Introduction
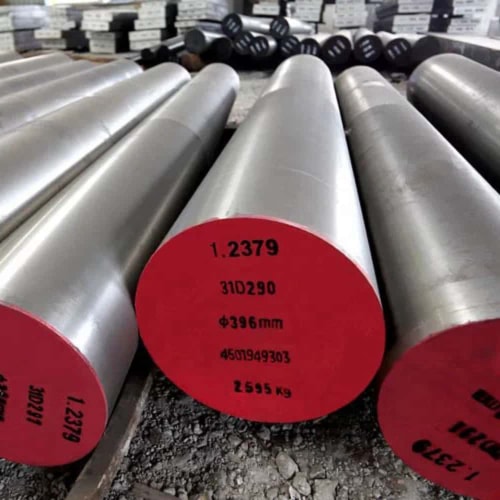
Cold work tool steel is an essential material in various manufacturing and machining processes. This specialized steel is known for its excellent hardness and wear resistance, making it ideal for a wide range of cold work tool steel applications. In this blog, we will delve into the characteristics that make cold work tool steel suitable for these applications, explore specific use cases, and discuss its significance across different industries.
What is Cold Work Tool Steel?
Cold work tool steel is designed for tools that operate at room temperature, as opposed to hot work tool steels, which are utilized in high-temperature environments. Cold work tool steels typically have high carbon content and various alloying elements that enhance their performance in cold work tool steel applications.
Key Characteristics of Cold Work Tool Steel
- High Hardness: Essential for wear resistance in cold work tool steel applications.
- Toughness: Ability to withstand stress without cracking.
- Dimensional Stability: Maintains shape and integrity during use.
- Wear Resistance: Critical for long-lasting tools.
Common Cold Work Tool Steel Grades
Different grades of cold work tool steel are tailored for specific applications. Below is a table highlighting some of the most common grades:
Grade | Composition | Typical Cold Work Tool Steel Applications |
---|---|---|
D2 | High carbon, chromium | Punches, dies, shear blades |
O1 | Oil-hardening, high carbon | General-purpose tools |
A2 | Air-hardening, chromium | Cutting tools, molds |
S7 | Shock-resistant, high toughness | Heavy-duty tools, impact applications |
M2 | High-speed, tungsten | Machining applications |
Applications of Cold Work Tool Steel
Punches and Dies
One of the primary cold work tool steel applications is in the manufacturing of punches and dies. These tools require high hardness and wear resistance to perform efficiently in stamping and forming processes.
Shear Blades
Cold work tool steel is also widely used for shear blades, which cut through various materials. The hardness of cold work tool steel makes it a top choice for this application in metal fabrication.
Cold Heading Tools
Cold heading is a process that involves forming metal at room temperature. Cold work tool steel’s durability and strength make it ideal for tools used in this cold work tool steel application, ensuring long tool life and performance.
Molds for Plastic Injection
In the realm of plastic injection molding, cold work tool steel is preferred for molds due to its toughness and wear resistance. These characteristics ensure that the molds maintain their integrity under high production rates.
Knives and Blades
Cold work tool steel is a popular choice for manufacturing knives and blades used in industrial applications. Its ability to retain sharpness and withstand wear makes it suitable for these demanding cold work tool steel applications.
Automotive Components
In the automotive industry, cold work tool steel is utilized for components that demand high strength and durability. Applications include connectors, brackets, and various high-performance parts.
Aerospace Applications
Cold work tool steel is crucial in the aerospace sector, where tools must perform under extreme conditions. This includes the manufacture of tools that produce critical components for aircraft and spacecraft.
Benefits of Using Cold Work Tool Steel
Enhanced Performance
The benefits of using cold work tool steel in various cold work tool steel applications include:
- Long Tool Life: Reduced frequency of tool replacements saves costs.
- Precision Manufacturing: Ensures high-quality outputs in production.
Cost-Effectiveness
Despite higher initial costs, the longevity and reduced downtime associated with cold work tool steel make it a cost-effective choice in the long run.
Versatility
Cold work tool steel’s adaptability allows for its use across various industries, making it a favorite for manufacturers seeking reliability and performance.
Comparison with Other Tool Steels
To better understand the role of cold work tool steel, it is useful to compare it with other tool steels:
Tool Steel Type | Operating Temperature | Hardness | Typical Cold Work Tool Steel Applications |
---|---|---|---|
Cold Work | Room Temperature | High | Punches, dies, shear blades |
Hot Work | Elevated Temperatures | Moderate | Forging dies, hot cutting tools |
High-Speed | Variable | Very High | Machining tools, drills, end mills |
Challenges in Cold Work Tool Steel Applications
Brittleness
Cold work tool steel can exhibit brittleness, which may lead to chipping or cracking under high stress. Proper heat treatment is crucial to address this issue in cold work tool steel applications.
Cost
The expense associated with cold work tool steel is higher than standard steels due to its alloying elements and specific heat treatment processes.
Machinability
While cold work tool steel is incredibly tough, its hardness can pose challenges during machining, necessitating specialized equipment and techniques.
Future Trends in Cold Work Tool Steel Applications
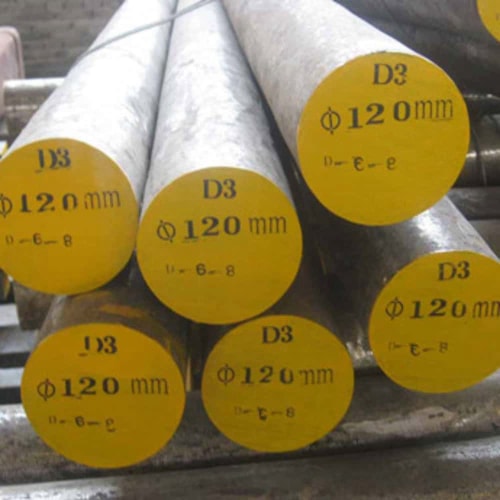
The future for cold work tool steel applications looks bright, with several emerging trends:
Development of New Alloys
Ongoing research is focused on creating new alloy compositions to further enhance the performance of cold work tool steels in various applications.
Increased Automation
As manufacturing processes become more automated, the demand for durable tools made from cold work tool steel is likely to rise.
Sustainable Practices
With industries shifting toward sustainability, the development of environmentally friendly tool steels may become a priority.
Conclusion
Cold work tool steel is a vital component in numerous manufacturing and machining processes. Its unique properties, including high hardness and wear resistance, make it ideal for a wide range of cold work tool steel applications, from punches and dies to aerospace components. Despite challenges such as brittleness and cost, the advantages of using cold work tool steel far outweigh the drawbacks, ensuring its ongoing relevance in modern industry.
FAQ
Q:What is the difference between cold work tool steel and hot work tool steel?
A:Cold work tool steel is intended for use at room temperature and offers high hardness and wear resistance, while hot work tool steel is utilized in high-temperature environments for applications such as forging.
Q:Can cold work tool steel be used for machining applications?
A:Yes, cold work tool steel is often employed in machining applications due to its excellent wear resistance and hardness, making it suitable for various cold work tool steel applications.
Q:How does heat treatment affect cold work tool steel?
A:Heat treatment significantly impacts the hardness, toughness, and overall performance of cold work tool steel, enhancing its desirable properties for specific cold work tool steel applications.
Q:What industries commonly use cold work tool steel?
A:Industries such as automotive, aerospace, and manufacturing frequently utilize cold work tool steel for various applications, including cutting tools, dies, and other essential tools.
Q:Is cold work tool steel environmentally friendly?
A:While cold work tool steel itself is not inherently eco-friendly, ongoing research aims to develop more sustainable practices in the industry to address environmental concerns.
Q:What are some alternatives to cold work tool steel?
A:Alternatives to cold work tool steel include hot work tool steel, high-speed steel, and polymer-based materials, each offering specific applications and advantages.
Q:How can I choose the right cold work tool steel grade for my application?
A:Selecting the appropriate grade involves considering factors such as required hardness, toughness, and specific application needs. Consulting with a material specialist can assist in making the best choice for cold work tool steel applications.