Introduction
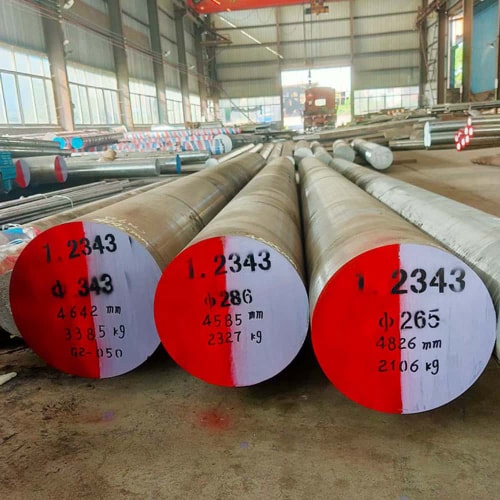
H11 tool steel is highly esteemed for its robust properties, positioning it as a preferred choice across diverse industrial applications. This comprehensive guide delves deep into the detailed characteristics and advantages of H11 tool steel, emphasizing its composition, mechanical properties, heat treatment, applications, and comparisons with other tool steels.
Composition of H11 Tool Steel
H11 tool steel is an air-hardening, hot-work tool steel primarily composed of:
- Chromium (Cr): Enhances hardenability and corrosion resistance.
- Tungsten (W): Improves high-temperature strength and wear resistance.
- Molybdenum (Mo): Enhances toughness and machinability.
- Vanadium (V): Refines grain structure and promotes wear resistance.
- Carbon (C): Provides hardness and strength.
The synergistic blend of these elements contributes significantly to the exceptional performance of H11 steel under thermal and mechanical stress.
Mechanical Properties
H11 tool steel boasts impressive mechanical properties essential for demanding applications:
- Hardness: Achieves a robust hardness of 55-60 HRC post heat treatment, ensuring longevity and durability in abrasive environments.
- Tensile Strength: Offers a formidable tensile strength of approximately 2000 MPa, ensuring structural integrity under heavy loads.
- Impact Resistance: Demonstrates exceptional toughness, crucial for applications subjected to sudden shocks.
- Wear Resistance: Exhibits outstanding wear resistance, maintaining sharp cutting edges and surfaces over prolonged use.
These superior properties make H11 steel an indispensable choice for tooling and components requiring reliability and extended service life.
Heat Treatment of H11 Tool Steel
Effective heat treatment is pivotal in optimizing H11 tool steel’s properties to meet specific application requirements:
- Annealing: Slow cooling from austenitizing temperature refines microstructure and relieves internal stresses, enhancing machinability.
- Hardening: Quenching in oil or air from elevated temperatures maximizes hardness and dimensional stability.
- Tempering: Precise tempering at controlled temperatures balances hardness with toughness, minimizing brittleness while retaining strength.
Careful adherence to heat treatment processes ensures H11 steel attains optimal performance characteristics essential for manufacturing and engineering applications.
Applications of H11 Tool Steel
H11 tool steel finds extensive application across various industries owing to its robust properties:
- Forging and Die Casting: Ideal for dies and molds requiring exceptional toughness and resistance to thermal fatigue.
- Extrusion: Well-suited for extrusion tooling due to its capability to withstand high temperatures and resist wear.
- High-Temperature Operations: Utilized in hot punches, forging dies, and aluminum die casting due to its excellent heat resistance and dimensional stability.
Its versatility and reliability position H11 steel as a preferred material choice in demanding industrial environments.
Case Studies and Performance Comparisons
Comparative analysis highlights the superior performance of H11 tool steel relative to other materials:
- Comparison with Tool Steel A: H11 demonstrates superior toughness and wear resistance compared to Tool Steel A, making it suitable for heavy-duty applications.
- Comparison with Tool Steel B: H11 surpasses Tool Steel B in impact strength and thermal stability, ensuring prolonged tool life and reduced maintenance costs.
Real-world case studies underscore H11 steel’s efficacy and cost-effectiveness in industrial tooling solutions.
Comparison of H11 Tool Steel properties with Other Tool Steels
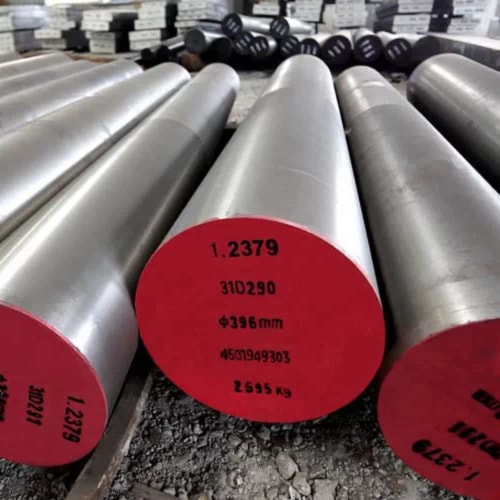
Property | H11 Tool Steel | Tool Steel A | Tool Steel B |
---|---|---|---|
Hardness (HRC) | 55-60 | 50-55 | 60-65 |
Tensile Strength | 2000 MPa | 1800 MPa | 2200 MPa |
Impact Strength | High | Medium | High |
Wear Resistance | Excellent | Good | Excellent |
This comparative table succinctly summarizes key properties of H11 tool steel against other commonly used tool steels, highlighting its strengths in hardness, impact resistance, and wear resistance.
Conclusion
In conclusion, H11 tool steel exemplifies superior properties essential for high-performance tooling and manufacturing applications. Its precise composition, robust mechanical attributes, effective heat treatment processes, diverse industrial applications, and comparative advantages underscore its significance in achieving reliability, efficiency, and cost-effectiveness in critical operations.
FAQ
Q:What are the main alloying elements in H11 tool steel?
A:Chromium, tungsten, molybdenum, vanadium, and carbon are the primary alloying elements.
Q:What is the typical hardness range of H11 tool steel?
A:H11 tool steel typically has a hardness range of 55-60 HRC.
Q:Which industries commonly use H11 tool steel?
A:H11 tool steel finds application in forging, die casting, extrusion, and high-temperature operations.
Q:How does heat treatment affect H11 tool steel properties?
A:Proper heat treatment enhances hardness, toughness, and machinability, optimizing H11 steel for specific applications.
Q:What advantages does H11 tool steel offer over other tool steels?
A:H11 tool steel provides excellent wear resistance, high hardness, and superior toughness compared to many other tool steels.