Introduction
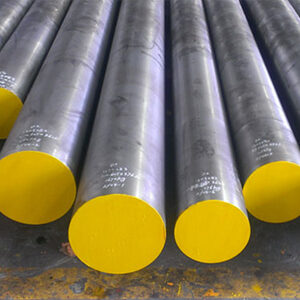
M7 tool steel is a pivotal material in industrial applications, valued for its exceptional properties that enhance performance and durability in tooling and manufacturing. This blog explores the comprehensive strengths of M7 tool steel, from its chemical composition to practical applications across various sectors.
What is M7 Tool Steel?
M7 tool steel, also known as 1.3348 steel, is a high-speed steel characterized by its high hardness, excellent wear resistance, and good toughness. It belongs to the M series of high-speed steels, which are widely used in cutting tools and machining applications due to their ability to maintain sharp cutting edges under high temperatures and stress.
Importance of Tool Steels in Industrial Settings
Tool steels play a crucial role in manufacturing processes where tools are subjected to high wear, heat, and stress. M7 steel specifically stands out for its balance of hardness and toughness, making it suitable for a wide range of applications where cutting efficiency and tool longevity are critical.
Properties of M7 Tool Steel
M7 tool steel possesses a combination of mechanical and chemical properties that contribute to its superior performance in industrial applications.
Mechanical Properties
The mechanical properties of M7 steel include:
- Hardness: Typically in the range of 60-65 HRC, which ensures the ability to maintain cutting edges even at elevated temperatures.
- Toughness: Exhibits good toughness, allowing the tool to withstand impact and shock during machining operations.
- Wear Resistance: High wear resistance due to its composition and heat treatment, prolonging tool life and reducing downtime for tool replacement.
Chemical Composition
The composition of M7 steel typically includes:
- Carbon (C): Provides hardness and wear resistance.
- Tungsten (W): Enhances hardness and heat resistance.
- Chromium (Cr) and Vanadium (V): Contribute to wear resistance and strength.
Microstructure Analysis
Microstructural analysis reveals a uniform distribution of carbides within a tempered martensitic matrix. This microstructure is essential for achieving the desired balance of hardness and toughness through proper heat treatment processes.
Applications in Cutting Tools
M7 tool steel is widely used in the production of cutting tools due to its superior properties that enhance cutting performance and tool life.
Drills and End Mills
In drilling applications, M7 tool steel drills maintain sharp cutting edges and withstand the high forces generated during metal removal. End mills made from M7 tool steel are capable of high-speed machining operations with excellent chip evacuation and surface finish.
Saw Blades and Reamers
Saw blades and reamers manufactured from M7 steel exhibit exceptional wear resistance and cutting precision. They are employed in industries requiring high accuracy and reliability in cutting operations.
Heat Treatment of M7 Tool Steel
The heat treatment process significantly influences the properties of M7 steel, optimizing its performance characteristics for specific applications.
Annealing and Hardening
Annealing of M7 tool steel involves heating to a specific temperature and holding it for sufficient time to achieve uniformity and relieve internal stresses. Hardening increases the hardness of the steel by heating to a critical temperature and quenching in oil or air to achieve martensitic transformation.
Tempering and Quenching
Tempering of M7 steel follows hardening to reduce brittleness and improve toughness. Different tempering temperatures are selected based on the desired balance between hardness and toughness for the application. Quenching methods are chosen to achieve the required hardness and microstructure.
Advantages in High-Speed Machining
M7 tool steel excels in high-speed machining applications due to its high heat resistance and ability to maintain cutting edge integrity at elevated temperatures.
High-Speed Drilling and Milling
In high-speed drilling and milling, M7 tool steel tools exhibit reduced wear and prolonged tool life compared to standard tool steels. They maintain dimensional accuracy and surface finish in high-production environments.
Turning and Boring Applications
M7 tool steel is effective in turning and boring operations where high cutting speeds and feed rates are required. It withstands the thermal and mechanical stresses encountered during these processes, contributing to overall machining efficiency.
Case Studies and Practical Examples
Real-world applications demonstrate the effectiveness of M7 steel in various industrial sectors, showcasing its performance under diverse operating conditions.
Automotive Industry Case Study
In automotive manufacturing, M7 steel is utilized for machining engine components, where high wear resistance and dimensional accuracy are critical for performance and reliability.
Aerospace Industry Application
Aerospace applications demand precision and durability from machining tools. M7 tool steel meets these requirements in the production of aircraft components, contributing to safety and performance.
Environmental Impact and Sustainability
Evaluating the environmental impact of M7 steel is crucial for sustainable manufacturing practices, considering its lifecycle and recyclability.
Recyclability and Longevity
M7 tool steel is recyclable, contributing to sustainable material management practices in manufacturing. Its longevity reduces the need for frequent tool replacements, minimizing waste and resource consumption.
Sustainable Manufacturing Practices
Selecting materials like M7 steel supports sustainable manufacturing by reducing energy consumption and environmental footprint throughout its lifecycle. Innovations in recycling and reuse further enhance sustainability in tooling applications.
Comparative Analysis with Other Tool Steels
Comparing M7 tool steel with other high-speed and tool steels provides insights into its unique advantages and considerations for specific applications.
Performance Metrics Comparison
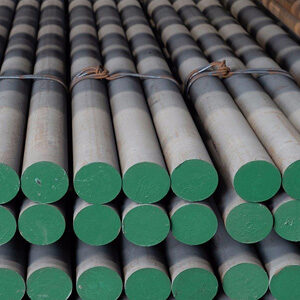
Comparative analysis reveals that M7 tool steel offers superior hardness, wear resistance, and toughness compared to conventional tool steels. Its balanced properties make it suitable for high-performance applications where cutting efficiency and tool longevity are paramount.
Industry Preferences and Trends
The preference for M7 steel continues to grow in industries requiring high-speed machining and precision cutting tools. Ongoing research and development focus on enhancing its properties and expanding its applications in evolving industrial sectors.
Conclusion
M7 tool steel emerges as a versatile and high-performance material in industrial applications, offering exceptional hardness, wear resistance, and toughness. Its widespread use in cutting tools and machining operations underscores its importance in enhancing productivity and reducing operational costs across various industries.
FAQ
Q:What are the key properties of M7 tool steel?
A:Discusses hardness, wear resistance, toughness, etc.
Q:How is M7 tool steel used in cutting tools?
A:Highlights applications in drills, end mills, etc.
Q:What is the heat treatment process for M7 tool steel?
A:Explains optimal heat treatment methods.
Q:What are the environmental benefits of using M7 tool steel?
A:Addresses recyclability and sustainability aspects.
Q:How does M7 tool steel compare to other tool steels?
A:Provides a comparative analysis of performance.