Welcome to My Blog!
Before we dive into the content, I’d love for you to join me on my social media platforms where I share more insights, engage with the community, and post updates. Here’s how you can connect with me:
Facebook:https://www.facebook.com/profile.php?id=100087990137347
LinkedIn:https://www.linkedin.com/company/89825762/admin/dashboard/
YouTube:www.youtube.com/@carbonsteelsupply-kj9lw
TikTok:www.tiktok.com/@carbonsteelsupply
Now, let’s get started on our journey together. I hope you find the content here insightful, engaging, and valuable.
Introduction
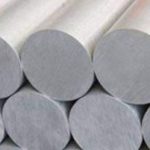
A11 Tool Steel is a high-performance steel known for its exceptional wear resistance and toughness. It is commonly used in applications where durability is crucial, such as in the manufacturing of cutting tools, dies, and molds. This comprehensive guide will explore the properties and best uses of A11 Tool Steel, offering insight into why it is a preferred choice in various industries. We’ll also provide answers to frequently asked questions and present information in a structured format, including tables for easy reference.
What is A11 Tool Steel?
A11 Tool Steel, also known as CPM A11, is a high-alloy steel produced using powder metallurgy technology. It has a unique combination of hardness, wear resistance, and toughness that makes it ideal for use in harsh environments where traditional steels might fail. A11 Tool Steel is primarily used for tools that require high wear resistance, such as cutting tools, cold-work tooling, and molds.
Key Properties of A11 Tool Steel:
- Hardness: High hardness levels after heat treatment, making it suitable for tough applications.
- Wear Resistance: Exceptional resistance to abrasive wear, ideal for extended tool life.
- Toughness: Maintains toughness even under stress, minimizing the risk of cracking.
- Machinability: Moderate machinability; requires specialized tools for efficient processing.
Chemical Composition of A11 Tool Steel
The chemical composition of A11 Tool Steel is crucial in determining its properties. The steel is alloyed with elements like carbon, chromium, vanadium, and molybdenum, which contribute to its high wear resistance and hardness.
Element | Percentage (%) |
---|---|
Carbon | 2.45 |
Chromium | 5.25 |
Vanadium | 9.75 |
Molybdenum | 1.30 |
Tungsten | 0.5 |
Cobalt | 0.5 |
This specific combination of elements gives A11 Tool Steel its unique characteristics, making it an ideal choice for applications that demand a balance of wear resistance and toughness.
Applications of A11 Tool Steel
A11 Tool Steel is used in a wide range of industries, including manufacturing, automotive, and metalworking. The following sections explore some of the most common applications of A11 Tool Steel:
Cutting Tools
A11 Tool Steel is frequently used to manufacture cutting tools such as saw blades, milling cutters, and end mills. The high wear resistance of the steel ensures that these tools maintain their sharpness for extended periods, reducing the need for frequent replacements and sharpening.
Dies and Molds
Cold-work dies and molds benefit greatly from A11 Tool Steel’s toughness and wear resistance. It is used for forming, blanking, and stamping operations where the tooling faces constant stress and abrasion. The steel’s properties help extend the lifespan of the dies, providing cost savings in high-production environments.
Punches and Forming Tools
Punches and forming tools made from A11 Tool Steel are able to withstand the impact and stress of repetitive operations. Its toughness reduces the risk of tool failure and cracking, making it a reliable material for these applications.
Heat Treatment of A11 Tool Steel
Heat treatment is essential for optimizing the performance of A11 Tool Steel. The process involves heating the steel to specific temperatures and then cooling it under controlled conditions to achieve the desired hardness and wear resistance. Below is a table summarizing the heat treatment process for A11 Tool Steel:
Heat Treatment Process | Temperature Range | Outcome |
---|---|---|
Preheating | 500–800°C (932–1472°F) | Prepares the steel for hardening |
Austenitizing | 1020–1050°C (1868–1922°F) | Achieves high hardness |
Quenching | Oil or air quench | Maximizes hardness and strength |
Tempering | 510–560°C (950–1040°F) | Balances toughness and hardness |
The heat treatment process is vital for unlocking the full potential of A11 Tool Steel. When properly treated, the steel can achieve a hardness level of up to 64 HRC, making it suitable for even the most demanding applications.
Advantages of Using A11 Tool Steel
A11 Tool Steel offers several advantages that make it a preferred choice for high-wear environments:
Superior Wear Resistance
One of the primary benefits of A11 Tool Steel is its exceptional wear resistance. This property makes it suitable for applications where tools and components are subject to constant abrasion and stress. The high vanadium content in the steel helps maintain this wear resistance, even at high hardness levels.
High Toughness
Despite its hardness, A11 Tool Steel maintains good toughness, allowing it to resist cracking and chipping under stress. This balance of hardness and toughness is crucial for tooling applications where impact resistance is essential.
Long Tool Life
Tools made from A11 Tool Steel often have extended lifespans compared to those made from other tool steels. This is particularly important in manufacturing settings where downtime for tool replacement can be costly.
Challenges in Using A11 Tool Steel
While A11 Tool Steel offers numerous benefits, there are some challenges associated with its use:
Difficulty in Machining
A11 Tool Steel’s high hardness and wear resistance can make it challenging to machine. Specialized cutting tools and techniques are required to process the steel efficiently without causing tool wear or damage. Using coated carbide or cubic boron nitride (CBN) tools is recommended for machining A11 Tool Steel.
Heat Treatment Sensitivity
The heat treatment process for A11 Tool Steel must be carefully controlled to achieve the desired properties. Inconsistent heat treatment can lead to variations in hardness and toughness, affecting the steel’s performance.
Cost Considerations
A11 Tool Steel is more expensive than other tool steels due to its alloying elements and production process. However, its durability and wear resistance often justify the initial investment, especially in high-production environments where long tool life is critical.
Maintenance and Care for A11 Tool Steel
Proper maintenance and care are essential to maximize the lifespan and performance of A11 Tool Steel tools and components. Here are some tips for maintaining A11 Tool Steel:
Proper Lubrication
Using the correct lubrication during machining and operational processes is vital for reducing friction and wear. High-performance lubricants designed for hard tool steels can help minimize tool wear and extend life.
Regular Inspection
Tools and components made from A11 Tool Steel should be regularly inspected for signs of wear, chipping, or cracking. Early detection of issues allows for timely maintenance and prevents catastrophic failures.
Proper Storage
Storing A11 Tool Steel tools and components in a clean, dry environment is important to prevent corrosion. Although A11 Tool Steel has some corrosion resistance, exposure to moisture can still lead to rust over time.
Future Trends in A11 Tool Steel Applications
The future of A11 Tool Steel in various industries looks promising as advancements in heat treatment and alloying techniques continue to enhance its properties. Here are some emerging trends:
Advanced Coatings
Applying advanced coatings to A11 Tool Steel can further improve its performance, particularly in terms of wear and corrosion resistance. Coatings such as TiN (Titanium Nitride) and DLC (Diamond-Like Carbon) are being explored to enhance the longevity and efficiency of A11 Tool Steel tools.
Additive Manufacturing
The integration of additive manufacturing (3D printing) technology with A11 Tool Steel offers the potential for creating complex tool geometries with optimized properties. Powder metallurgy techniques are being developed to allow A11 Tool Steel to be used in 3D printing processes, enabling faster production times and reduced waste.
Conclusion
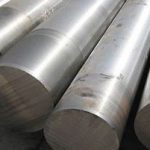
A11 Tool Steel is a versatile and high-performance material widely used in industries that demand durability and wear resistance. From cutting tools and dies to forming tools and punches, A11 Tool Steel’s properties make it an ideal choice for applications where traditional steels may fail. While there are challenges in machining and heat treatment, the benefits of using A11 Tool Steel often outweigh these difficulties, especially when long tool life and reliability are essential.
FAQ
Q1: What is A11 Tool Steel used for?
A1: A11 Tool Steel is used for manufacturing cutting tools, dies, molds, punches, and forming tools where high wear resistance and toughness are essential.
Q2: How hard can A11 Tool Steel get after heat treatment?
A2: A11 Tool Steel can reach hardness levels up to 64 HRC after proper heat treatment, making it suitable for demanding applications.
Q3: Is A11 Tool Steel difficult to machine?
A3: Yes, due to its high hardness and wear resistance, A11 Tool Steel can be challenging to machine. Specialized tools such as coated carbide or CBN tools are recommended.