Introduction
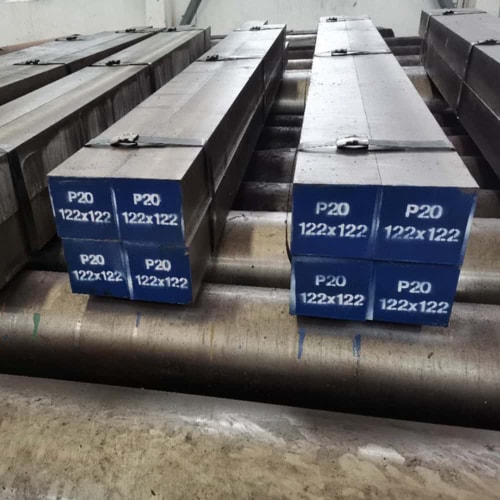
In the realm of manufacturing, efficiency is paramount. Every improvement in materials, processes, and technologies contributes to streamlined production and enhanced product quality. One such cornerstone of modern manufacturing is mould steel. This article delves into how mould steel revolutionizes manufacturing processes, unlocking new levels of efficiency and productivity.
Advantages of Mould Steel in Manufacturing Processes
Precision and Consistency
Mould steel enables the production of highly precise components with consistent quality. Its uniform properties and dimensional stability ensure repeatability in manufacturing processes, reducing waste and rework. Manufacturers can achieve tight tolerances and intricate geometries, meeting the demands of modern designs.
Extended Tool Life
The exceptional durability of mould steel prolongs tool life, minimizing downtime for maintenance and replacement. This longevity translates to cost savings and uninterrupted production schedules. By choosing the appropriate grade of mould steel and implementing proper heat treatment, manufacturers can optimize tool life for specific applications.
Complex Geometry
With mould steel’s superior machinability, manufacturers can create intricate molds and dies, accommodating complex part geometries and enhancing product design flexibility. From automotive components to consumer electronics casings, mould steel enables the production of diverse and sophisticated parts with ease.
Surface Finish
Mould steel’s high-quality surface finish eliminates the need for extensive post-processing, delivering finished components with minimal additional treatment, further streamlining production. This saves time and resources while maintaining aesthetic and functional requirements, especially in industries where surface quality is critical, such as consumer electronics and medical devices.
Case Studies: Mould Steel in Action
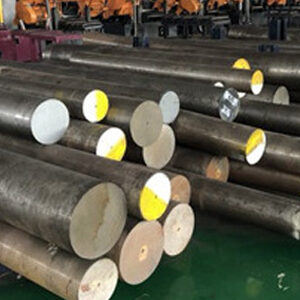
Automotive Industry
In automotive manufacturing, mould steel plays a pivotal role in producing precision components for engines, transmissions, and body panels. Its resilience ensures the longevity of critical tooling, contributing to efficient mass production. Manufacturers leverage mould steel’s properties to meet stringent performance and safety standards in the automotive sector.
Consumer Electronics
The consumer electronics sector relies on mould steel for manufacturing components such as casings, connectors, and circuitry. Its ability to maintain tight tolerances and surface finish requirements meets the exacting standards of modern electronics. Mould steel enables the production of sleek, durable, and high-performance devices that resonate with consumers worldwide.
Medical Devices
In the medical field, where precision and hygiene are paramount, mould steel facilitates the production of surgical instruments, implants, and diagnostic equipment. Its corrosion resistance and biocompatibility ensure compliance with stringent regulatory standards. From surgical tools to implantable devices, mould steel enables the creation of reliable and safe medical products that improve patient outcomes.
Understanding Mould Steel: Properties and Applications
Mould steel, also known as tool steel, is engineered to withstand high stress, wear, and abrasion. Its exceptional hardness, toughness, and machinability make it indispensable in various manufacturing applications. Let’s explore the properties and applications of mould steel:
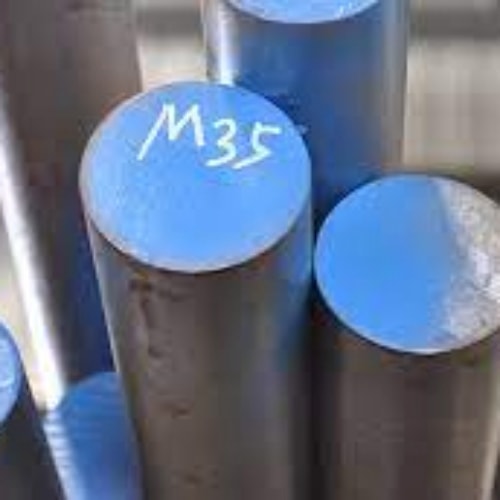
Property | Description |
---|---|
Hardness | High hardness ensures resistance to deformation and wear. |
Toughness | Ability to withstand impact and loading without fracturing. |
Machinability | Ease of machining allows for intricate mold designs. |
Corrosion Resistance | Protection against environmental degradation. |
Mould steel finds extensive use in injection molding, die casting, and extrusion processes across industries such as automotive, aerospace, consumer goods, and medical devices.
FAQ
Q: What are the main types of mould steel available?
A: The main types include P20, H13, S7, and D2, each tailored to specific manufacturing requirements based on factors such as hardness, toughness, and corrosion resistance. Manufacturers select the appropriate grade of mould steel based on the application’s demands and operating conditions.
Q: How can I optimize the performance of mould steel in my manufacturing process?
A: Proper heat treatment, maintenance, and lubrication are crucial for maximizing the performance and lifespan of mould steel tools. Consultation with material specialists can provide valuable insights into optimizing tooling processes. By following best practices and monitoring tool performance, manufacturers can enhance productivity and efficiency in their operations.
Q: Is mould steel suitable for high-temperature applications?
A: Yes, certain grades of mould steel, such as H13, are designed to withstand elevated temperatures encountered in processes like die casting and extrusion. These heat-resistant grades maintain their mechanical properties and dimensional stability at high temperatures, ensuring reliable performance in demanding manufacturing environments.
Conclusion
Mould steel stands as a cornerstone of modern manufacturing, enabling precision, durability, and versatility across a spectrum of industries. Its impact on efficiency and productivity cannot be overstated, as it continues to revolutionize manufacturing processes worldwide. By harnessing the properties and capabilities of mould steel, manufacturers can unlock new realms of possibility and remain competitive in an ever-evolving market landscape.
Through precision engineering, extended tool life, and versatility in design, mould steel empowers manufacturers to push the boundaries of what’s achievable, paving the way for a future of innovation and excellence in manufacturing. By embracing mould steel as a foundational material, manufacturers can optimize production processes, reduce costs, and deliver high-quality products that meet the demands of today’s dynamic market.