Introduction
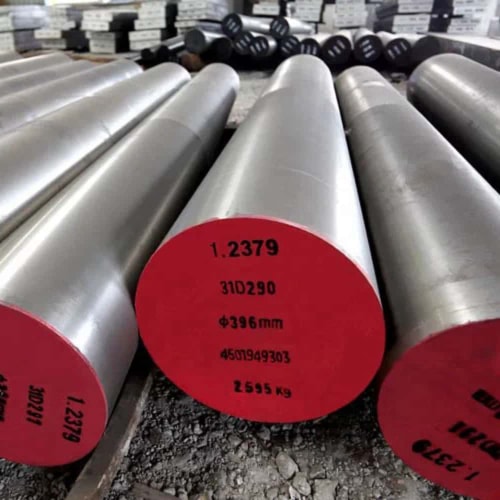
In today’s manufacturing landscape, the choice of tool steel suppliers is pivotal to ensuring product quality, reliability, and operational efficiency. Tool steel, renowned for its hardness, durability, and ability to withstand harsh conditions, is indispensable across industries like automotive, aerospace, and machinery manufacturing. This blog delves into the crucial role of tool steel suppliers and explores the factors that make their selection vital in the production process.
Understanding Tool Steel Suppliers
What is Tool Steel?
Tool steel is a specialized type of carbon and alloy steel designed for making tools, dies, and molds. It possesses high hardness, abrasion resistance, and the ability to retain sharp cutting edges under high temperatures, making it ideal for applications requiring toughness and durability.
Role of Tool Steel Suppliers
Tool steel suppliers are integral to the manufacturing supply chain, providing high-quality raw materials that meet rigorous industry standards. They ensure consistency in material properties, reliable delivery schedules, and technical support to optimize tooling performance and reduce production costs.
Factors to Consider When Choosing Tool Steel Suppliers
Quality and Certification
Choosing a supplier that adheres to international quality standards such as ISO 9001 ensures that tool steels meet specified mechanical properties and dimensional tolerances. Certifications like ISO 14001 indicate commitment to environmental management practices, promoting sustainability in manufacturing processes.
Range of Products
A diverse product portfolio allows manufacturers to select tool steels tailored to specific applications, including cold work, hot work, high-speed steel, and plastic mold steel. Suppliers offering comprehensive options cater to various machining and tooling needs, enhancing versatility and performance.
Technical Expertise and Support
Effective tool steel suppliers offer valuable technical guidance on material selection, heat treatment processes, and machining recommendations. Their expertise helps optimize tool performance, extend tool life, and mitigate operational risks, contributing to overall productivity gains.
Importance of Reliable Supply Chains
Just-in-Time Delivery
Timely delivery of tool steels minimizes production downtime and inventory costs. Reliable suppliers maintain efficient logistics networks and inventory management systems to ensure seamless supply chain operations, meeting fluctuating demand and production schedules.
Consistency and Traceability
Traceable supply chains enable manufacturers to verify the origin and quality of tool steels, ensuring compliance with regulatory requirements and quality standards. Consistent material properties facilitate predictable tool performance and reduce the incidence of defects in finished products.
Case Studies and Success Stories
Case Study : Automotive Industry Application
An in-depth analysis showcasing how automotive manufacturers benefit from partnering with reliable tool steel suppliers. Insights into material selection strategies, performance metrics improvement, and supplier collaboration enhancing manufacturing efficiency and product quality.
Case Study : Aerospace Industry Application
Examining the critical role of tool steel suppliers in meeting stringent performance requirements and regulatory standards within the aerospace industry. Case examples highlight innovation in material technologies, supply chain integration, and long-term partnership benefits.
Comparison of Tool Steel Types
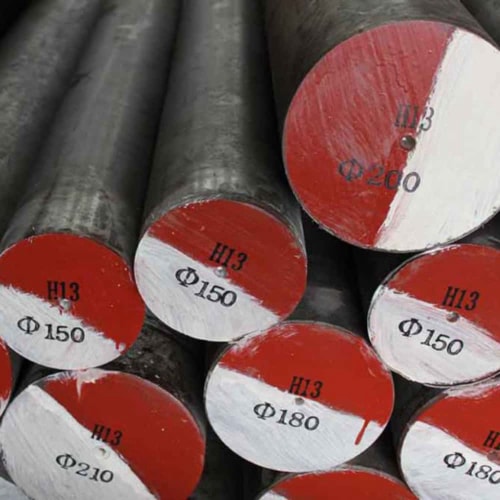
Type of Tool Steel | Characteristics | Applications |
---|---|---|
Cold Work Steel | High hardness, wear resistance | Stamping dies, cutting tools |
Hot Work Steel | Heat resistance, toughness | Forging dies, extrusion tools |
High-Speed Steel | Superior cutting performance | Drills, milling cutters, taps |
Plastic Mold Steel | Corrosion resistance, polishability | Injection molds, extrusion dies |
Conclusion
Choosing the right tool steel supplier is pivotal for achieving manufacturing excellence and competitiveness. By prioritizing factors such as quality, technical expertise, and supply chain reliability, manufacturers can optimize tooling performance, reduce operational costs, and enhance overall productivity. As industries evolve, the role of tool steel suppliers remains indispensable in driving innovation and sustainable growth.
FAQ
Q:What are the different types of tool steels?
A:Tool steels are classified into various types based on composition and performance characteristics, including cold work, hot work, high-speed steel, and plastic mold steel, each suited to specific manufacturing applications.
Q:How can I ensure the quality of tool steel products?
A:Ensure your tool steel supplier maintains certifications like ISO 9001 and provides material test reports (MTRs) with each shipment. Conduct regular quality audits and inspections to verify material properties and consistency, ensuring adherence to stringent industry standards.
Q:What role does heat treatment play in tool steel performance?
A:Heat treatment processes such as annealing, quenching, and tempering significantly impact tool steel hardness, toughness, and wear resistance. Proper heat treatment enhances material properties, optimizing tool performance for demanding machining applications.