Introduction
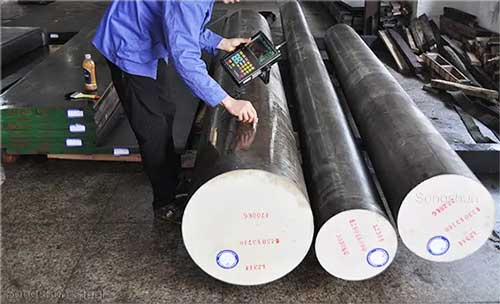
Cold work tool steels play a pivotal role in various industries where materials need to withstand mechanical stress, maintain sharp cutting edges, and resist wear and tear. Understanding their properties is crucial for selecting the right material for specific applications. In this comprehensive guide, we delve into the key properties of cold work tool steels, focusing on hardness, toughness, and corrosion resistance.
Understanding Cold Work Tool Steel
Cold work tool steels represent a specialized category of high-carbon steels engineered specifically for applications performed at or below room temperature. Renowned for their exceptional mechanical properties, including strength, hardness, and wear resistance, these steels are indispensable in a wide range of industrial processes such as cutting, stamping, and forming.
One of the key characteristics of cold work tool steels is their high carbon content, which contributes to their superior hardness and wear resistance. This elevated carbon content enables the formation of hard carbides within the steel matrix, enhancing its ability to withstand abrasion, deformation, and cutting forces encountered during cold working operations.
In addition to carbon, cold work tool steels often contain alloying elements such as chromium, molybdenum, vanadium, and tungsten. These alloying additions serve to further improve the steel’s mechanical properties, including toughness, edge retention, and resistance to deformation under load. For example, chromium contributes to enhanced corrosion resistance, while molybdenum and vanadium promote fine grain structure and improve hardenability.
The exceptional strength and wear resistance of cold work tool steels make them well-suited for demanding applications across various industries. In metalworking, they are widely employed in the production of cutting tools, dies, and molds used for shaping and machining metallic materials. Their ability to maintain sharp cutting edges and withstand heavy loads ensures efficient and precise machining operations.
Hardness: The Cornerstone of Cold Work Tool Steels
Hardness stands as a pivotal property within the realm of cold work tool steels, defining the material’s capacity to withstand deformation, indentation, and abrasion when subjected to applied pressure. This crucial characteristic not only dictates the steel’s suitability for specific applications but also determines its overall performance and longevity in service. A multitude of factors intricately interplay to influence the hardness of these steels, encompassing alloy composition, heat treatment regimen, and microstructural attributes.
Alloy composition serves as a foundational determinant of the hardness exhibited by cold work tool steels. By carefully controlling the presence and proportion of alloying elements such as carbon, chromium, vanadium, and tungsten, steel manufacturers tailor the steel’s mechanical properties to meet the demands of diverse applications. Carbon content, in particular, plays a pivotal role in enhancing hardness by facilitating the formation of carbides within the steel matrix, thereby bolstering its resistance to deformation and wear.
Equally significant is the role of heat treatment in modulating the hardness of cold work tool steels. Through controlled heating and cooling processes, such as quenching and tempering, the steel’s microstructure undergoes transformation, leading to the development of desirable mechanical properties, including hardness. Quenching involves rapid cooling of the steel from elevated temperatures, inducing a phase change that imparts hardness and strength to the material. Subsequent tempering serves to relieve internal stresses and refine the microstructure, balancing hardness with toughness to optimize performance.
Toughness: Balancing Strength with Durability
While hardness undoubtedly holds significant importance in cold work tool steels, it is imperative to recognize that toughness plays an equally vital role in determining the overall performance and reliability of these materials. Unlike hardness, which primarily focuses on a material’s resistance to indentation and deformation, toughness encompasses the ability of a material to absorb energy and undergo plastic deformation before fracturing. Achieving the right balance between hardness and toughness is paramount in cold work tool steels to prevent premature failure and ensure prolonged tool life in demanding operational environments.
Toughness serves as a critical property in cold work tool steels as it enables the material to withstand sudden impact or shock loads without fracturing. In applications where the tool is subjected to intermittent or cyclic loading, such as stamping or forming operations, toughness becomes particularly crucial in preventing catastrophic failure and maintaining dimensional stability over time. A high level of toughness allows the tool to absorb energy and deform plastically, thereby dissipating the impact forces and reducing the risk of crack initiation and propagation.
However, achieving optimal toughness in cold work tool steels often necessitates a careful balancing act with hardness. While hardness is desirable for enhancing wear resistance and maintaining sharp cutting edges, excessive hardness can sometimes compromise the material’s toughness and make it susceptible to brittle fracture. Conversely, excessively tough materials may exhibit inadequate wear resistance and poor dimensional stability, leading to accelerated tool wear and reduced precision in machining operations.
To strike the right balance between hardness and toughness, steel manufacturers employ various alloying elements and heat treatment techniques tailored to the specific requirements of the application. For instance, the addition of elements such as molybdenum, nickel, and silicon can enhance the toughness of cold work tool steels by promoting the formation of tough microstructural constituents, such as fine-grained ferrite or martensite-austenite (MA) islands. Additionally, optimizing the tempering process following quenching can help refine the steel’s microstructure, relieving residual stresses and improving its resistance to crack propagation while maintaining adequate hardness levels.
Corrosion Resistance: Protecting Against Deterioration
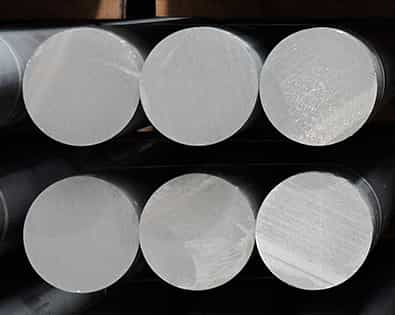
In addition to mechanical properties such as hardness and toughness, corrosion resistance holds paramount importance in the performance of cold work tool steels, particularly in environments characterized by exposure to moisture, chemicals, or harsh conditions. Cold work tool steels endowed with adequate corrosion resistance not only exhibit enhanced durability and longevity but also mitigate the risk of premature degradation, thereby minimizing the need for frequent maintenance and replacement.
Corrosion resistance is a critical consideration in applications where cold work tool steels are exposed to corrosive agents such as moisture, acids, alkalis, or other chemical substances. In such environments, unprotected steel surfaces are susceptible to corrosion, leading to surface degradation, material loss, and eventual failure of the tool. By incorporating corrosion-resistant alloys or surface treatments, cold work tool steels can effectively withstand the corrosive effects of these environments, ensuring prolonged service life and optimal performance.
Various factors contribute to the corrosion resistance of cold work tool steels, including alloy composition, surface finish, and environmental conditions. Alloying elements such as chromium, molybdenum, and nickel are commonly added to enhance corrosion resistance by forming a protective oxide layer on the steel surface, which acts as a barrier against corrosive agents. Additionally, specialized surface treatments such as electroplating, passivation, or coating with corrosion-resistant materials further improve the steel’s resistance to corrosion, providing an additional layer of protection against environmental degradation.
In industries such as aerospace, automotive, and marine engineering, where exposure to corrosive environments is prevalent, the selection of corrosion-resistant cold work tool steels is essential to ensure the longevity and reliability of critical components. For example, in aerospace applications, where tools are subjected to high humidity, saltwater exposure, and aggressive chemicals, corrosion-resistant cold work tool steels help maintain dimensional stability, precision, and performance over extended periods, reducing the risk of costly downtime and maintenance.
Furthermore, in industries such as food processing, pharmaceuticals, and chemical manufacturing, where hygiene and product purity are paramount, the use of corrosion-resistant cold work tool steels ensures compliance with stringent regulatory requirements and maintains the integrity of the end product. Tools and equipment fabricated from corrosion-resistant steels are less prone to contamination, surface pitting, or discoloration, thereby preserving product quality and consumer safety.
Comparative Analysis: Examining Different Grades
To better understand the diverse range of cold work tool steels available, let’s conduct a comparative analysis of several popular grades, including their chemical compositions, hardness values, toughness ratings, and corrosion resistance properties.
Grade | Chemical Composition | Hardness (HRC) | Toughness (J) | Corrosion Resistance |
---|---|---|---|---|
A2 | 1.00% C, 5.25% Cr, 1.00% Mo | 60-62 | 10-15 | Moderate |
D2 | 1.50% C, 11.50% Cr, 0.90% V | 58-60 | 15-20 | Moderate to High |
O1 | 0.90% C, 0.60% Mn, 1.00% Cr | 58-60 | 20-25 | Low to Moderate |
S7 | 0.50% C, 3.25% Cr, 1.30% Mo | 54-56 | 25-30 | Moderate |
FAQ
What factors influence the hardness of cold work tool steels?
The hardness of cold work tool steels is influenced by factors such as alloy composition, heat treatment, quenching, and tempering processes.
How does toughness differ from hardness?
Toughness refers to a material’s ability to withstand impact and deformation, whereas hardness measures its resistance to indentation and abrasion.
Why is corrosion resistance important in cold work tool steels?
Corrosion resistance helps protect tooling from deterioration caused by exposure to moisture, chemicals, and other corrosive substances, ensuring prolonged service life.
Can cold work tool steels be customized for specific applications?
Yes, manufacturers can tailor the chemical composition, heat treatment, and processing of cold work tool steels to meet the unique requirements of different applications.
How can I improve the performance of cold work tool steels?
Optimizing heat treatment processes, selecting the appropriate grade based on application requirements, and implementing proper maintenance practices can all contribute to enhancing the performance of cold work tool steels.
Conclusion
Cold work tool steels are indispensable materials in various industries, offering unparalleled hardness, toughness, and corrosion resistance. By understanding these properties and selecting the right grade for specific applications, manufacturers can enhance productivity, minimize downtime, and optimize performance.