Introduction
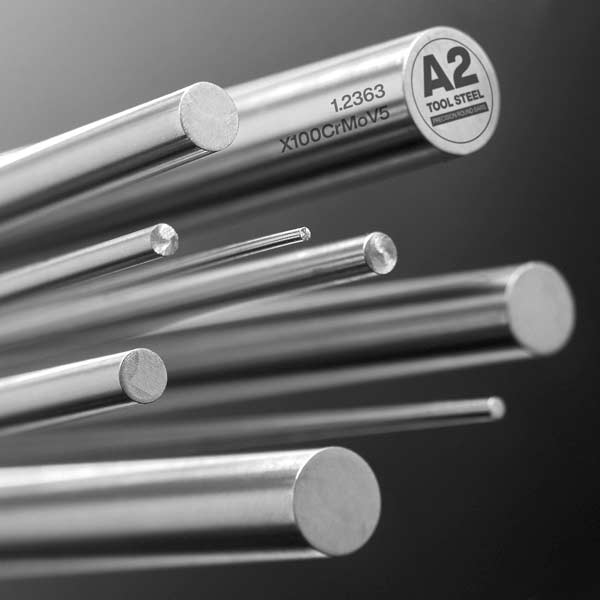
Tool steel A2 is a versatile, air-hardening chromium alloy tool steel that has earned a prominent position in various industries. Renowned for its exceptional balance of toughness and wear resistance, A2 is a preferred choice for manufacturers seeking a reliable and cost-effective tool steel solution. This comprehensive guide delves into the intricate details of tool steel A2, exploring its properties, applications, and other critical characteristics.
Understanding the Composition and Properties of Tool Steel A2
Tool steel A2 is an alloy steel meticulously crafted with an approximate composition of 1% carbon, 5% chromium, and 1% molybdenum. This specific elemental blend bestows A2 with a unique set of properties that make it suitable for a diverse range of applications.
Key Properties of Tool Steel A2:
- Exceptional Toughness: A2 exhibits superior toughness, rendering it highly resistant to fractures and chipping, even under demanding operating conditions.
- Excellent Wear Resistance: The strategic inclusion of chromium significantly enhances the wear resistance of A2, prolonging tool life and reducing maintenance requirements.
- Good Machinability: In its annealed state, A2 demonstrates excellent machinability, streamlining manufacturing processes and reducing production costs.
- Good Dimensional Stability: A2 possesses exceptional dimensional stability, minimizing distortion during heat treatment and ensuring precise component dimensions.
- Air-Hardening Capability: A2 can be effectively hardened through simple air cooling, eliminating the need for complex quenching oil treatments.
Applications of Tool Steel A2
The remarkable properties of tool steel A2 have made it indispensable in numerous industries. Some of the most common applications of tool steel A2 include:
- Cutting Tools: A2 is widely used in the manufacturing of various cutting tools, such as knives, punches, dies, and shear blades. Its exceptional toughness and wear resistance ensure optimal performance and longevity.
- Molds and Dies: A2 is frequently employed in the production of molds and dies for plastic injection molding, forging, and extrusion processes. Its dimensional stability and resistance to wear contribute to the production of high-quality components.
- Jigs and Fixtures: A2 is well-suited for the fabrication of jigs and fixtures, such as clamps, gauges, and holding devices. Its durability and precision make it an ideal choice for these critical manufacturing tools.
- Automotive Components: A2 finds application in the production of various automotive components, including gears, shafts, and other wear-resistant parts. Its excellent mechanical properties ensure the reliability and longevity of these components.
- Aerospace Components: A2 is utilized in the manufacturing of aerospace components, such as fasteners, bearings, and structural parts. Its high strength-to-weight ratio and resistance to fatigue make it a suitable choice for demanding aerospace applications.
Heat Treatment of Tool Steel A2
The heat treatment process for tool steel A2 is a critical step in optimizing its properties. It typically involves the following stages:
- Annealing: The steel is subjected to a controlled heating and cooling cycle to soften it for subsequent machining operations.
- Hardening: The steel is heated to a specific temperature, known as the austenitizing temperature, and then rapidly cooled, typically in air, to achieve the desired hardness.
- Tempering: The hardened steel is reheated to a lower temperature to alleviate internal stresses and improve toughness.
Advantages of Using Tool Steel A2
- Cost-Effective: A2 is generally more cost-effective compared to other tool steels with similar properties, making it an attractive option for various applications.
- Versatility: A2’s exceptional balance of properties makes it suitable for a wide range of applications, enhancing its versatility and flexibility.
- Good Machinability: The excellent machinability of A2 in its annealed state significantly reduces machining time and costs.
- Excellent Balance of Properties: A2 offers an optimal combination of toughness and wear resistance, making it a reliable choice for demanding applications.
Disadvantages of Using Tool Steel A2
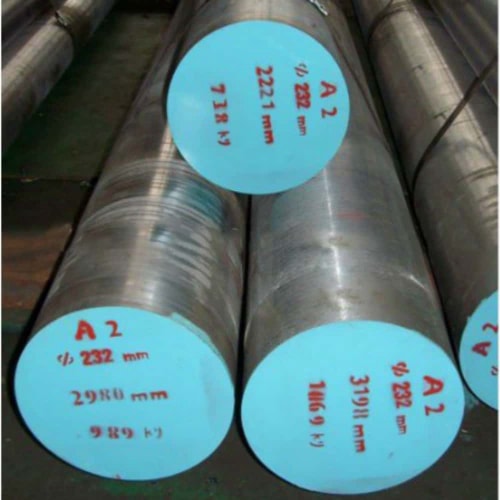
- Lower Wear Resistance Compared to Some Other Tool Steels: While A2 offers good wear resistance, it may not be the ideal choice for applications requiring extremely high wear resistance. Other tool steels, such as D2, may be more suitable in such cases.
- Susceptibility to Corrosion: A2 is not as corrosion-resistant as stainless steels. In corrosive environments, additional protective measures may be necessary to prevent corrosion.
Conclusion
Tool steel A2 is a versatile and cost-effective material that offers an exceptional balance of toughness and wear resistance. Its wide range of applications and ease of use make it a popular choice for manufacturers in various industries. By understanding the properties, applications, and heat treatment of tool steel A2, engineers and designers can make informed decisions when selecting materials for their projects.
FAQ
What is the difference between A2 and D2 tool steel?
While both A2 and D2 tool steels are popular choices for various applications, they differ in their composition and properties. A2 tool steel is primarily known for its toughness and wear resistance, making it suitable for cutting tools, molds, and dies. D2 tool steel offers superior wear resistance and edge retention, making it ideal for high-stress applications like punches, dies, and forming tools.
How is A2 tool steel hardened?
A2 tool steel is typically hardened through a process called air hardening. This involves heating the steel to a specific temperature (austenitizing temperature) and then allowing it to cool naturally in air. This process transforms the steel’s microstructure, resulting in increased hardness and strength.
Can A2 tool steel be welded?
Yes, A2 tool steel can be welded. However, it’s important to use proper welding techniques and post-weld heat treatment to maintain the steel’s mechanical properties. Welding can affect the microstructure and hardness of the steel, so careful consideration is necessary.
How do I select the right tool steel for my application?
Selecting the right tool steel for a specific application requires careful consideration of factors such as the required hardness, toughness, wear resistance, and corrosion resistance. A2 tool steel is a versatile choice for many applications, but it’s essential to assess the specific needs of your project. Consulting with a materials engineer or a tool steel supplier can help you make an informed decision.