Introduction
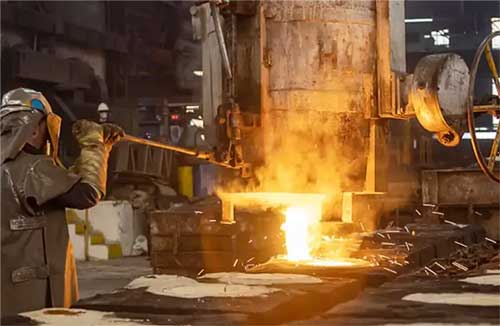
M2 tool steel round bar stands as a pinnacle in the realm of tool steels, revered for its exceptional properties, versatile uses, and numerous benefits across various industries. In this comprehensive guide, we will delve into the properties, uses, and benefits of M2 tool steel round bar, providing valuable insights for engineers, manufacturers, and enthusiasts alike.
Understanding M2 Tool Steel: Properties and Composition
M2 tool steel is a high-speed steel known for its outstanding wear resistance, toughness, and heat resistance. Its composition primarily consists of tungsten, molybdenum, vanadium, carbon, and chromium, imparting exceptional hardness and durability to the material.
Element | Composition (%) |
---|---|
Tungsten (W) | 5.50 – 6.75 |
Molybdenum (Mo) | 4.50 – 5.50 |
Vanadium (V) | 1.75 – 2.20 |
Carbon (C) | 0.78 – 1.05 |
Chromium (Cr) | 3.75 – 4.50 |
Manganese (Mn) | 0.15 – 0.40 |
Silicon (Si) | 0.20 – 0.45 |
Sulfur (S) | 0.03 max |
Phosphorus (P) | 0.03 max |
Applications of M2 Tool Steel Round Bar
M2 tool steel round bar is highly valued across a wide range of industries due to its exceptional properties and performance characteristics. Known for its high-speed capabilities, M2 tool steel is widely used in the manufacture of cutting tools such as drills, end mills, and reamers. Its ability to maintain sharp cutting edges, even under high temperatures, makes it an ideal choice for machining applications that require precision and durability.
In addition to cutting tools, M2 tool steel is also extensively utilized in the production of punches, dies, and forming tools. Its superior hardness and wear resistance enable it to perform efficiently in demanding environments, ensuring long tool life and consistent performance. The material’s toughness and resistance to abrasion further enhance its suitability for applications involving heavy-duty operations and high-speed machining.
Moreover, M2 tool steel round bars are frequently employed in the aerospace, automotive, and manufacturing industries, where reliable and robust tooling solutions are essential. The steel’s capability to endure extreme conditions without compromising on performance ensures that it meets the rigorous demands of these sectors. As a result, M2 tool steel continues to be a preferred material for professionals seeking high-performance tooling solutions that deliver both efficiency and longevity.
Benefits of M2 Tool Steel Round Bar
The benefits of M2 tool steel round bar are manifold, making it a preferred choice for numerous engineering and manufacturing applications. Its exceptional hardness and wear resistance significantly extend tool life, thereby reducing the frequency of tool replacements and minimizing tooling costs. This durability translates into cost savings and increased efficiency for manufacturers, as the need for frequent maintenance or replacement is substantially lowered.
One of the standout features of M2 tool steel is its high heat resistance. This property is particularly crucial in high-speed machining operations, where tools are subjected to intense heat due to friction. M2 tool steel maintains its hardness and sharpness even at elevated temperatures, allowing for prolonged cutting performance and consistent precision in machining processes. This ability to withstand thermal stress without losing performance ensures that tools made from M2 steel can operate at higher speeds and feeds, improving overall productivity.
Additionally, M2 tool steel exhibits excellent toughness and impact resistance, making it suitable for applications that involve heavy-duty cutting and shaping operations. Its resilience under stress prevents cracking and chipping, further extending the lifespan of tools. This robustness makes M2 tool steel an ideal material for manufacturing a wide range of tools, including drills, taps, end mills, saw blades, punches, and dies.
Machining and Heat Treatment of M2 Tool Steel Round Bar
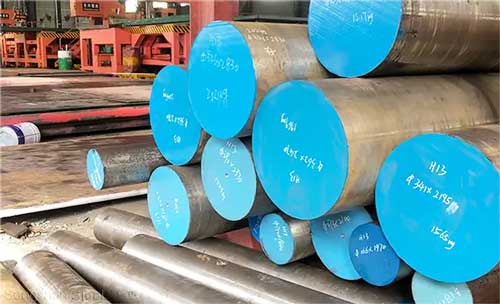
Machining M2 tool steel round bar demands meticulous attention to cutting parameters and tooling techniques due to its inherent high hardness and abrasiveness. M2 tool steel, known for its exceptional wear resistance and toughness, presents significant challenges during machining, necessitating the use of robust tools and precise settings to achieve desired outcomes. To ensure optimal mechanical properties and performance, proper heat treatment is crucial. This process includes several stages: annealing, hardening, and tempering, each of which must be carefully controlled.
Annealing involves heating the M2 tool steel to a specific temperature to relieve internal stresses, soften the material, and improve its machinability. Following annealing, the hardening process is conducted, which entails heating the steel to a higher temperature and then rapidly cooling it, typically using oil or air quenching, to attain the desired hardness. Finally, tempering is performed by reheating the hardened steel to a lower temperature to enhance its toughness and reduce brittleness.
By adhering to the recommended heat treatment procedures, M2 tool steel can achieve a balanced combination of hardness, strength, and toughness, making it suitable for demanding applications. Table 2 outlines the specific parameters and steps involved in the heat treatment process for M2 tool steel, providing detailed guidance to achieve the best possible mechanical properties and performance characteristics.
FAQ
Q: What are the main properties of M2 tool steel round bar?
A: M2 tool steel round bar exhibits exceptional wear resistance, toughness, and heat resistance, making it ideal for high-speed machining applications.
Q: What industries commonly use M2 tool steel round bar?
A: M2 tool steel round bar finds applications in industries such as aerospace, automotive, manufacturing, and metalworking, among others.
Q: How does M2 tool steel round bar compare to other tool steels?
A: M2 tool steel round bar offers superior wear resistance and heat resistance compared to many other tool steels, making it ideal for demanding machining applications.
Q: What are the recommended machining and heat treatment techniques for M2 tool steel round bar?
A: Machining M2 tool steel round bar requires careful consideration of cutting parameters, tooling materials, and lubrication methods. Proper heat treatment, including annealing, hardening, and tempering, is essential to achieve optimal mechanical properties and performance characteristics.
Q: Where can I purchase M2 tool steel round bar?
A: M2 tool steel round bar is available from various suppliers and distributors specializing in high-speed steels and tooling materials. It is essential to source from reputable suppliers known for quality and reliability.
Conclusion
In conclusion, M2 tool steel round bar stands as a formidable material renowned for its exceptional properties, versatile applications, and numerous benefits in engineering and manufacturing. Its superior wear resistance, toughness, and heat resistance make it an indispensable choice for cutting tools, drills, and other high-speed machining applications. By understanding its properties, applications, and optimal processing techniques, engineers and manufacturers can unlock the full potential of M2 tool steel round bar in their projects.