Introduction
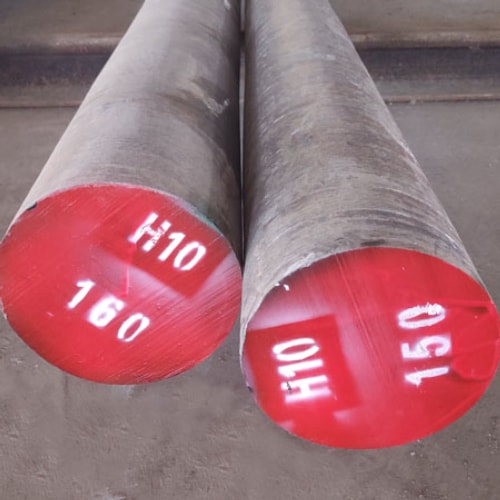
H10 tool steel is a versatile and durable material widely used in various industrial applications. Known for its excellent high-temperature properties and resistance to thermal fatigue, H10 tool steel is a popular choice for tooling and manufacturing processes. This comprehensive guide will delve into the properties, applications, and benefits of H10 tool steel, providing a thorough understanding of why this material is highly regarded in the industry.
What is H10 Tool Steel?
it is part of the hot work tool steel family, known for its exceptional toughness, wear resistance, and ability to withstand high temperatures. It is primarily used in applications where the tool will be exposed to elevated temperatures and requires maintaining its strength and hardness.
Composition of H10 Tool Steel
It has a specific chemical composition that gives it its unique properties. The primary elements include:
- Carbon (C): 0.32-0.45%
- Chromium (Cr): 2.75-3.50%
- Molybdenum (Mo): 0.75-1.20%
- Vanadium (V): 0.20-0.50%
- Silicon (Si): 0.80-1.20%
- Manganese (Mn): 0.20-0.50%
These elements work together to enhance the steel’s toughness, strength, and thermal stability.
Properties of H10 Tool Steel
High-Temperature Resistance
One of the most notable properties of H10 tool steel is its ability to withstand high temperatures without losing its strength or hardness. This makes it ideal for applications such as hot forging and extrusion processes.
Thermal Fatigue Resistance
It is highly resistant to thermal fatigue, which is the cracking that can occur when materials are subjected to repeated heating and cooling cycles. This property extends the lifespan of tools made from H10 steel, reducing the need for frequent replacements.
Wear Resistance
It exhibits excellent wear resistance, ensuring that the tools maintain their shape and effectiveness over time, even under strenuous working conditions.
Toughness
The toughness of H10 tool steel allows it to absorb impact and shock without fracturing, making it suitable for heavy-duty applications.
Applications of H10 Tool Steel
Hot Forging
It is commonly used in hot forging due to its ability to withstand high temperatures and resist thermal fatigue. It ensures that the dies used in forging processes remain effective for longer periods, improving efficiency and reducing downtime.
Die Casting
In die casting, It is used for making dies that can endure the thermal cycling and high pressures involved in the process. Its resistance to heat and wear makes it ideal for producing high-quality, durable die castings.
Extrusion
It is also used in extrusion processes where materials are forced through a die to create specific shapes. Its thermal stability and toughness are critical in maintaining the precision and longevity of extrusion dies.
Molds for Plastic Injection
The high wear resistance and toughness of H10 tool steel make it suitable for molds used in plastic injection molding. These molds need to withstand repeated use and maintain their dimensional accuracy, which H10 tool steel provides.
Benefits of Using H10 Tool Steel
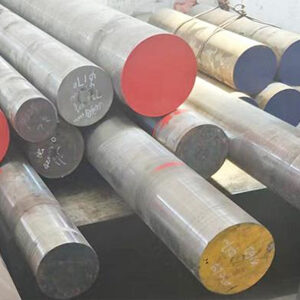
Extended Tool Life
The properties of H10 tool steel, such as high-temperature resistance and thermal fatigue resistance, contribute to a longer tool life. This reduces the frequency of tool replacements, leading to cost savings and increased productivity.
Improved Performance
Tools made from H10 tool steel perform consistently under high temperatures and strenuous conditions, ensuring that manufacturing processes run smoothly and efficiently.
Cost-Effective
Although the initial cost of H10 tool steel may be higher than other materials, its durability and extended lifespan make it a cost-effective choice in the long run.
Versatility
H10 tool steel’s unique combination of properties makes it suitable for a wide range of applications, from forging and die casting to extrusion and plastic injection molding. This versatility makes it a valuable material in various industries.
Comparison with Other Tool Steels
Table: Comparison of H10 Tool Steel with Other Hot Work Tool Steels
Property | H10 Tool Steel | H13 Tool Steel | H11 Tool Steel |
---|---|---|---|
Carbon Content | 0.32-0.45% | 0.32-0.45% | 0.32-0.45% |
Chromium Content | 2.75-3.50% | 4.75-5.50% | 4.75-5.50% |
Molybdenum Content | 0.75-1.20% | 1.10-1.75% | 1.10-1.75% |
Vanadium Content | 0.20-0.50% | 0.80-1.20% | 0.80-1.20% |
Thermal Fatigue Resistance | High | Very High | High |
Wear Resistance | Excellent | Excellent | Very Good |
Toughness | High | High | Very High |
Applications | Forging, Die Casting, Extrusion | Die Casting, Extrusion, Plastic Injection Molding | Forging, Die Casting, Extrusion |
Heat Treatment of H10 Tool Steel

Hardening Process
The hardening process of H10 tool steel involves heating the material to a specific temperature range, typically between 1025°C and 1080°C, followed by rapid cooling, usually in oil or air. This process enhances the hardness and strength of the steel.
Tempering
After hardening, H10 tool steel is tempered to reduce brittleness and achieve the desired mechanical properties. The tempering temperature typically ranges from 500°C to 650°C, depending on the specific application requirements.
Annealing
Annealing is performed to soften the H10 tool steel for machining or to relieve internal stresses. This process involves heating the steel to a temperature range of 820°C to 880°C, followed by slow cooling in a furnace.
Machinability and Welding
Machinability
H10 tool steel offers good machinability, making it easier to shape and form into desired tools and components. Using appropriate cutting tools and machining parameters is crucial to ensure precision and surface finish.
Welding
Welding H10 tool steel requires careful consideration of preheating and post-weld heat treatment to avoid cracking and ensure the integrity of the weld. Preheating to around 300°C to 400°C and post-weld tempering are typically recommended.
Conclusion
H10 tool steel is a highly valuable material in various industries due to its exceptional high-temperature resistance, thermal fatigue resistance, and overall durability. Its versatility makes it suitable for applications such as hot forging, die casting, extrusion, and plastic injection molding. By understanding the properties, applications, and benefits of H10 tool steel, manufacturers can make informed decisions to optimize their tooling processes and enhance productivity.
FAQ
What are the main advantages of H10 tool steel?
H10 tool steel offers high-temperature resistance, excellent thermal fatigue resistance, wear resistance, and toughness, making it ideal for demanding applications.
How does H10 tool steel compare to H13 tool steel?
H10 tool steel has slightly lower chromium and vanadium content compared to H13, resulting in different properties. H13 offers very high thermal fatigue resistance and is often preferred for applications requiring extreme durability.
Can H10 tool steel be welded?
Yes, H10 tool steel can be welded with proper preheating and post-weld heat treatment to avoid cracking and ensure the weld’s integrity.
What industries commonly use H10 tool steel?
Industries such as automotive, aerospace, manufacturing, and construction commonly use H10 tool steel for applications involving hot forging, die casting, extrusion, and plastic injection molding.
What is the typical heat treatment process for H10 tool steel?
The heat treatment process for H10 tool steel includes hardening by heating to 1025°C-1080°C, followed by rapid cooling, tempering at 500°C-650°C, and annealing at 820°C-880°C to relieve stresses or soften the material.