Introduction
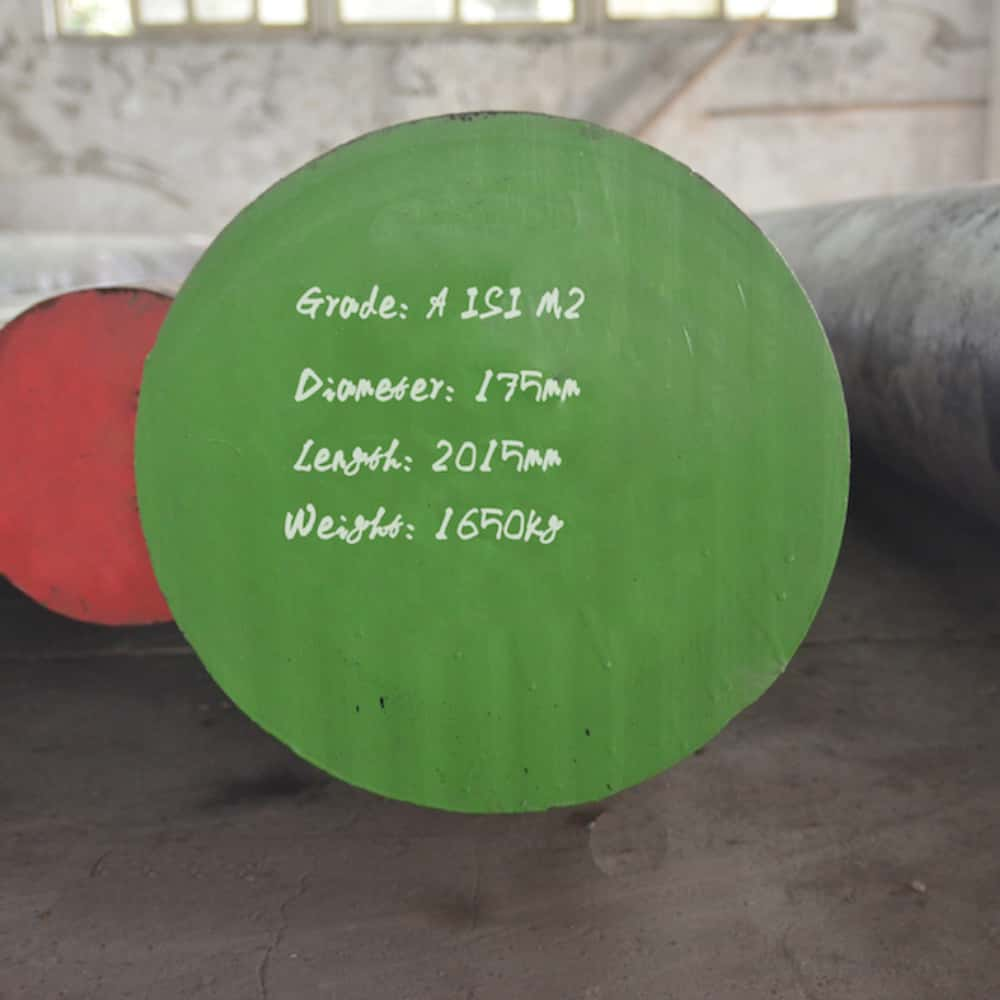
High-speed steel (HSS) stands as a cornerstone in the realm of industrial tooling, heralding a new era of efficiency and precision across diverse sectors. Its advent has brought about a paradigm shift, elevating cutting, drilling, and machining operations to unprecedented levels of performance. In this comprehensive guide, we embark on an enlightening journey into the intricate world of high-speed steel, unravelling its nuanced composition, multifaceted applications, unparalleled advantages, and essential maintenance insights. By delving deep into the essence of HSS, we aim to equip professionals and enthusiasts alike with a profound understanding of this remarkable alloy, empowering them to harness its full potential and usher in a new era of innovation and productivity.
Understanding High Speed Steel: Composition and Properties
High speed steel is an alloy comprising various elements such as tungsten, molybdenum, chromium, and vanadium. These elements contribute to its remarkable hardness, wear resistance, and heat resistance properties, making it an ideal choice for demanding industrial applications. Below is a table summarizing the composition of typical high-speed steel grades:
Element | Composition (%) |
---|---|
Tungsten (W) | 12-18 |
Molybdenum (Mo) | 2-10 |
Chromium (Cr) | 3-5 |
Vanadium (V) | 1-5 |
Carbon (C) | 0.7-1.2 |
Advantages of High Speed Steel
High speed steel (HSS) stands as a beacon of superiority amidst the landscape of conventional tool materials, boasting a myriad of advantages that propel it to the forefront of industrial applications.
- Exceptional Hardness and Wear Resistance: At the core of HSS lies its exceptional hardness, a quality that bestows upon it the ability to withstand the most rigorous of machining conditions. This inherent hardness, coupled with its remarkable wear resistance, ensures prolonged tool life, reducing the frequency of tool replacements and resulting in substantial cost savings for manufacturers. Whether facing abrasive materials or high-speed cutting operations, HSS stands resilient, delivering consistent performance over extended periods.
- Enhanced Machining Efficiency: The unparalleled hardness and wear resistance of HSS translate directly into enhanced machining efficiency, driving productivity to new heights. By maintaining sharp cutting edges for extended durations, HSS tools facilitate smoother, more precise machining processes, minimizing the need for frequent interruptions and tool changes. This seamless continuity in operation not only boosts throughput but also improves surface finish quality, elevating the overall standard of manufactured components.
- High Temperature Stability: One of the hallmark features of HSS is its ability to retain hardness and integrity even under the most blistering of operating temperatures. Unlike traditional tool materials that may succumb to thermal degradation, HSS stands firm, maintaining its cutting edge sharpness and dimensional stability throughout prolonged machining sessions. This resilience in the face of heat ensures consistent performance in demanding machining environments, where temperatures can soar to extreme levels.
- Versatility Across Applications: HSS’s versatility knows no bounds, as it finds application across a diverse spectrum of industries and machining operations. From precision cutting in the aerospace sector to high-speed drilling in automotive manufacturing, HSS adapts seamlessly to varying requirements, demonstrating its adaptability and reliability across the board. Its compatibility with a wide range of materials further enhances its appeal, making it the tool material of choice for an array of machining tasks.
- Cost-Effectiveness: While HSS may initially appear as a premium option compared to conventional tool materials, its exceptional longevity and performance swiftly justify the investment. The extended tool life afforded by HSS translates into reduced downtime, lower tooling costs, and enhanced overall efficiency, ultimately delivering a superior return on investment. In the long run, the cost-effectiveness of HSS becomes unmistakably apparent, positioning it as a sound strategic choice for forward-thinking manufacturers.
Maintenance and Care of High Speed Steel Tools
Proper maintenance is crucial to prolonging the lifespan and performance of high-speed steel tools. Regular inspection for wear and damage, along with appropriate lubrication during use, can significantly enhance tool longevity. Additionally, storing tools in a clean, dry environment and avoiding exposure to corrosive agents are essential practices for preserving their integrity.
Applications of High Speed Steel
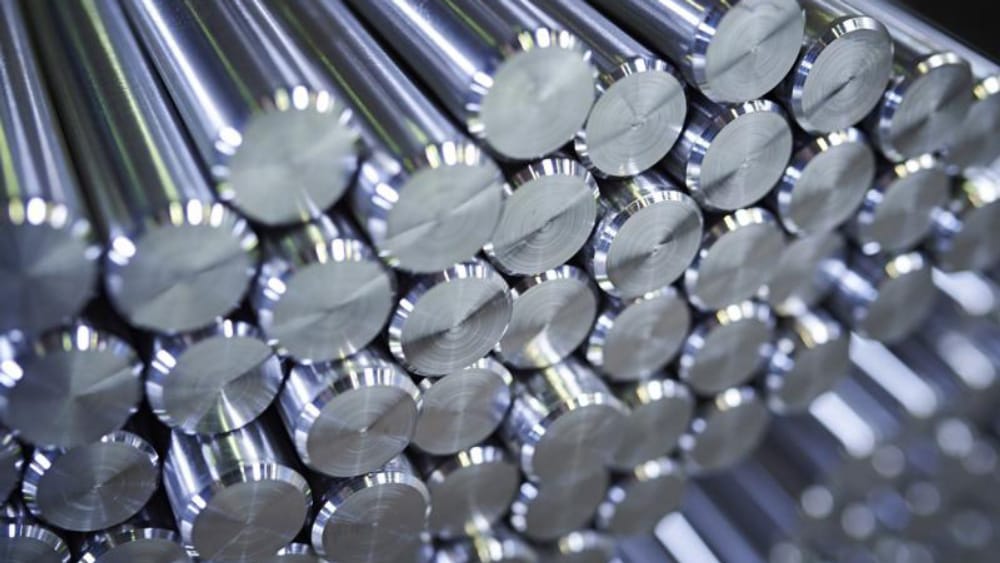
High speed steel finds widespread usage across various industries, including automotive, aerospace, and manufacturing. Its versatility allows for the fabrication of cutting tools, drills, taps, and dies. The table below highlights common applications of high-speed steel and the corresponding grades preferred in each application:
Application | Preferred HSS Grade |
---|---|
Cutting Tools | M2, M35, M42 |
Drills | M2, M7 |
Taps | M35, M42 |
Dies | M2, M3 |
Conclusion
High speed steel continues to play a pivotal role in advancing industrial productivity and efficiency. Its exceptional properties make it indispensable in various machining applications, offering superior performance and durability. By understanding its composition, applications, and maintenance requirements, manufacturers can unlock the full potential of high-speed steel, achieving optimal results in their machining operations.
FAQ
Q:What are the key characteristics of high-speed steel?
A:High speed steel exhibits exceptional hardness, wear resistance, and heat resistance properties, making it ideal for cutting, drilling, and machining applications.
Q:How does high-speed steel compare to other tool materials?
A:Compared to conventional tool materials such as carbon steel or carbide, high-speed steel offers superior hardness, toughness, and heat resistance, resulting in extended tool life and enhanced machining performance.
Q:What are the common grades of high-speed steel available in the market?
A:Some of the common grades of high-speed steel include M2, M35, and M42, each tailored to specific applications based on their composition and properties.
Q:How can I maintain high-speed steel tools for optimal performance?
A:Regular inspection for wear and damage, proper lubrication during use, and storing tools in a clean, dry environment are essential practices for maintaining high speed steel tools and maximizing their lifespan.
Q:What are the primary industries that utilize high-speed steel?
A:High-speed steel finds extensive usage in industries such as automotive, aerospace, and manufacturing, where cutting, drilling, and machining operations are prevalent.