High hardness ensures prolonged tool life |
Wear Resistance | Resists wear even under high-stress conditions |
Thermal Conductivity | Efficiently dissipates heat during operation |
Machinability | Facilitates ease of machining and tool fabrication |
FAQ
Q:What is H13 round bar, and why is it preferred in the tooling industry?
A:H13 round bar is a type of hot-work tool steel renowned for its exceptional properties, including high hardness, wear resistance, and thermal conductivity. It is preferred in the tooling industry due to its ability to withstand high temperatures, resist wear under demanding conditions, and facilitate efficient heat dissipation.
Q:How does the composition of H13 round bar contribute to its performance?
A:The composition of H13 round bar, characterized by elements such as chromium, molybdenum, vanadium, and carbon, imparts unique properties to the material. Chromium enhances hardenability and corrosion resistance, while molybdenum and vanadium contribute to strength and toughness. Carbon content ensures high hardness and wear resistance.
Q:What are the typical applications of H13 round bar in the tooling industry?
A:H13 round bar finds extensive applications in various tooling processes, including die casting, forging, extrusion, plastic molding, and more. Its versatility and superior properties make it suitable for manufacturing dies, punches, inserts, molds, and other tooling components subjected to high temperatures and mechanical stress.
Q:How does heat treatment affect the properties of H13 tool steel round bar?
A:Heat treatment plays a crucial role in optimizing the properties of H13 tool steel round bar to meet specific application requirements. Processes such as annealing, hardening, tempering, and stress relieving are employed to achieve desired hardness, toughness, and dimensional stability, enhancing the performance and longevity of tooling components.
Q:What considerations should be taken into account when machining H13 round bar?
A:Machining H13 round bar requires careful consideration of factors such as cutting speed, feed rate, tool geometry, and coolant usage. Proper machining practices help prevent tool wear, maintain dimensional accuracy, and ensure surface finish quality, maximizing the efficiency and productivity of tooling operations.
Q:Is H13 round bar cost-effective compared to other tooling materials?
A:While the initial cost of H13 tool steel round bar may be higher than some alternative materials, its superior performance, extended tool life, and reduced downtime often result in long-term cost savings for tooling applications. Additionally, the versatility and reliability of H13 tool steel round bar justify its investment in various industrial settings.
Conclusion
In conclusion, H13 round bar emerges as a cornerstone material in the tooling industry, offering a unique blend of superior properties and versatility. Its widespread adoption across various tooling applications underscores its crucial role in enhancing productivity, efficiency, and cost-effectiveness. With its exceptional performance and reliability, H13 round bar continues to shape the landscape of tooling, ensuring optimal outcomes for diverse industrial endeavors.
With this comprehensive understanding of why H13 tool steel round bar is crucial in the tooling industry, manufacturers and professionals can make informed decisions, leveraging its unparalleled benefits to drive innovation and success.