Welcome to My Blog!
Before we dive into the content, I’d love for you to join me on my social media platforms where I share more insights, engage with the community, and post updates. Here’s how you can connect with me:
Facebook:https://www.facebook.com/profile.php?id=100087990137347
LinkedIn:https://www.linkedin.com/company/89825762/admin/dashboard/
YouTube:www.youtube.com/@carbonsteelsupply-kj9lw
TikTok:www.tiktok.com/@carbonsteelsupply
Now, let’s get started on our journey together. I hope you find the content here insightful, engaging, and valuable.
Introduction
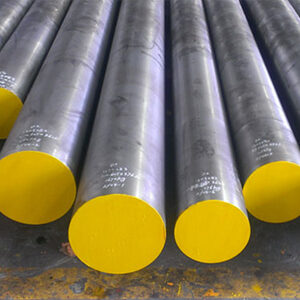
When it comes to selecting the best material for knives and cutting tools, M4 tool steel stands out as a popular choice among professionals and hobbyists alike. Known for its exceptional strength, edge retention, and wear resistance, M4 tool steel offers a combination of properties that make it ideal for demanding applications. In this blog, we will explore why M4 tool steel is a top choice for knives and cutting tools, diving into its characteristics, advantages, and practical uses.
What Is M4 Tool Steel?
M4 tool steel is a high-speed steel known for its impressive toughness and durability. It belongs to the M-series of tool steels, which are specifically engineered to withstand extreme conditions. M4 tool steel contains high levels of carbon, vanadium, molybdenum, and tungsten, making it an excellent option for cutting tools that require high wear resistance and the ability to maintain a sharp edge for extended periods.
Key Elements in M4 Tool Steel
Element | Percentage (%) | Function |
---|---|---|
Carbon (C) | 1.4-1.65 | Increases hardness and wear resistance |
Vanadium (V) | 3.75-4.5 | Enhances strength and edge retention |
Molybdenum (Mo) | 4.75-5.5 | Improves toughness and high-temperature strength |
Tungsten (W) | 5.5-6.75 | Boosts hardness and resistance to deformation |
This composition contributes to M4 tool steel’s exceptional properties, which include superior edge retention and toughness, making it a preferred material for high-performance cutting tools and knives.
Advantages of Using M4 Tool Steel in Knives
Superior Edge Retention
One of the most significant advantages of M4 tool steel is its exceptional edge retention. The combination of vanadium and tungsten in its composition provides a fine grain structure, allowing knives and cutting tools to maintain a sharp edge even after extended use. This is particularly important for chefs, craftsmen, and other professionals who rely on the performance of their blades in critical applications.
High Wear Resistance
The high carbon content in M4 tool steel contributes to its wear resistance, making it suitable for applications that involve frequent cutting and abrasive materials. This characteristic ensures that M4 tool steel knives can endure tough conditions without becoming dull or damaged quickly.
Toughness and Durability
In addition to edge retention and wear resistance, M4 tool steel is renowned for its toughness. This toughness allows it to withstand impact without chipping or breaking, which is crucial in heavy-duty cutting tools. Knives made from M4 tool steel are less likely to experience structural damage, providing long-term reliability and performance.
Applications of M4 Tool Steel in Cutting Tools
M4 tool steel is highly versatile and can be used in various cutting tools beyond knives. Its properties make it suitable for:
- Industrial Blades: Ideal for high-speed cutting applications where edge retention and durability are critical.
- Drill Bits and Milling Cutters: Used in machining and manufacturing processes due to its toughness and wear resistance.
- Woodworking Tools: Popular in woodworking due to its ability to maintain sharpness and resist damage from impact or abrasive surfaces.
- Survival Knives: Preferred in outdoor and survival gear for its reliable performance under extreme conditions.
Heat Treatment Process for M4 Tool Steel
The performance of M4 tool steel can be further optimized through the heat treatment process. Proper heat treatment increases the hardness, toughness, and wear resistance of the steel. Here’s an overview of the typical heat treatment process:
Process Step | Temperature Range (°C) | Description |
---|---|---|
Preheating | 450-500 | Gradually heating the steel to reduce stress |
Austenitizing | 1100-1200 | Heating to a high temperature to form austenite |
Quenching | Oil or air quenching | Cooling rapidly to harden the steel |
Tempering | 500-600 | Reheating to achieve the desired balance of hardness and toughness |
By carefully controlling the heat treatment process, manufacturers can enhance the performance of M4 tool steel, ensuring that it meets the demands of various cutting applications.
Maintenance Tips for M4 Tool Steel Knives
To maximize the lifespan and performance of M4 tool steel knives, proper maintenance is essential. Here are some tips:
- Regular Sharpening: Although M4 tool steel holds its edge for a long time, occasional sharpening is necessary to maintain its optimal performance.
- Prevent Rusting: While M4 tool steel is not stainless, it can resist rust if properly cared for. Applying a thin layer of oil after cleaning can help prevent corrosion.
- Avoid High Impact: Although tough, avoiding heavy impacts or dropping the knife on hard surfaces can prevent chipping or structural damage.
Comparisons: M4 Tool Steel vs. Other Tool Steels
When choosing the best steel for knives and cutting tools, it’s helpful to understand how M4 tool steel compares to other popular tool steels.
Property | M4 Tool Steel | D2 Tool Steel | S30V Tool Steel |
---|---|---|---|
Hardness (HRC) | 62-64 | 59-61 | 58-61 |
Toughness | High | Medium | High |
Edge Retention | Excellent | Good | Excellent |
Corrosion Resistance | Low | Medium | High |
Applications | Knives, industrial tools | Knives, punches | Premium knives |
This comparison shows that M4 tool steel excels in hardness, toughness, and edge retention but may require extra care due to its lower corrosion resistance compared to some other high-end tool steels.
Frequently Asked Questions (FAQ)
Q1: Is M4 Tool Steel Good for Knives?
Yes, M4 tool steel is an excellent choice for knives, especially those used in demanding environments. Its high hardness, wear resistance, and edge retention capabilities make it suitable for both professional and survival knives.
Q2: Does M4 Tool Steel Rust Easily?
M4 tool steel is not stainless and therefore can rust if not properly maintained. However, with proper care—such as applying oil and avoiding exposure to moisture—it can maintain its integrity and performance.
Q3: How Do You Sharpen M4 Tool Steel Knives?
Sharpening M4 tool steel knives can be done using diamond or ceramic sharpening stones, as these materials are capable of cutting through its tough and hard surface effectively.
Q4: Can M4 Tool Steel Be Used for Woodworking Tools?
Absolutely, M4 tool steel is a great option for woodworking tools due to its toughness and edge retention. Its ability to withstand impact and resist wear makes it a reliable choice for high-speed woodworking applications.
Conclusion
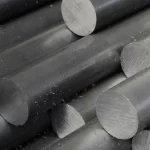
In conclusion, M4 tool steel is a premium material for knives and cutting tools, offering exceptional hardness, toughness, and wear resistance. Its composition and properties make it ideal for various demanding applications, from industrial blades to survival knives. While it does require proper maintenance to prevent rust, the benefits far outweigh this minor drawback.
By understanding the characteristics, applications, and maintenance tips for M4 tool steel, you can make an informed decision on whether this steel is the best option for your cutting tools. Whether you are a professional craftsman, chef, or outdoor enthusiast, investing in M4 tool steel guarantees long-term performance and reliability.