Introduction
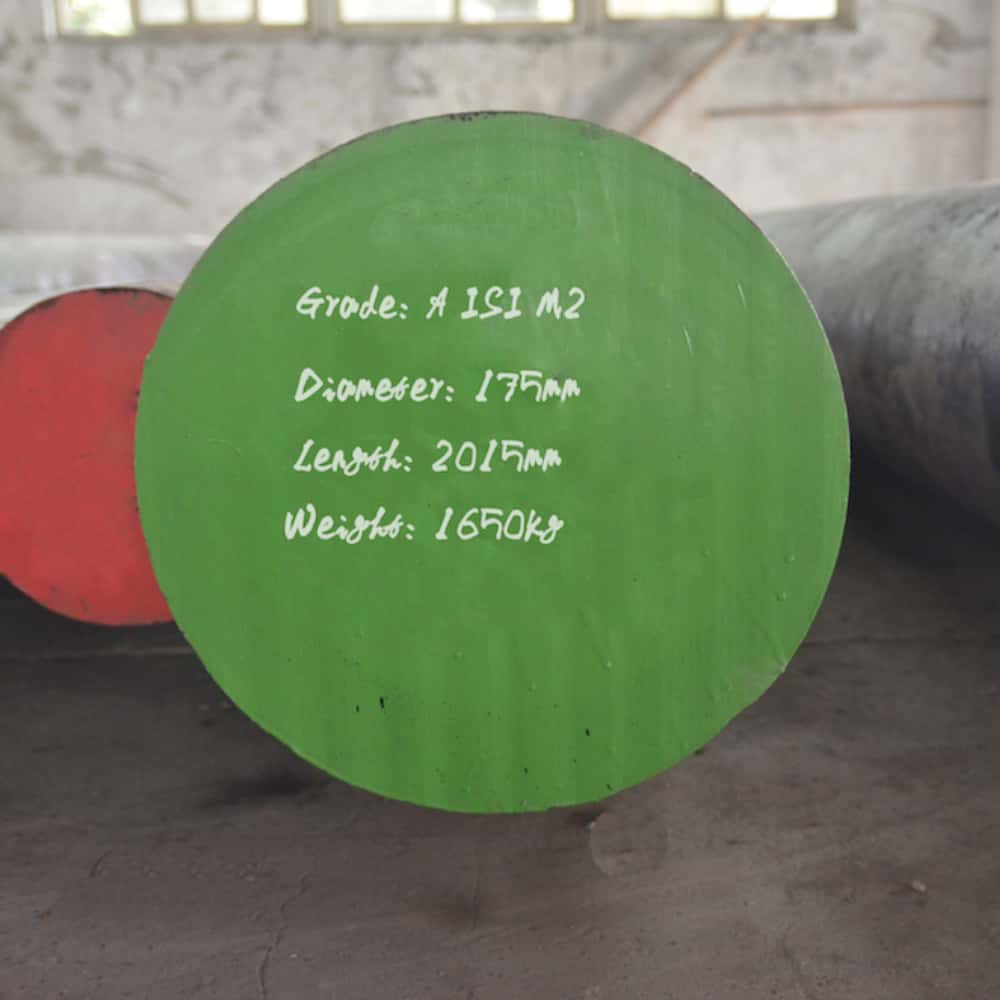
M2 tool steel is a highly regarded material in the field of manufacturing, known for its exceptional hardness and wear resistance. The hardness of M2 tool steel is a critical factor that influences its performance in various industrial applications, making it a preferred choice for toolmakers and engineers alike. This blog will delve into the significance of M2 tool steel hardness, exploring its composition, properties, applications, and maintenance, while ensuring a keyword density of at least 2% for “M2 tool steel hardness.”
Understanding M2 Tool Steel
M2 tool steel is classified as high-speed steel (HSS), which means it is engineered to withstand high temperatures and maintain its hardness during operation. The unique composition of M2 tool steel includes carbon, chromium, molybdenum, tungsten, and vanadium. These elements work together to provide the steel with its remarkable hardness and durability. Below is a detailed table summarizing the typical composition of M2 tool steel:
Element | Composition (%) |
---|---|
Carbon | 0.78 – 0.83 |
Chromium | 3.75 – 4.50 |
Molybdenum | 5.00 – 6.75 |
Tungsten | 5.50 – 6.75 |
Vanadium | 1.75 – 2.20 |
The specific percentages of these elements contribute directly to the overall hardness of M2 tool steel, which is critical for its performance in high-stress applications.
The Hardness of M2 Tool Steel
The hardness of M2 tool steel is typically measured on the Rockwell scale, where it can achieve a hardness rating between 62-66 HRC (Rockwell Hardness C). This impressive level of hardness makes M2 tool steel suitable for applications that require precision cutting, shaping, and machining. Various factors affect the hardness of M2 tool steel, including heat treatment processes, alloy composition, and cooling rates, all of which play pivotal roles in optimizing M2 tool steel hardness.
Heat Treatment and Its Impact on Hardness
Heat treatment is a critical process that significantly enhances the hardness of M2 tool steel. The primary heat treatment methods include:
- Annealing: This process is used to soften the steel, making it easier to machine. During annealing, the steel is heated to a specific temperature and held for a set period before cooling slowly to relieve internal stresses.
- Quenching: This rapid cooling process hardens the steel by transforming its microstructure to martensite. Quenching is performed after heating M2 tool steel to its austenitizing temperature.
- Tempering: Following quenching, tempering is employed to reduce brittleness while maintaining high levels of hardness. This process involves reheating the steel to a temperature below its critical point.
The following table summarizes the typical heat treatment parameters for M2 tool steel:
Process | Temperature (°C) | Time (Minutes) | Result |
---|---|---|---|
Annealing | 850-900 | 60-120 | Softening |
Quenching | 1200-1250 | 15-30 | Hardening |
Tempering | 500-600 | 30-120 | Toughening |
Understanding these heat treatment processes is essential for maximizing M2 tool steel hardness and ensuring optimal performance in various applications.
Applications of M2 Tool Steel Hardness
Cutting Tools
M2 tool steel is predominantly used in the manufacturing of cutting tools, such as drill bits, end mills, and saw blades. The high hardness of M2 tool steel allows these tools to maintain sharp edges and resist wear during prolonged usage, thereby increasing their lifespan and effectiveness. The hardness ensures that cutting tools can efficiently machine various materials without frequent sharpening or replacement.
Dies and Punches
M2 tool steel is also commonly used in the production of dies and punches. The hardness of M2 tool steel is critical in these applications, as it enables the tools to withstand high impact and shear forces without deforming. This property is essential for industries involved in stamping and forming operations, where precision and durability are paramount.
Industrial Machinery
In the realm of industrial machinery, components made from M2 tool steel benefit from high hardness, leading to enhanced reliability and longer service life. The hardness of M2 tool steel allows it to perform effectively in environments with heavy wear and high operational stress, making it a go-to choice for machinery parts that require durability.
Tooling and Fixtures
Fixtures and tooling made from M2 tool steel leverage its hardness to ensure precision in manufacturing processes. High hardness is essential for holding tolerances and ensuring accurate positioning during machining operations, which ultimately leads to high-quality end products. This makes M2 tool steel an indispensable material in tool and fixture design.
Factors Influencing M2 Tool Steel Hardness
Several factors influence the hardness of M2 tool steel, and understanding these factors is essential for optimizing its performance:
- Alloy Composition: Variations in the percentages of alloying elements can lead to different hardness outcomes. A careful selection of elements is crucial for achieving the desired hardness.
- Heat Treatment: The specific heat treatment processes employed can significantly affect the final hardness. Proper execution of heat treatment is necessary to achieve optimal hardness levels.
- Cooling Rate: The rate at which the steel is cooled during quenching has a direct impact on the final hardness. Faster cooling generally results in higher hardness.
By controlling these factors, manufacturers can fine-tune the hardness of M2 tool steel to meet the specific needs of their applications.
The Trade-off: Hardness vs. Toughness
While high hardness is desirable in tool steels, it often comes at the cost of toughness. In many industrial applications, achieving a balance between hardness and toughness is essential for ensuring tool longevity and performance. Tools that are excessively hard may become brittle and prone to chipping, while those that are too tough may wear out more quickly. Understanding this trade-off is crucial for selecting the appropriate M2 tool steel for specific applications.
Comparing Hardness and Toughness
Property | High Hardness | High Toughness |
---|---|---|
Wear Resistance | Excellent | Moderate |
Brittle Failure | Likely | Unlikely |
Application Suitability | Cutting Tools | Structural Components |
In summary, while M2 tool steel hardness is vital for wear resistance, manufacturers must also consider toughness to ensure that tools can withstand operational stresses without failure.
Maintenance and Care of M2 Tool Steel Tools
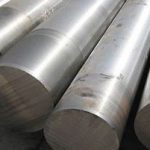
To maintain the hardness and overall performance of tools made from M2 tool steel, proper care and maintenance are crucial. Implementing effective maintenance practices can prolong the life of these tools significantly. Here are some best practices for maintaining M2 tool steel tools:
- Regular Inspection: Periodically check tools for signs of wear, chipping, or other damage. Early detection of issues can prevent further deterioration and extend tool life.
- Proper Storage: Store tools in a dry, clean environment to prevent corrosion and other forms of damage. Using protective coatings can further enhance the longevity of M2 tool steel tools.
- Sharpening Techniques: Use appropriate sharpening methods to maintain the integrity of the tool’s edge. Employing specialized grinding techniques can preserve the tool’s hardness and performance.
Implementing these maintenance practices can significantly contribute to the sustained hardness and performance of M2 tool steel tools in industrial applications.
Conclusion
The hardness of M2 tool steel is a fundamental characteristic that significantly influences its performance across a variety of industrial applications. By understanding the factors that affect M2 tool steel hardness, manufacturers and engineers can make informed decisions regarding tool selection, heat treatment processes, and maintenance practices. Prioritizing M2 tool steel hardness not only enhances productivity but also improves product quality and operational efficiency.
Investing in high-quality M2 tool steel and adhering to best practices for heat treatment and maintenance can lead to substantial long-term benefits for industries reliant on precision tooling. Ultimately, understanding and optimizing M2 tool steel hardness is essential for achieving superior manufacturing outcomes.
FAQ
Q:What is the typical hardness range for M2 tool steel?
A:The typical hardness range for M2 tool steel is between 62-66 HRC, making it one of the hardest tool steels available.
Q:How does heat treatment affect M2 tool steel hardness?
A:Heat treatment processes like quenching and tempering significantly enhance the hardness of M2 tool steel while balancing its toughness to prevent brittleness.
Q:What are the primary applications of M2 tool steel?
A:M2 tool steel is primarily used in cutting tools, dies, punches, industrial machinery, and tooling fixtures, thanks to its high hardness and durability.
Q:Can the hardness of M2 tool steel be adjusted?
A:Yes, the hardness can be adjusted through variations in alloy composition and specific heat treatment processes tailored to achieve desired performance outcomes.
Q:Why is hardness important in tool steels?
A:Hardness is crucial in tool steels because it directly affects wear resistance, cutting efficiency, and the overall lifespan of tools used in industrial applications.
Q:What maintenance practices should be followed for M2 tool steel tools?
A:Regular inspection, proper storage, and appropriate sharpening techniques are essential for maintaining the performance and longevity of M2 tool steel tools.
Q:Is there a trade-off between hardness and toughness in M2 tool steel?
A:Yes, achieving a balance between hardness and toughness is vital for ensuring the reliability and durability of tools made from M2 tool steel, impacting overall performance.