Introduction
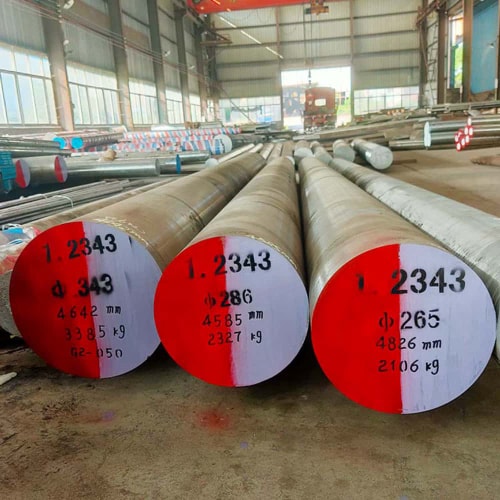
Tool steel types are the backbone of the manufacturing industry, providing the necessary hardness, durability, and wear resistance for a wide range of applications. From cutting tools and dies to molds and punches, tool steel types play a crucial role in shaping the products we use every day. But with so many different tool steel types available, choosing the right one for a specific application can be overwhelming.
In this comprehensive guide, we will delve into the world of tool steel types, exploring their various types, properties, and applications. By the end of this article, you will have a better understanding of how to select the optimal tool steel type for your project.
Understanding Tool Steels
Tool steels are alloys primarily composed of iron, carbon, and alloying elements such as chromium, vanadium, tungsten, and molybdenum. These alloying elements impart specific properties to the steel, such as hardness, toughness, wear resistance, and red hardness.
Key Properties of Tool Steels:
- Hardness: The ability of a material to resist penetration.
- Toughness: The ability of a material to absorb energy before fracturing.
- Wear resistance: The ability of a material to resist abrasion and wear.
- Red hardness: The ability of a material to retain its hardness at elevated temperatures.
Types of Tool Steels
Tool steel types can be broadly classified into several categories based on their composition and intended use:
- Carbon Tool Steels: These steels contain relatively high amounts of carbon and are suitable for general-purpose cutting tools.
- Alloy Tool Steels: These steels contain alloying elements that improve their performance compared to carbon tool steels.
- High-Speed Steels: These steels are designed for high-speed machining operations and exhibit excellent red hardness.
- Shock-Resistant Tool Steels: These steels have high toughness and are used for applications that involve impact loads.
- Mold and Die Steels: These steels are specifically designed for making molds and dies for various manufacturing processes.
A Comparison of Tool Steel Types
Property | Carbon Tool Steel | Alloy Tool Steel | High-Speed Steel | Shock-Resistant Tool Steel | Mold and Die Steel |
---|---|---|---|---|---|
Hardness | Moderate | High | High | Moderate | High |
Toughness | Moderate | Moderate | Moderate | High | Moderate |
Wear resistance | Moderate | High | High | Moderate | High |
Red hardness | Low | Moderate | High | Moderate | Moderate |
Cost | Low | Moderate | High | Moderate | High |
Selecting the Right Tool Steel Type
Choosing the appropriate tool steel type for a specific application requires careful consideration of several factors, including:
- The material being machined: Different materials require different tool steel types.
- The machining process: The cutting speed, feed rate, and depth of cut will influence the choice of tool steel type.
- The desired tool life: The expected lifespan of the tool will determine the required hardness and toughness.
- The operating temperature: For high-temperature applications, red hardness is a critical factor.
Applications of Tool Steel Types
Tool steel types find widespread use in a variety of industries, including:
- Automotive: Manufacturing engine components, transmission parts, and body panels.
- Aerospace: Producing aircraft components, such as turbine blades and landing gear.
- Medical: Creating surgical instruments and implants.
- Electronics: Manufacturing semiconductor components and printed circuit boards.
Heat Treatment of Tool Steel Types
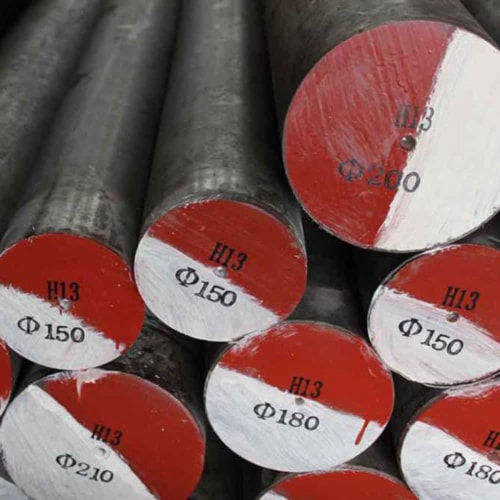
Heat treatment is a critical process that modifies the properties of tool steel types. Common heat treatment processes include:
- Annealing: Softening the steel for machining.
- Quenching: Rapidly cooling the steel to increase hardness.
- Tempering: Reducing the brittleness of the quenched steel.
Conclusion
Tool steel types are essential materials for modern manufacturing. By understanding the different tool steel types and their properties, you can make informed decisions when selecting the right tool steel type for your application. Remember that the choice of tool steel type should always be based on a thorough analysis of the specific requirements of your project.
FAQ
What is the difference between carbon steel and tool steel?
Carbon steel is a generic term for steel alloys containing primarily iron and carbon. Tool steel, on the other hand, is a specific type of steel alloy designed for cutting and forming tools. Tool steels often contain additional alloying elements that enhance their performance, such as chromium, vanadium, tungsten, and molybdenum.
How is tool steel made?
Tool steel is produced through a complex process involving melting, casting, forging, and heat treatment. The specific manufacturing process varies depending on the type of tool steel and its intended application.
What is the hardest tool steel?
The hardness of tool steel depends on its composition and heat treatment. High-speed steels, particularly those with high tungsten and molybdenum content, are known for their exceptional hardness, especially at elevated temperatures. However, the specific hardest tool steel will depend on the specific application and the desired properties.
Can tool steel be welded?
Yes, tool steel can be welded, but it requires specialized welding techniques and filler metals to prevent cracking and distortion. The weldability of tool steel depends on its composition and the specific welding process used.