Introduction

D2 tool steel is renowned for its exceptional hardness, making it a vital material in the manufacturing of cutting tools, dies, and punches. This comprehensive guide explores the intricacies of D2 steel hardness, its composition, applications, and factors influencing its mechanical properties.
What is D2 Tool Steel?
D2 tool steel belongs to the cold-work tool steel category, characterized by high carbon (1.40-1.60%) and chromium (11.00-13.00%) content. This combination results in superior hardness, wear resistance, and dimensional stability at elevated temperatures. It is widely used in industries requiring high-performance tooling materials that endure rigorous conditions.
Chemical Composition of D2 Tool Steel
The chemical composition of D2 steel significantly influences its mechanical properties, including hardness. Apart from carbon and chromium, D2 steel contains molybdenum (0.70-1.20%), vanadium (0.70-1.20%), silicon (0.60% max), and manganese (0.60% max). These elements enhance hardenability, wear resistance, and toughness, making D2 steel suitable for various industrial applications.
Chemical Composition of D2 Tool Steel
Element | Composition (%) |
---|---|
Carbon (C) | 1.40 – 1.60 |
Chromium (Cr) | 11.00 – 13.00 |
Molybdenum (Mo) | 0.70 – 1.20 |
Vanadium (V) | 0.70 – 1.20 |
Silicon (Si) | 0.60 max |
Manganese (Mn) | 0.60 max |
Hardness of D2 Tool Steel
The hardness of D2 steel is predominantly determined by its microstructure, which is optimized through heat treatment processes such as quenching and tempering. After heat treatment, D2 steel typically achieves a hardness of 58-62 HRC (Rockwell C scale), which ensures excellent resistance to abrasive wear and deformation under high stress conditions.
Factors Affecting D2 Tool Steel Hardness
Several factors influence the hardness of D2 tool steel:
- Heat Treatment: The hardening process involves austenitizing at high temperatures followed by quenching in oil or air to achieve a fully hardened structure.
- Composition: Higher carbon and chromium content enhance the hardenability of D2 steel, resulting in higher achievable hardness levels.
- Grain Size: Fine grain structure obtained through proper heat treatment contributes to increased hardness and improved toughness.
- Surface Finish: Grinding and polishing operations affect the surface hardness and dimensional accuracy of finished tools and components.
Applications of D2 Tool Steel
Due to its high hardness, wear resistance, and dimensional stability, D2 tool steel is employed in various industrial applications:
- Cutting Tools: Blades, knives, drills, and taps benefit from D2 steel’s ability to maintain sharp cutting edges.
- Cold Working Tools: Punches, dies, and forming tools endure high stress and abrasive wear conditions, making D2 steel ideal for prolonged use.
- Molds and Dies: Plastic injection molds and forging dies require materials with excellent wear resistance and dimensional stability, where D2 steel excels.
- Woodworking Tools: Chisels, plane blades, and saw blades benefit from D2 steel’s ability to retain sharpness and withstand impact.
Testing and Measuring D2 Tool Steel Hardness
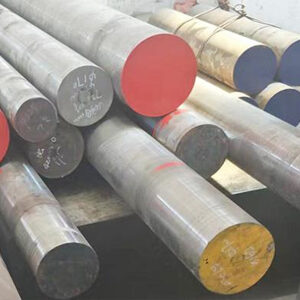
The hardness of D2 steel is typically measured using the Rockwell C scale (HRC). Other methods such as Brinell and Vickers hardness tests provide additional insights depending on specific application requirements and industry standards. Proper hardness testing ensures that D2 steel meets performance expectations in demanding operational environments.
Conclusion
In conclusion, D2 tool steel hardness is a defining characteristic that underpins its suitability for a wide range of industrial applications. Its composition, coupled with precise heat treatment processes, enables manufacturers to achieve desired hardness levels critical for tool longevity and performance. Understanding these aspects of D2 tool steel hardness ensures informed material selection and enhances operational efficiency in manufacturing processes.
FAQ
Q: What is the typical hardness range for D2 tool steel?
A: D2 steel typically ranges from 58 to 62 HRC after proper heat treatment, ensuring excellent wear resistance and toughness.
Q: How does D2 steel compare to other tool steels in terms of hardness?
A: D2 steel offers higher hardness compared to many other tool steels due to its high carbon and chromium content, making it suitable for applications requiring superior wear resistance and dimensional stability.
Q: Can D2 tool steel be welded?
A: D2 steel is challenging to weld due to its high carbon and chromium content, which can lead to cracking during welding. Preheating and post-weld heat treatment are recommended to minimize these issues and maintain material integrity.