Introduction
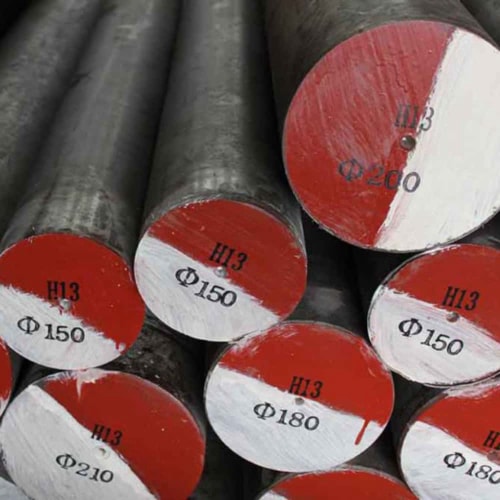
H13 tool steel is renowned for its exceptional performance in high-temperature applications. Its unique properties make it a favored choice among manufacturers of dies, molds, and tools. However, to unlock the full potential of H13, proper heat treatment is crucial. This blog delves into the importance of H13 tool steel heat treatment in tool manufacturing, exploring its benefits, processes, and best practices.
Understanding H13 Tool Steel
What is H13 Tool Steel?
H13 tool steel is a hot work tool steel that is often used in applications where high temperature and wear resistance are necessary. Composed mainly of chromium, molybdenum, and vanadium, H13 exhibits a good balance between toughness and hardness, making it ideal for various tool manufacturing applications.
Key Properties of H13 Tool Steel
Property | Value |
---|---|
Hardness (HRC) | 48-52 |
Tensile Strength (MPa) | 1,200-1,400 |
Thermal Conductivity | 23 W/m·K |
Density (g/cm³) | 7.85 |
Toughness | Good |
The above properties underline why H13 tool steel is a preferred choice for tool manufacturers aiming for durability and high performance.
The Role of Heat Treatment
What is Heat Treatment?
Heat treatment is a metallurgical process that alters the physical and sometimes chemical properties of a material. For H13 tool steel, heat treatment plays a vital role in enhancing hardness, improving toughness, and increasing wear resistance.
Importance of Heat Treatment in H13 Tool Steel
- Enhancement of Mechanical Properties: Heat treatment significantly increases the hardness of H13 tool steel, making it more suitable for demanding applications.
- Stress Relief: Proper heat treatment helps relieve internal stresses, which can lead to tool failure if not managed.
- Increased Lifespan: Tools made from heat-treated H13 exhibit longer service life, which translates into cost savings for manufacturers.
H13 Tool Steel Heat Treatment Process
Step-by-Step Heat Treatment Process
The heat treatment process for H13 tool steel involves several key stages:
Stage | Temperature Range (°C) | Duration |
---|---|---|
Pre-Heating | 500-650 | 1-2 hours |
Austenitizing | 1,000-1,050 | 30-60 minutes |
Quenching | Oil or air quench | Immediate |
Tempering | 500-650 | 1-2 hours (repeated) |
Pre-Heating
Pre-heating prepares the steel for a uniform heating process, which minimizes thermal shock during the subsequent austenitizing phase.
Austenitizing
During this stage, the steel is heated to a temperature where the microstructure transforms to austenite. This transformation is essential for achieving the desired hardness.
Quenching
Quenching involves rapidly cooling the steel to set the microstructure. This step is critical as it significantly influences the hardness of the tool.
Tempering
Tempering is performed after quenching to relieve stresses and adjust the hardness to the desired level. It is common to repeat this step multiple times for optimal results.
Benefits of H13 Tool Steel Heat Treatment
Enhanced Wear Resistance
H13 tool steel’s wear resistance is significantly improved through heat treatment, making it an ideal choice for applications such as die casting and forging.
Improved Toughness
Heat treatment also enhances the toughness of H13, ensuring that tools can withstand significant impacts and stresses without fracturing.
Cost-Effectiveness
While the initial investment in heat treatment may seem high, the long-term benefits, including reduced tool failure rates and extended lifespan, make it a cost-effective option for manufacturers.
Common Applications of H13 Tool Steel
Tool Manufacturing
H13 is widely used for manufacturing:
- Die Casting Dies: Required for producing complex shapes in molten metals.
- Hot Forging Tools: Essential for shaping materials under high temperatures.
- Plastic Molds: Used in the production of plastic parts where heat resistance is crucial.
Aerospace and Automotive Industries
H13 tool steel is also favored in the aerospace and automotive sectors for manufacturing components that endure high temperatures and harsh conditions.
Best Practices for H13 Tool Steel Heat Treatment
Selecting the Right Equipment
Choosing the appropriate heat treatment equipment, such as vacuum furnaces or oil quenching tanks, is critical to achieving consistent results.
Monitoring Temperature and Time
Maintaining precise control over temperature and duration during the heat treatment process is essential for achieving the desired properties in H13 tool steel.
Quality Control Measures
Implementing rigorous quality control measures ensures that the heat-treated tools meet the required specifications and standards.
Challenges in H13 Tool Steel Heat Treatment
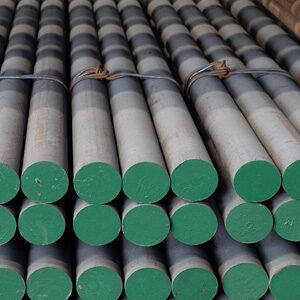
Distortion During Heat Treatment
One of the main challenges in heat treating H13 tool steel is distortion, which can affect the dimensional accuracy of the final product. Proper fixturing and quenching techniques can mitigate this issue.
Cracking Risks
Improper heat treatment can lead to cracking in the material. Understanding the right cooling rates and techniques is crucial to avoid this problem.
Cost of Heat Treatment
While heat treatment adds significant value, the cost can be a concern for some manufacturers. Investing in reliable processes and equipment can yield better returns in the long run.
Conclusion
H13 tool steel heat treatment is an essential step in the manufacturing of high-performance tools. Understanding the intricacies of the heat treatment process not only enhances the mechanical properties of H13 but also ensures the longevity and reliability of the tools produced. By adhering to best practices and leveraging advanced heat treatment techniques, manufacturers can significantly improve their product quality and operational efficiency.
FAQ
Q:What is the best heat treatment for H13 tool steel?
A:The best heat treatment for H13 typically involves pre-heating, austenitizing, quenching, and tempering at specified temperatures to achieve optimal hardness and toughness.
Q:How does heat treatment affect the cost of H13 tool steel?
A:While heat treatment can increase upfront costs, the long-term benefits in terms of tool lifespan and performance often outweigh these initial investments.
Q:Can H13 tool steel be re-heat treated?
A:Yes, H13 tool steel can be re-heat treated to restore or enhance its properties if the tools have suffered wear or damage during use.
Q:What are the common defects in H13 tool steel heat treatment?
A:Common defects include distortion, cracking, and incomplete hardening, often caused by improper temperature control or quenching techniques.
Q:Is H13 tool steel suitable for cold work applications?
A:While H13 is primarily designed for hot work applications, it can be used in some cold work applications where moderate wear resistance is required.
Q:How does the heat treatment process vary for different applications?
A:The specific parameters of heat treatment may vary depending on the intended application, with different hardness and toughness requirements influencing the process.
Q:What industries benefit the most from H13 tool steel?
A:Industries such as automotive, aerospace, and manufacturing benefit significantly from H13 tool steel due to its high performance in demanding environments.