Introduction
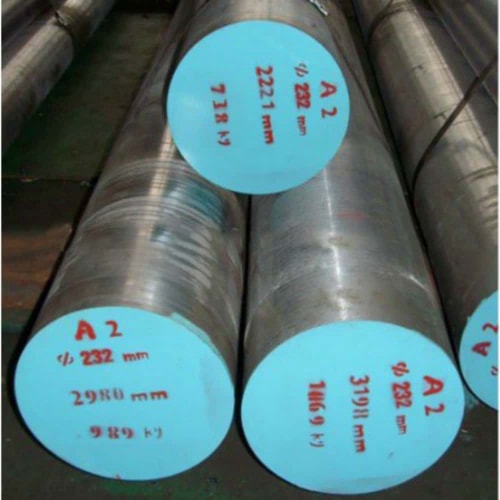
A2 tool steel is a versatile material widely used in the manufacturing of cutting tools, dies, and other applications where high wear resistance and toughness are essential. Its performance largely depends on the quality of its heat treatment. This blog explores the intricate process of heat treating A2 tool steel, emphasizing its importance in achieving optimal mechanical properties and extending tool life.
Properties of A2 Tool Steel Heat Treatment
A2 tool steel is characterized by its excellent wear resistance, good toughness, and dimensional stability. These properties make it suitable for applications that require cutting, forming, or stamping operations under demanding conditions. The alloy composition, which includes chromium, manganese, molybdenum, and vanadium, contributes to its ability to retain hardness and withstand wear.
Importance of Heat Treatment
Enhancing Hardness and Wear Resistance
The primary objective of heat treating A2 tool steel is to enhance its hardness and wear resistance. This is achieved through a sequence of controlled heating, rapid cooling (quenching), and tempering processes.
Austenitizing involves heating the steel to a temperature typically between 1700°F and 1800°F (925°C to 980°C) to convert it into an austenitic structure. The precise temperature and holding time are critical to ensuring uniform transformation across the entire material.
Improving Toughness and Dimensional Stability
After austenitizing, the steel undergoes quenching, where it is rapidly cooled in a medium such as air, oil, or polymer. The choice of quenching medium influences the final hardness and microstructure of the steel. Proper quenching ensures the formation of a hardened martensitic structure, which is crucial for achieving high hardness levels (approximately 60-62 HRC) and excellent wear resistance.
Tempering follows quenching to reduce the hardness to a more practical level while improving toughness and dimensional stability. Tempering temperatures typically range from 400°F to 1200°F (200°C to 650°C), depending on the desired balance between hardness and toughness. Multiple tempering cycles may be employed to achieve the optimal combination of properties.
A2 Tool Steel Heat Treatment Process
Austenitizing
During austenitizing, it is essential to control the heating rate to prevent thermal stresses and ensure uniform heating throughout the steel. The steel is held at the austenitizing temperature for a sufficient duration to allow for complete transformation.
Quenching
Quenching is a critical step that requires careful consideration of cooling rates to avoid cracking and distortion. The cooling medium and agitation rate play significant roles in achieving the desired hardness and microstructure. Air quenching provides a slower cooling rate, while oil or polymer quenching offers faster rates, each influencing the final properties of the steel.
Tempering
Tempering is performed immediately after quenching to reduce the brittleness induced by the high hardness of martensite. The tempering temperature and time are selected based on the desired mechanical properties. Lower tempering temperatures result in higher hardness and wear resistance, whereas higher temperatures improve toughness and reduce internal stresses.
Factors Affecting Heat Treatment
Steel Composition
The composition of A2 tool steel, particularly the levels of carbon, chromium, and vanadium, affects its hardenability and response to heat treatment. Higher alloy content generally enhances wear resistance and toughness but may require more precise control during heat treatment.
Heating and Cooling Rates
Controlling the heating and cooling rates is critical to achieving uniform hardness and minimizing the risk of cracking. Rapid cooling rates during quenching promote the formation of martensite, while slower rates allow for partial transformation to bainite or pearlite, depending on the quenching medium and steel composition.
Surface Preparation and Preheating
Proper surface preparation, including cleaning and removing contaminants, ensures uniform heat distribution and minimizes surface defects. Preheating the steel before austenitizing reduces thermal gradients and internal stresses, improving dimensional stability during heat treatment.
Comparison of Heat Treatment Parameters
Heat Treatment Step | Temperature Range | Cooling Medium | Purpose |
---|---|---|---|
Austenitizing | 1700°F – 1800°F | Air, Oil, Polymer | Convert to austenite for uniform transformation |
Quenching | Variable | Air, Oil, Polymer | Rapid cooling to form martensite for high hardness |
Tempering | 400°F – 1200°F | Air, Oil, Salt Bath | Reduce hardness while improving toughness |
Case Studies and Applications
Case Study : Punches and Dies
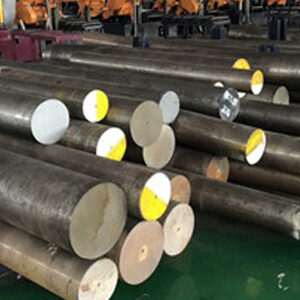
A2 tool steel heat treated to high hardness levels is ideal for punching and stamping applications due to its exceptional wear resistance and edge retention. The combination of hardness and toughness allows punches and dies to withstand repetitive impacts and abrasive wear, resulting in extended tool life.
Case Study : Forming Tools
Forming tools such as dies and molds benefit from A2 tool steel’s ability to maintain dimensional stability and toughness under cyclic loading conditions. Proper heat treatment ensures minimal wear and deformation during forming operations, improving product quality and reducing tool maintenance costs.
Conclusion
A2 tool steel’s performance in industrial applications hinges significantly on the quality of its heat treatment. By understanding and optimizing the heat treatment process, manufacturers can unlock the full potential of A2 tool steel, ensuring enhanced durability, wear resistance, and dimensional stability in their tools and components.
FAQ
Q:What is A2 tool steel known for?
A:A2 tool steel is renowned for its high hardness, excellent wear resistance, and good toughness, making it suitable for cutting tools, dies, and other applications subjected to abrasive wear.
Q:Why is heat treatment important for A2 tool steel?
A:Heat treatment enhances the mechanical properties of A2 tool steel, including hardness, toughness, and dimensional stability, ensuring optimal performance in demanding applications.
Q:What are the primary steps in heat treating A2 tool steel?
A:The primary steps include austenitizing, quenching, and tempering. Austenitizing involves heating the steel to a critical temperature, quenching rapidly cools it to form martensite, and tempering reduces brittleness while improving toughness.