Welcome to My Blog! 🌟
Before we dive into the content, I’d love for you to join me on my social media platforms. It’s where I share more insights, engage with our vibrant community, and post regular updates. Here’s how you can stay connected:
📘 Facebook: Connect with me on Facebook
Now, let’s embark on this journey together. I hope you find the content here insightful, engaging, and most importantly, valuable. Let’s explore, learn, and grow together! 🚀
Table of Contents
Introduction
Choosing the right material for industrial tools is crucial for performance, cost-efficiency, and durability. One essential resource that professionals often rely on is the tool steel grades chart. This chart provides critical information about different grades of tool steel and helps users compare their properties, applications, and limitations. Tool steel is specifically formulated to withstand high pressure, temperature, and wear, making it vital in manufacturing processes like cutting, stamping, and forming. In this article, we will explore ten key insights that will help you understand and utilize the tool steel grades chart effectively.
Understanding Tool Steel and Its Classifications
Tool steel is a specialized category of carbon and alloy steels formulated for use in tooling applications such as cutting, shaping, stamping, and forming. Its hallmark characteristics include exceptional hardness, superior abrasion resistance, and an ability to maintain a sharp cutting edge even under high stress. These attributes make it a preferred choice in a wide range of industries including automotive, aerospace, die casting, metal stamping, and plastic molding.
The classification of tool steel is primarily based on how it responds to heat treatment and its intended use. Below are the most common classifications:
- Water-hardening (W-grade): These are the most cost-effective tool steels, hardened by quenching in water. They exhibit high hardness but lower resistance to heat and shock, making them suitable for light-duty applications.
- Cold-work tool steels (O, A, and D grades): Designed for operations performed at room temperature, these steels are known for their toughness and wear resistance. For instance, O1 (oil-hardening) is easy to machine, A2 (air-hardening) offers good dimensional stability, and D2 provides high wear resistance due to its high carbon and chromium content.
- Hot-work tool steels (H grades): These are specifically formulated to withstand high temperatures and thermal cycling. Commonly used in forging, extrusion, and die casting, grades like H13 offer both strength and heat resistance under extreme operating conditions.
- High-speed tool steels (T and M grades): As the name implies, these steels can cut materials at high speeds while maintaining hardness. T-grade (tungsten-based) and M-grade (molybdenum-based) are used in drills, taps, and end mills where heat buildup is considerable.
- Shock-resistant tool steels (S grades): S-grade steels are engineered to absorb shock and impact loads, making them suitable for punches, chisels, and hammers.
Each classification is tailored to specific industrial requirements, which is why understanding the tool steel grades chart is critical for effective material selection.
Why the Tool Steel Grades Chart Is Essential
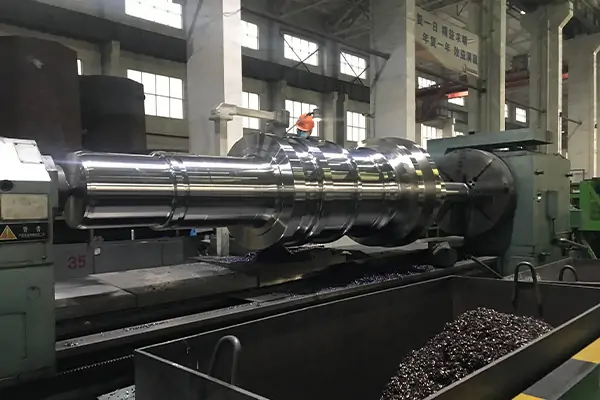
Selecting the right tool steel can be a complex decision influenced by many operational variables, including the environment in which the tool will operate, the type of load it will bear, and how frequently it will be used. This is where the tool steel grades chart becomes an invaluable resource.
The chart compiles a comprehensive set of mechanical and physical properties of each grade, allowing engineers, designers, and procurement teams to quickly compare materials. Some of the critical parameters typically featured in such a chart include:
- Hardness: Measured in the Rockwell C scale (HRC), hardness is a key determinant of a tool’s wear resistance and cutting efficiency. For example, D2 can reach up to 62 HRC, making it ideal for cutting tools and dies.
- Toughness: This refers to the material’s ability to absorb energy and deform without fracturing. Grades like S7 offer excellent toughness, making them suitable for high-impact applications.
- Wear resistance: High chromium tool steels like D2 or M4 exhibit excellent resistance to abrasive wear, extending the life of tools that operate in harsh environments.
- Heat resistance: Hot-work steels such as H13 retain strength at elevated temperatures, which is essential for operations like die casting or hot forging.
- Machinability: While some tool steels offer incredible performance, they can be difficult to machine. The chart helps identify grades like O1 that balance performance with ease of manufacturing.
Having all this data in a single reference like the tool steel grades chart helps eliminate guesswork and reduces the risk of tool failure due to poor material selection. For instance, if you’re manufacturing a cold-forming die that requires both dimensional stability and wear resistance, consulting the chart would guide you to choose A2 or D2 rather than an unsuitable hot-work grade.
Moreover, the chart is often updated with modern alloy developments and new treatments, reflecting the evolving landscape of materials science and manufacturing technology. Engineers and buyers who reference the tool steel grades chart regularly are better positioned to make informed decisions, reduce downtime, and optimize tool performance in real-world applications.
Tool Steel Grades Chart: Key Comparisons
Below is a simplified tool steel grades chart that outlines several commonly used tool steels, along with their key attributes:
Grade | Type | Hardness (HRC) | Toughness | Wear Resistance | Heat Resistance | Applications |
---|---|---|---|---|---|---|
W1 | Water-hardening | 50-60 | Moderate | Moderate | Low | Hand tools, dies |
A2 | Cold-work | 57-62 | High | High | Moderate | Punches, dies, blanking tools |
D2 | Cold-work | 58-64 | Moderate | Very High | Moderate | Molds, cutting tools |
H13 | Hot-work | 44-53 | High | Moderate | Very High | Hot dies, forging dies |
M2 | High-speed | 60-66 | Low | High | High | Drills, taps, milling tools |
S7 | Shock-resistant | 54-58 | Very High | Low | Moderate | Shears, chisels, jackhammer |
This chart helps decision-makers quickly identify a steel grade that balances all required characteristics for their particular operation.
Common Mistakes When Using the Tool Steel Grades Chart
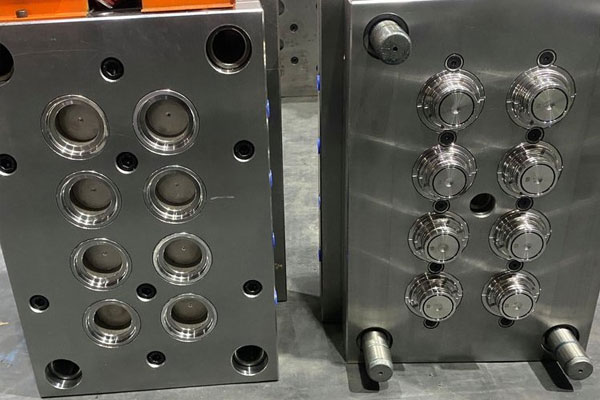
Misinterpreting the data in a tool steel grades chart can lead to suboptimal material selection. Some frequent errors include:
Overlooking Heat Treatment Effects
Heat treatment can drastically change the hardness and toughness of a steel grade. Failing to account for post-processing can lead to premature tool failure.
Ignoring Application Environment
Using a high-hardness tool steel in a shock-heavy environment can result in chipping. For example, using D2 in an impact application instead of S7 is a common misstep.
Misunderstanding Trade-offs
A grade with extremely high wear resistance often has lower toughness. It is essential to balance requirements to avoid tool breakage.
How to Use the Tool Steel Grades Chart Effectively
To make the most of the tool steel grades chart, follow these steps:
- Define the application requirements — including type of work, material being worked on, and operational stress.
- Identify the top priorities — is wear resistance more important than toughness?
- Match the properties — use the chart to find grades that meet or exceed your requirements.
- Consult with metallurgists — when in doubt, it’s always wise to double-check with experts.
- Prototype and test — small-scale trials can validate your selection before full production.
Advanced Insights for Engineers and Designers
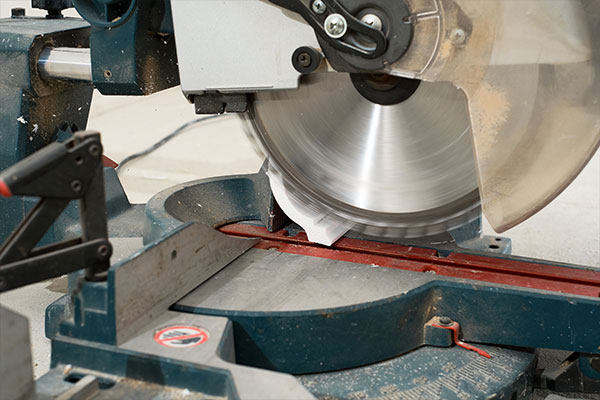
Engineers dealing with complex manufacturing setups often need more nuanced information. Some additional considerations include:
- Tool geometry and steel grade must align — harder steels need optimized tool geometry to reduce stress concentration.
- Surface treatment compatibility — coatings like TiN and DLC interact differently depending on the steel grade.
- Grinding behavior — certain grades are more prone to burning or cracking during grinding.
Taking a systems-level approach will ensure long-term performance and reliability.
Conclusion
The tool steel grades chart is not just a table—it’s a decision-making asset. By understanding its details and comparing key attributes, you can make smarter decisions, reduce tool failure, and optimize performance. While the chart provides a strong starting point, practical experience and expert consultation remain essential for final decisions. Whether you’re working in automotive, aerospace, or general manufacturing, knowing how to leverage the tool steel grades chart is a professional advantage.
FAQ
What is the most wear-resistant tool steel?
D2 is among the most wear-resistant tool steels, making it ideal for cutting and forming applications.
How is hardness measured in tool steel?
Hardness is typically measured using the Rockwell Hardness Scale (HRC), which is shown in most charts.
Is hot-work tool steel good for high temperatures?
Yes, hot-work steels like H13 are specifically designed for high-temperature operations such as die casting.
Can tool steel be used without heat treatment?
Some grades like O1 can be used with minimal treatment, but optimal performance usually requires proper heat treatment.
How often should I refer to the tool steel grades chart?
Each time you face a new application or performance issue, revisiting the chart ensures you’re using the right material.