Introduction
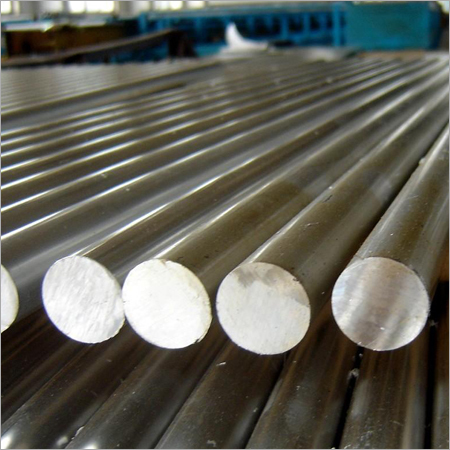
Tool steel round bars are essential components in various industries, offering exceptional strength, durability, and wear resistance for a wide range of applications. In this comprehensive guide, we’ll delve into everything you need to know about tool steel round bars, from their properties and characteristics to common uses, machining techniques, and maintenance practices.
Properties and Characteristics of Tool Steel Round Bars
Tool steel round bars are highly esteemed in various industries for their exceptional mechanical properties, which include not only high hardness, toughness, and wear resistance but also a host of other desirable characteristics. In this section, we will delve deeper into the realm of tool steel grades, exploring their diverse compositions and elucidating how these unique formulations contribute to their performance across a spectrum of applications.
Understanding Tool Steel Grades: Tool steel encompasses a broad range of alloy steels specifically engineered for use in tooling and machining applications. These steels are classified into distinct grades based on their chemical composition, microstructure, and intended use. By comprehending the nuances of each grade, manufacturers and engineers can make informed decisions regarding material selection to meet the demands of their specific applications.
Exploring Composition Variations: The composition of tool steel grades can vary significantly, with alloying elements such as carbon, chromium, vanadium, tungsten, and molybdenum playing pivotal roles in shaping their properties. For instance, higher carbon content enhances hardness and wear resistance, while chromium contributes to corrosion resistance and tempering stability. By analyzing the composition of different grades, stakeholders can gain insights into their inherent strengths and limitations.
Impact on Performance in Various Applications: The mechanical properties of tool steel grades have profound implications for their performance in diverse applications. For instance, high-speed tool steels excel in cutting and machining operations due to their superior hardness and heat resistance, while cold work tool steels are prized for their exceptional toughness and wear resistance in applications involving metal forming and shaping. By understanding how specific properties correlate with performance requirements, engineers can select the most suitable grade for their intended application.
Common Grades and Alloys of Tool Steel Round Bars
The world of tool steel encompasses a vast array of grades and alloys, each meticulously engineered to meet specific performance requirements in a variety of industrial applications. In this section, we will embark on a journey through some of the most common grades of tool steel, shedding light on their unique characteristics, strengths, and typical applications.
AISI D2: Renowned for its exceptional wear resistance and high hardness, AISI D2 tool steel is a popular choice for applications requiring cutting, shearing, and stamping. Its composition, which includes high levels of chromium and carbon, confers superior edge retention and abrasion resistance, making it well-suited for use in cold work tooling, such as blanking dies, forming dies, and thread rolling dies. Additionally, AISI D2 exhibits good dimensional stability and moderate toughness, further enhancing its suitability for demanding industrial environments.
AISI O1: AISI O1 tool steel is prized for its excellent machinability, dimensional stability, and wear resistance, making it a versatile option for a wide range of tooling applications. With a composition characterized by high carbon and chromium content, AISI O1 delivers impressive edge retention and surface finish quality, making it ideal for precision cutting, forming, and shaping operations. Common uses of AISI O1 include blanking and forming dies, punches, and gauges in industries such as automotive, aerospace, and manufacturing.
AISI A2: AISI A2 tool steel is celebrated for its exceptional toughness, impact resistance, and wear resistance, making it a preferred choice for applications involving heavy-duty machining and forming. Its composition, featuring high levels of chromium, molybdenum, and vanadium, imparts superior hardenability and heat resistance, enabling AISI A2 to withstand high-temperature operations without sacrificing toughness. Typical applications of AISI A2 include punches, dies, shear blades, and extrusion tooling in industries such as metal stamping, forging, and plastic molding.
Applications of Tool Steel Round Bars
Tool steel round bars serve as indispensable components across a multitude of industries, owing to their exceptional strength, durability, and versatility. In this section, we’ll delve deeper into the myriad of applications where tool steel round bars find widespread use, highlighting their crucial role in driving innovation and efficiency across diverse sectors.
Tool and Die Making: Tool steel round bars are the backbone of tool and die making processes, where precision and durability are paramount. These bars are utilized to craft a wide range of tools and dies, including cutting tools, punches, dies, and molds. Their high hardness, wear resistance, and dimensional stability ensure that these tools can withstand the rigors of repetitive use and maintain tight tolerances over extended periods, making them indispensable for manufacturing operations.
Mold Making: In the field of mold making, tool steel round bars play a pivotal role in the fabrication of injection molds, extrusion dies, and compression molds for various industries such as automotive, consumer goods, and electronics. The superior machinability and surface finish of tool steel round bars enable manufacturers to produce intricate mold cavities and intricate part geometries with exceptional precision and efficiency, facilitating the mass production of high-quality components.
Machining: Tool steel round bars are extensively used in machining applications, where they are employed to create cutting tools, lathe tools, milling cutters, and drill bits. Their high hardness, toughness, and wear resistance allow these tools to withstand the extreme forces and temperatures generated during metal cutting and shaping processes, ensuring precise and efficient material removal across a wide range of materials, including metals, plastics, and composites.
Machining Techniques for Tool Steel Round Bars
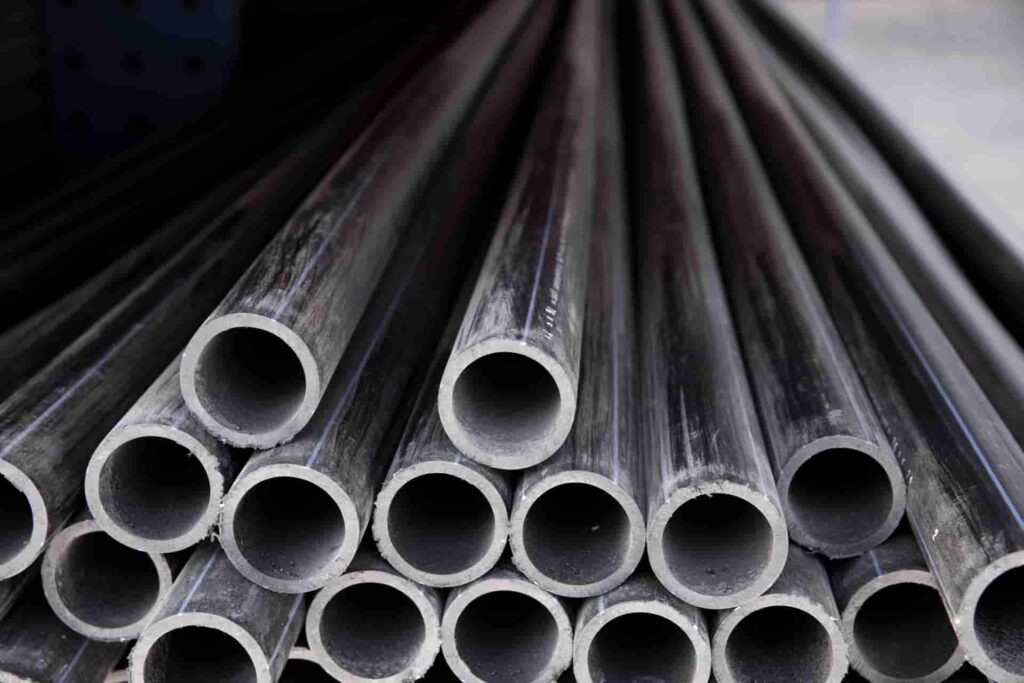
Machining tool steel round bar is a nuanced process that requires precision, expertise and the application of advanced technology to achieve the required dimensional accuracy and surface finish. In this section, we will delve into the complexities of machining tool steel round bar, exploring common techniques such as turning, milling, drilling, etc., while highlighting best practices for achieving the best results.
Turning: Turning is a fundamental machining operation that involves rotating a tool against a stationary workpiece to remove material and create cylindrical shapes. When turning tool steel round bars, it’s essential to use sharp cutting tools with appropriate geometries and cutting parameters to minimize heat generation and tool wear. Additionally, maintaining proper cutting speeds, feed rates, and depths of cut ensures smooth surface finishes and dimensional accuracy.
Milling: Milling is a versatile machining process that utilizes rotating cutting tools to remove material from the surface of a workpiece. When milling tool steel round bars, selecting the appropriate milling cutter, tool path, and cutting parameters is crucial for achieving precise profiles, contours, and surface finishes. High-speed steel (HSS) or carbide end mills are commonly used for milling tool steel, offering superior hardness and wear resistance to withstand the rigors of metal cutting.
Drilling: Drilling is a machining operation used to create holes in a workpiece using rotating cutting tools called drills. When drilling tool steel round bars, selecting the right drill bit geometry, cutting speed, and feed rate is essential to prevent tool breakage, minimize burrs, and achieve accurate hole dimensions. Coolant or lubricant may be used to dissipate heat and prolong tool life, particularly when drilling hardened tool steel grades.
Maintenance and Care of Tool Steel Round Bars
Proper maintenance is essential for prolonging the lifespan and performance of tool steel round bars. This section will cover maintenance practices such as storage, handling, cleaning, and corrosion prevention, ensuring that tool steel round bars remain in optimal condition for extended use.
Maintenance Practice | Description |
---|---|
Storage | Tool steel round bars should be stored in a clean, dry environment away from moisture and contaminants to prevent corrosion and surface damage. |
Handling | When handling tool steel round bars, use proper lifting equipment and techniques to prevent bending, twisting, or dropping, which can lead to surface defects. |
Cleaning | Regularly clean tool steel round bars using mild detergent and water to remove dirt, oil, and debris. Dry thoroughly and apply a light coat of rust inhibitor if necessary. |
Corrosion Prevention | Apply a corrosion inhibitor or protective coating to tool steel round bars when storing for extended periods or when exposed to corrosive environments. |
FAQ
Q: What are the advantages of using tool steel round bars?
A: Tool steel round bars offer superior mechanical properties, including high hardness, toughness, and wear resistance, making them ideal for applications requiring strength, durability, and precision.
Q: How do I choose the right grade of tool steel round bar for my application?
A: Consider factors such as the desired hardness, toughness, and wear resistance, as well as the specific requirements of your application. Consult with a materials engineer or supplier to determine the most suitable grade for your needs.
Q: Can tool steel round bars be heat treated?
A: Yes, tool steel round bars can undergo heat treatment processes such as annealing, hardening, and tempering to achieve desired mechanical properties and performance characteristics.
Conclusion
Tool steel round bars are indispensable components in modern manufacturing and engineering, offering unparalleled strength, durability, and versatility for a wide range of applications. By understanding their properties, common grades, applications, machining techniques, and maintenance practices, you can harness the full potential of tool steel round bars to optimize performance and productivity in your projects.