Welcome to My Blog!
Before we dive into the content, I’d love for you to join me on my social media platforms where I share more insights, engage with the community, and post updates. Here’s how you can connect with me:
Facebook:https://www.facebook.com/profile.php?id=100090797846538
Now, let’s get started on our journey together. I hope you find the content here insightful, engaging, and valuable.
Table of Contents
Introduction
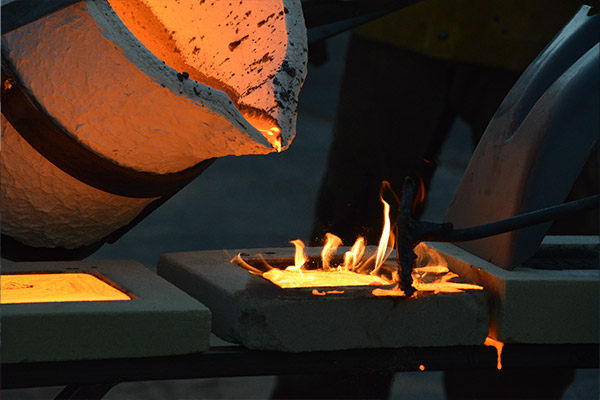
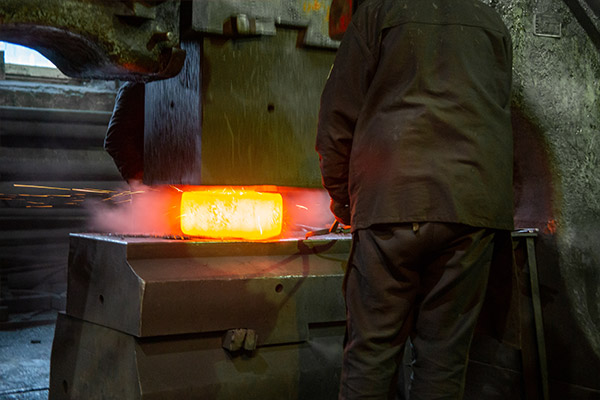
When it comes to the longevity and performance of tool steels, the heat treatment process plays a pivotal role. Among the various tool steels available, A2 tool steel is renowned for its excellent wear resistance, toughness, and dimensional stability. However, to unlock its full potential, proper a2 tool steel heat treat procedures are essential. This blog delves into the importance of heat treating A2 tool steel, exploring the science behind it, the steps involved, and the benefits it brings to the table.
Understanding A2 Tool Steel
Before diving into the specifics of a2 tool steel heat treat, it’s crucial to understand what A2 tool steel is and why it’s so widely used. A2 tool steel is an air-hardening, medium-alloy tool steel that contains chromium and molybdenum. These elements contribute to its hardness, wear resistance, and ability to retain shape under stress. A2 tool steel is commonly used in applications such as die making, punches, and industrial cutting tools, where durability and precision are paramount.
Composition of A2 Tool Steel
The composition of A2 tool steel includes:
- Carbon: 1.0%
- Manganese: 0.6%
- Chromium: 5.0%
- Molybdenum: 1.0%
- Vanadium: 0.2%
This specific blend of elements gives A2 tool steel its unique properties, making it a preferred choice for demanding applications.
The Science Behind A2 Tool Steel Heat Treat
Heat treatment is a controlled process used to alter the physical and mechanical properties of a material. For A2 tool steel, the heat treat process involves heating the steel to a specific temperature, holding it at that temperature for a predetermined time, and then cooling it at a controlled rate. This process transforms the microstructure of the steel, enhancing its hardness, toughness, and overall performance.
Phases of Heat Treatment
The a2 tool steel heat treat process typically involves three main phases:
- Austenitizing: Heating the steel to a temperature where its microstructure transforms into austenite.
- Quenching: Rapidly cooling the steel to lock in the austenitic structure, forming martensite.
- Tempering: Reheating the steel to a lower temperature to reduce brittleness and improve toughness.
Each phase plays a critical role in determining the final properties of the A2 tool steel.
Steps in A2 Tool Steel Heat Treat
To achieve the desired properties, the a2 tool steel heat treat process must be meticulously followed. Here are the detailed steps involved:
Preheating
Before austenitizing, the steel is preheated to reduce thermal shock and ensure uniform heating. Preheating is typically done at temperatures between 1200°F to 1400°F (649°C to 760°C).
Austenitizing
The steel is then heated to the austenitizing temperature, which is around 1750°F to 1850°F (954°C to 1010°C) for A2 tool steel. Holding the steel at this temperature allows the carbon to dissolve into the austenite, creating a uniform structure.
Quenching
After austenitizing, the steel is rapidly cooled, usually by air quenching. Air quenching is preferred for A2 tool steel because it minimizes the risk of distortion and cracking compared to oil or water quenching.
Tempering
Tempering is the final step, where the steel is reheated to a temperature between 350°F to 1100°F (177°C to 593°C). This process reduces the brittleness of the martensite formed during quenching and enhances the steel’s toughness. The exact tempering temperature depends on the desired hardness and application.
Benefits of Proper A2 Tool Steel Heat Treat
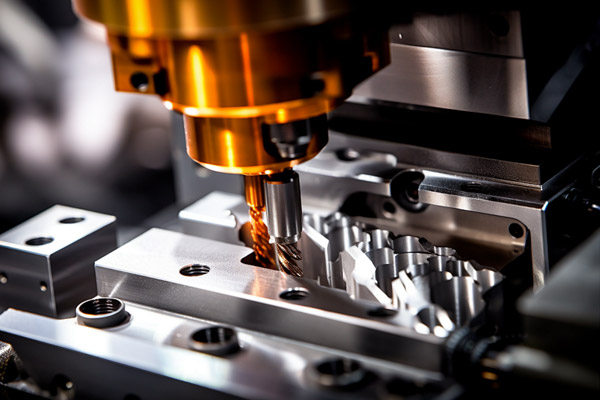
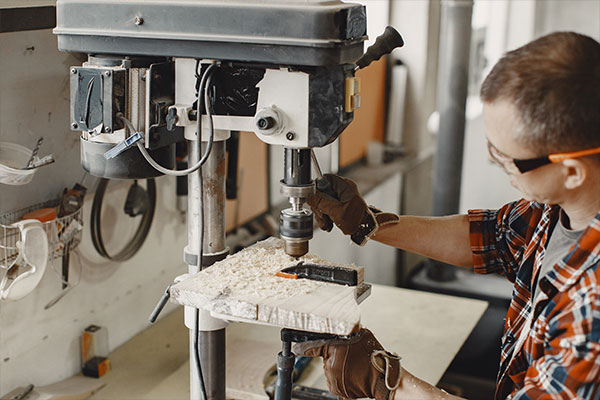
Properly heat treating A2 tool steel offers numerous benefits, making it a crucial step in ensuring the longevity and performance of the material.
Enhanced Hardness and Wear Resistance
The primary benefit of a2 tool steel heat treat is the significant increase in hardness. This hardness translates to improved wear resistance, allowing tools made from A2 steel to withstand prolonged use without significant wear.
Improved Toughness
While hardness is essential, toughness is equally important, especially in applications where the tool may be subjected to impact or shock loading. Tempering after quenching enhances the toughness of A2 tool steel, reducing the risk of cracking or breaking under stress.
Dimensional Stability
Heat treating A2 tool steel ensures dimensional stability, meaning the tool will retain its shape and size even under extreme conditions. This stability is crucial in precision applications where even minor distortions can lead to significant issues.
Extended Tool Life
By enhancing hardness, toughness, and dimensional stability, proper a2 tool steel heat treat significantly extends the life of tools. This extension translates to cost savings, as tools need to be replaced less frequently.
Consistent Performance
Heat-treated A2 tool steel offers consistent performance, ensuring that the tool behaves predictably under various conditions. This consistency is vital in industrial applications where reliability is paramount.
A2 Tool Steel Heat Treat Parameters
To achieve the desired properties, it’s essential to follow specific heat treat parameters. Below is a table summarizing the key parameters for a2 tool steel heat treat.
Parameter | Temperature Range | Holding Time | Cooling Method |
---|---|---|---|
Preheating | 1200°F to 1400°F (649°C to 760°C) | 30 minutes per inch of thickness | Air or furnace cooling |
Austenitizing | 1750°F to 1850°F (954°C to 1010°C) | 30 minutes per inch of thickness | Air quenching |
Tempering | 350°F to 1100°F (177°C to 593°C) | 1 to 2 hours | Air cooling |
These parameters ensure that the a2 tool steel heat treat process is carried out effectively, resulting in a material with the desired properties.
Common Mistakes in A2 Tool Steel Heat Treat
While the a2 tool steel heat treat process is well-established, certain mistakes can compromise the final properties of the steel. Here are some common pitfalls to avoid:
Incorrect Austenitizing Temperature
Heating the steel to an incorrect austenitizing temperature can lead to incomplete transformation or excessive grain growth, both of which can negatively impact the steel’s properties.
Inadequate Holding Time
Holding the steel at the austenitizing temperature for too short a time can result in incomplete carbon dissolution, leading to uneven hardness and reduced wear resistance.
Improper Quenching
Using an incorrect quenching method, such as oil or water quenching for A2 tool steel, can cause excessive stress, leading to distortion or cracking.
Insufficient Tempering
Failing to temper the steel adequately can leave it too brittle, increasing the risk of cracking under stress. It’s essential to temper the steel to the correct temperature and hold it for the appropriate time.
Applications of Heat-Treated A2 Tool Steel
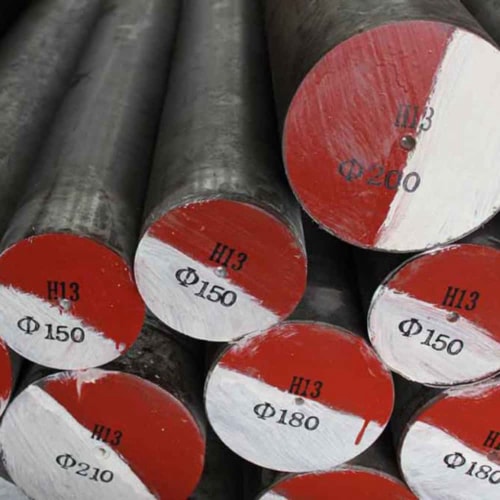
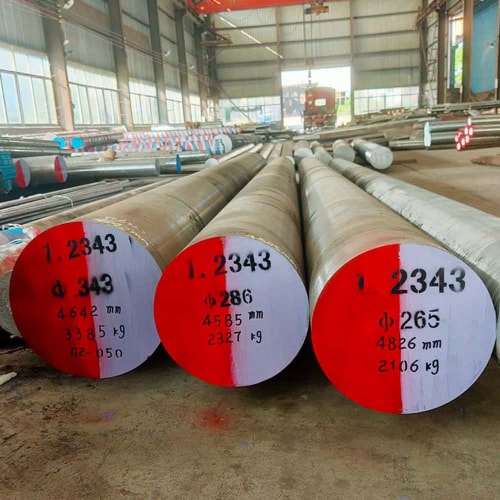
The enhanced properties of heat-treated A2 tool steel make it suitable for a wide range of applications. Here are some common uses:
Die Making
A2 tool steel is widely used in die making due to its excellent wear resistance and dimensional stability. Heat-treated A2 steel dies can withstand the rigors of high-volume production, ensuring consistent quality.
Punches
Punches made from heat-treated A2 tool steel offer superior hardness and toughness, making them ideal for piercing and forming operations. The extended tool life reduces downtime and maintenance costs.
Industrial Cutting Tools
Industrial cutting tools, such as blades and shears, benefit from the enhanced properties of heat-treated A2 tool steel. The increased hardness and wear resistance ensure that the tools maintain their cutting edge over extended periods.
Gages and Fixtures
Gages and fixtures made from heat-treated A2 tool steel offer excellent dimensional stability, ensuring accurate measurements and consistent performance in precision applications.
Conclusion
In conclusion, the a2 tool steel heat treat process is a critical step in ensuring the longevity and performance of A2 tool steel. By following the proper procedures and avoiding common mistakes, manufacturers can unlock the full potential of this versatile material. The enhanced hardness, toughness, and dimensional stability achieved through heat treating make A2 tool steel an excellent choice for a wide range of demanding applications. Whether you’re involved in die making, punch production, or industrial cutting, investing in proper heat treatment will pay dividends in the form of extended tool life and consistent performance.
FAQ
What is the purpose of heat treating A2 tool steel?
The purpose of heat treating A2 tool steel is to enhance its hardness, toughness, and dimensional stability, ensuring it performs well in demanding applications and has a long service life.
Can A2 tool steel be heat treated at home?
While it is possible to heat treat A2 tool steel at home, it requires precise control over temperature and cooling rates. For best results, it’s recommended to use professional heat treatment services.
How does tempering affect A2 tool steel?
Tempering reduces the brittleness of A2 tool steel after quenching, improving its toughness and reducing the risk of cracking under stress.
What is the difference between air quenching and oil quenching?
Air quenching involves cooling the steel in still air, while oil quenching involves immersing the steel in oil. Air quenching is preferred for A2 tool steel as it minimizes the risk of distortion and cracking.
How long does the heat treatment process take?
The duration of the heat treatment process depends on the thickness of the steel and the specific parameters used. Typically, it can take several hours, including preheating, austenitizing, quenching, and tempering.