Introduction
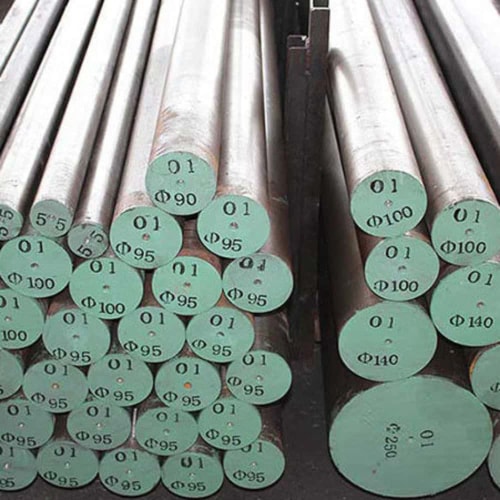
When it comes to tool manufacturing, the choice of materials can make or break the effectiveness and longevity of the final product. Among various tool steels available, O1 tool steel stands out due to its unique characteristics, particularly its hardness. In this blog, we will explore the significance of O1 tool steel hardness in detail, covering its properties, applications, and the crucial role it plays in the manufacturing process.
Understanding O1 Tool Steel
O1 tool steel is an oil-hardening, non-deforming steel known for its excellent wear resistance and ability to hold a sharp edge. The steel’s composition typically includes carbon, chromium, manganese, and molybdenum, making it an ideal choice for various tooling applications. Its unique properties contribute significantly to its hardness, which is a crucial factor for any tool’s performance and durability.
Chemical Composition of O1 Tool Steel
Element | Composition (%) |
---|---|
Carbon (C) | 0.90 – 1.00 |
Chromium (Cr) | 0.40 – 0.60 |
Manganese (Mn) | 0.60 – 0.90 |
Molybdenum (Mo) | 0.15 – 0.30 |
Vanadium (V) | < 0.10 |
Phosphorus (P) | < 0.03 |
Sulfur (S) | < 0.03 |
The Hardness of O1 Tool Steel
What is Hardness?
Hardness refers to a material’s ability to resist deformation, particularly permanent deformation, scratching, cutting, or wear. In the context of O1 tool steel, hardness is measured using several scales, including Rockwell and Brinell, which assess the material’s resistance to various forms of mechanical stress.
Measuring O1 Tool Steel Hardness
The hardness of O1 tool steel can be influenced by several factors, including the heat treatment process and the specific alloying elements present. Typically, O1 tool steel can achieve hardness levels ranging from 58 to 65 HRC (Rockwell Hardness C scale) after appropriate heat treatment.
Hardness Scale | O1 Tool Steel Hardness (HRC) |
---|---|
Rockwell C | 58 – 65 |
Brinell | 200 – 300 |
The Role of Hardness in Tool Performance
Durability and Wear Resistance
One of the primary reasons O1 tool steel is favored in tool manufacturing is its exceptional durability. Higher hardness levels directly correlate with increased wear resistance, allowing tools made from O1 steel to maintain their cutting edges longer, reducing the frequency of tool replacement.
Edge Retention
Another critical aspect of O1 tool steel hardness is edge retention. Tools that require precise cuts, such as knives and molds, benefit significantly from the ability of O1 steel to hold a sharp edge. This capability minimizes the need for frequent sharpening, leading to improved efficiency and reduced downtime in production environments.
Heat Treatment Process
Importance of Heat Treatment
Heat treatment is vital in achieving the desired hardness in O1 tool steel. This process typically involves several stages: hardening, quenching, and tempering. Each stage plays a significant role in ensuring the final hardness meets specific manufacturing requirements.
Stages of Heat Treatment for O1 Tool Steel
- Hardening: Heating the steel to a high temperature (around 800-850°C) to dissolve the carbides.
- Quenching: Rapidly cooling the steel using oil to lock in hardness.
- Tempering: Reheating to a lower temperature (around 150-200°C) to relieve stresses while maintaining hardness.
Applications of O1 Tool Steel
Common Uses in Tool Manufacturing
Due to its hardness and versatility, O1 tool steel is used in various applications, including:
- Cutting Tools: Drills, taps, and blades.
- Molds and Dies: Precision molds for injection molding and die-casting.
- Hand Tools: Chisels, punches, and knives.
Application Type | Examples | Hardness Requirements (HRC) |
---|---|---|
Cutting Tools | Drills, Taps | 58 – 64 |
Molds and Dies | Injection Molds | 60 – 65 |
Hand Tools | Chisels, Knives | 58 – 62 |
The Economic Impact of Hardness in Manufacturing
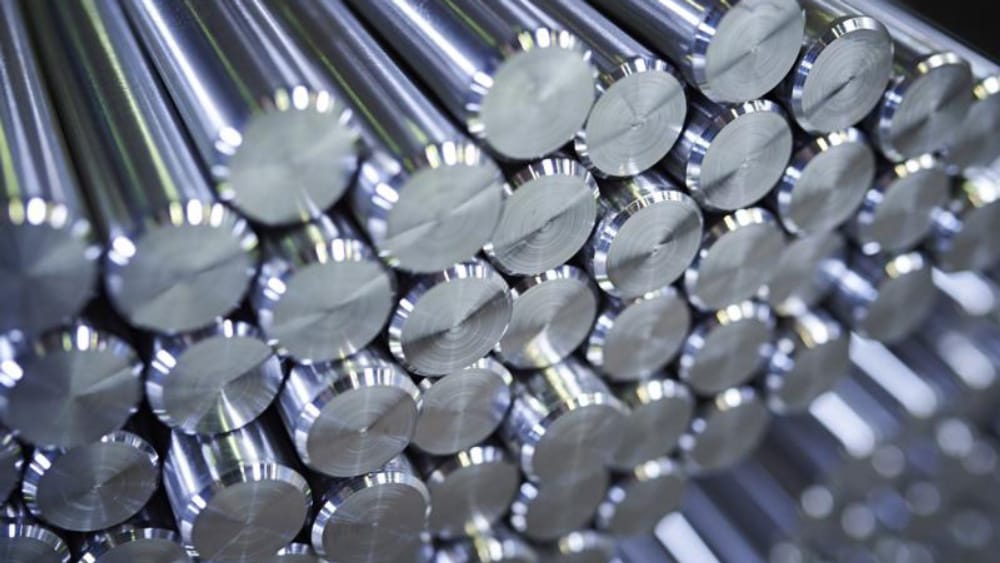
Cost Efficiency
Investing in O1 tool steel, despite its higher initial costs compared to lower-grade materials, often leads to long-term cost savings. The combination of durability and extended tool life can significantly reduce manufacturing costs over time.
Production Efficiency
Tools made from O1 steel reduce the need for frequent replacements and maintenance, contributing to overall production efficiency. This advantage allows manufacturers to focus on production without the constant need for tool changes, leading to higher output and reduced labor costs.
Conclusion
In summary, the hardness of O1 tool steel plays a fundamental role in tool manufacturing. Its unique properties ensure durability, wear resistance, and edge retention, making it a top choice for various applications. Understanding the importance of O1 tool steel hardness is crucial for manufacturers looking to produce high-quality tools that meet industry demands.
FAQ
Q:What is the hardness range of O1 tool steel?
A:O1 tool steel typically has a hardness range of 58 to 65 HRC after appropriate heat treatment.
Q:Why is hardness important in tool manufacturing?
A:Hardness is crucial because it determines a tool’s durability, wear resistance, and ability to retain a sharp edge, all of which are essential for efficient manufacturing.
Q:Can O1 tool steel be used for all types of tools?
A:While O1 tool steel is versatile, it is particularly suited for cutting tools, molds, and hand tools that require high hardness and wear resistance.
Q:How does heat treatment affect O1 tool steel hardness?
A:Heat treatment significantly affects hardness by altering the microstructure of the steel, allowing it to achieve the desired hardness levels through processes like hardening, quenching, and tempering.
Q:Is O1 tool steel expensive compared to other tool steels?
A:O1 tool steel is generally more expensive than lower-grade materials, but its long-term durability and efficiency often justify the initial investment.
Q:How should tools made from O1 tool steel be maintained?
A:Regular maintenance includes proper sharpening techniques and using appropriate storage methods to prevent damage and maintain edge integrity.
Q:What are some alternatives to O1 tool steel?
A:Alternatives to O1 tool steel include A2, D2, and M2 tool steels, each with different properties suited for specific applications, but may not offer the same balance of hardness and toughness as O1.