Our Services
Increase productivity, reduce risk, and choose a trusted partner that offers steel products with a full range of processing services.
Qilu Tool Steel offers a comprehensive range of steel processing services and is committed to tailoring solutions to the unique needs of our customers. Our processing capabilities include steel cutting, face milling, side milling, drilling, rough turning, centerless stripping, forging, heat treating and metal testing. Whether you need a customized steel part for a specific manufacturing requirement or are looking for high-precision professional machining services, our team has the expertise and experience to ensure a high-quality solution for you.
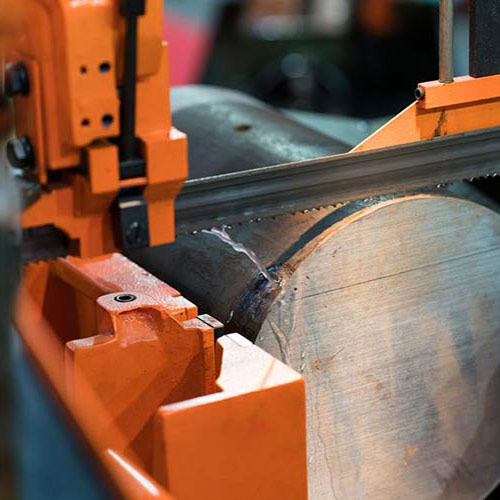
Steel Processing
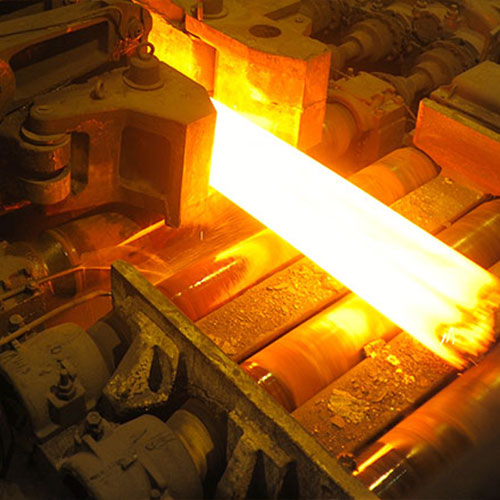
Heated Forging
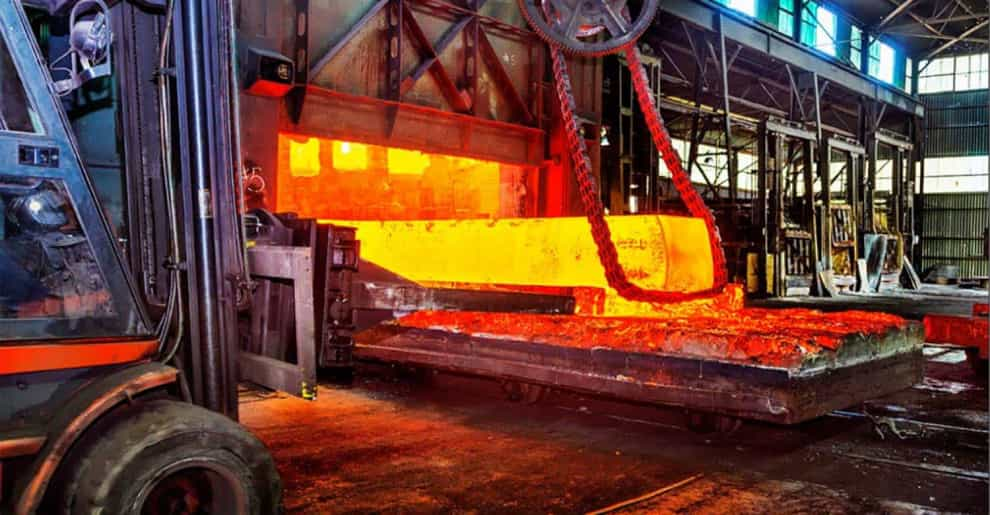
Heat Treatment
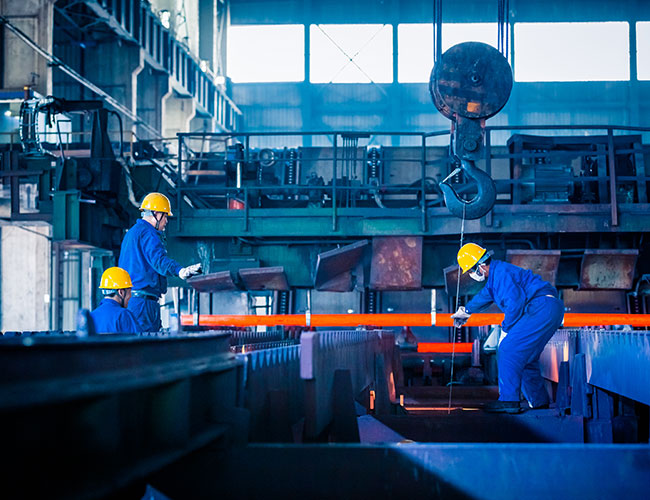
Third Party Testing
Steel Processing
Qilu Tool Steel focuses on providing diversified steel processing solutions designed to meet the individual needs of all types of customers. Our services include precision cutting, fine drilling, accurate punching and complex bending of steel.
Whether you need to create a steel part with special specifications or are looking for highly customized processing services, our team is able to complete each task perfectly with our in-depth industry experience and expertise. We work closely with our customers to gain an in-depth understanding of their unique requirements, providing customized solutions to ensure the best possible results for every project.
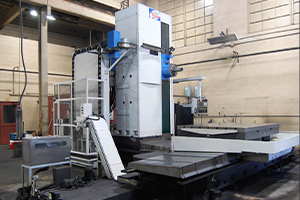
Face Milling and Side Milling
Our company can supply follows materials in face milling and side mill processes:
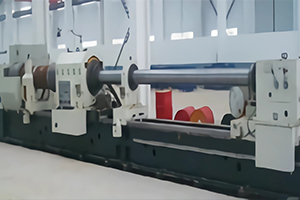
Boring Drilling
Our company can provide Boring Drilling services for the following materials:
Size Range
Width: 3000mm Max
Height: 1000mm Max
Dimension Tolerance
-0/+3mm Max
Size Range
Inner Diameter:25mm-350mm
Length: 10000mm Max
Wall Thickness :≥100mm
Dimension Tolerance
-3/+0mm Max
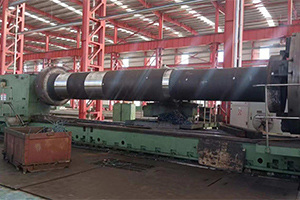
Rough Turning
Our company can provide Rough Turning services for the following materials:
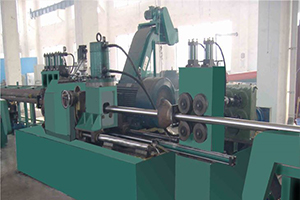
Centerless Peeling
Our company can provide Centerless Peeling services for the following materials:
Size Range
Diamater: 80mm-1200mm
Length: 10000mm
Dimension Tolerance
-0/+3mm Max
Size Range
Diamater: 25mm-300mm
Length: 3000mm Min
Dimension Tolerance
-0/+1.5mm
Heated Forging
Heat treatment optimizes the properties of materials through heating and cooling processes to improve hardness, wear resistance, strength, etc. to meet different industrial needs.
The upsetting process, in which the diameter of a workpiece is increased by compressing its length, is by far the most widely used form of forging and is particularly suitable for mass production. This process enables the manufacture of common components such as engine valves, couplings, bolts, screws and other fasteners.
The process is characterized by a die designed with multiple cavities, and the workpiece can be moved from one cavity to another. Whenever the die is closed, the upsetting tool or punch moves in the longitudinal direction, pushing the bar into the die cavity to form the desired shape. Since all cavities can be utilized for each cycle, each cycle produces a complete finished part, making upsetting particularly suited to high volume production.
The upsetting process is usually carried out on a specialized high-speed machine called a crank press, but it can also be operated on a vertical crank press or a hydraulic press. These machines are usually designed to work horizontally so that the workpiece can be moved quickly from station to station to ensure productivity.
The initial form of the workpiece is usually wire or bar, but some high specification machines can handle bars up to 25 cm (9.8 in) in diameter and with a capacity of over 1000 tons. In standard headers, the process is often carried out using a split die with multiple cavities, a design that allows the process to perform complex forming tasks more accurately.
Rules That Must Be Followed When Designing Parts That Require Upsetting
In the upsetting process, unsupported metal that exceeds a certain percentage of its length may result in damage or undesirable effects during processing. In general, the length of unsupported metal that can be successfully flattened in a single blow without damage should be limited to three times the diameter of the bar.
Successful upsetting is also possible where the upsetting diameter does not exceed 1.5 times the diameter of the billet and the length of the billet is more than three times the diameter. In cases where a billet length greater than three times the diameter is required and the cavity diameter is not greater than 1.5 times the diameter of the billet, the length of the unsupported metal beyond the surface of the die shall not exceed the diameter of the bar in order to avoid problems such as uneven machining or material waste.
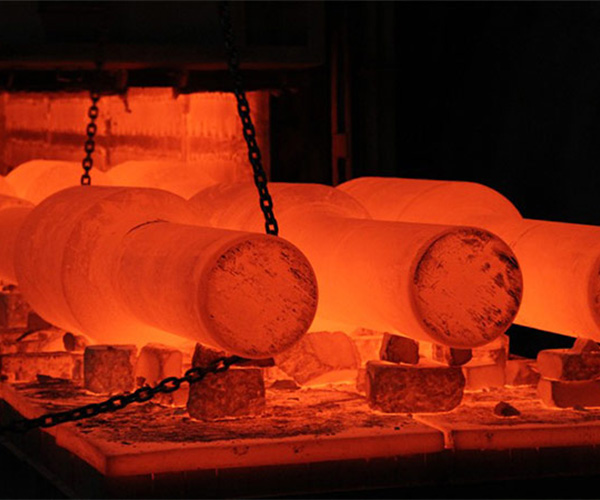
Heat Treatment
We Offer the Following Heat Treatment Services:
Normalizing, annealing, quenching, tempering, carburizing, nitriding, high-frequency surface quenching and other processing services.
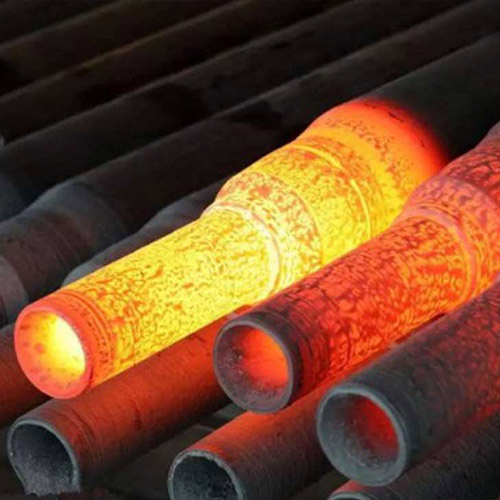
Normalizing
Normalizing is a common heat treatment process used to increase the hardness and refine the grain structure of a material. By heating the metal to a specific temperature and then cooling it naturally in air to room temperature, the normalizing process can effectively refine the grain size and thus improve the overall properties of the material.
Normalizing not only improves the microstructure of the steel, but also enhances the homogeneity of its properties, allowing it to exhibit better mechanical properties and stress resistance in service. The process is commonly used to improve the machinability, toughness and hardness of steel, making it more reliable for various engineering applications.
Annealing
Annealing is a heat treatment process designed to improve the properties of metals and alloys, especially ductility and toughness. The process consists of heating the material to a specific temperature, maintaining that temperature for a period of time to ensure uniform heating, and then achieving the desired microstructure and mechanical properties by slow cooling to room temperature.
During the annealing process, the internal structure of the material changes, mainly through the rearrangement of the crystal lattice to reduce the internal stresses in the material. By annealing, the ductility and toughness of the material are significantly improved, making it easier to perform subsequent machining and deformation processes. This process is often used to improve the machinability, crack resistance and formability of metals.
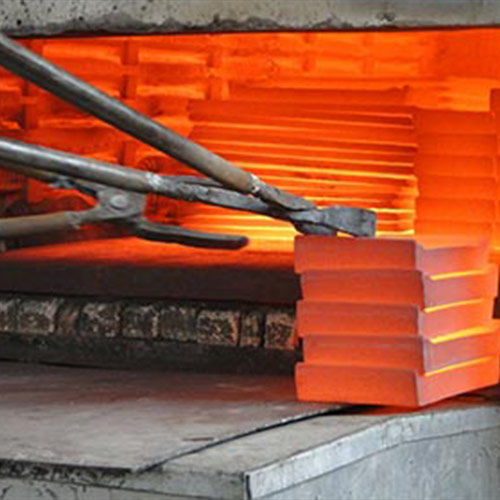
Annealing is a heat treatment process for metallic materials designed to improve their properties, such as increasing toughness, machinability, and mechanical properties. Common forms of annealing include:
Complete annealing: the material is heated to a sufficiently high temperature and held at that temperature for a period of time, after which it is slowly cooled. This method of annealing significantly increases the toughness of the material and improves its machinability, making it easier to subsequently process.
Normalizing: Similar to full annealing, but after normalizing, the material is cooled naturally in air to room temperature, often accompanied by subsequent hardening. This process is primarily used for heavy steel parts and is effective in increasing the strength and hardness of the material.
Spheroidal Annealing: The material is heated to near the critical temperature and cooled slowly, which helps to evenly distribute the carbon elements in the material, creating a spherical microstructure. Spheroidal annealing improves the machinability of the material, especially if further processing is required.
Age Annealing: The material is heated to a specific temperature and held at that temperature for a certain period of time to induce the precipitation of alloying elements in solid solution. This process can significantly change the physical and mechanical properties of the material, increasing its hardness and strength.
Stress Relief Annealing: Heating the material to an appropriate temperature and cooling it slowly to remove stresses and defects within the metal. This type of annealing improves the machinability of the material, as well as its corrosion resistance, and is suitable for high-precision machining of metallic materials.
Depending on the type of metal and the application requirements, choosing the right form of annealing can achieve the best machining results and performance.
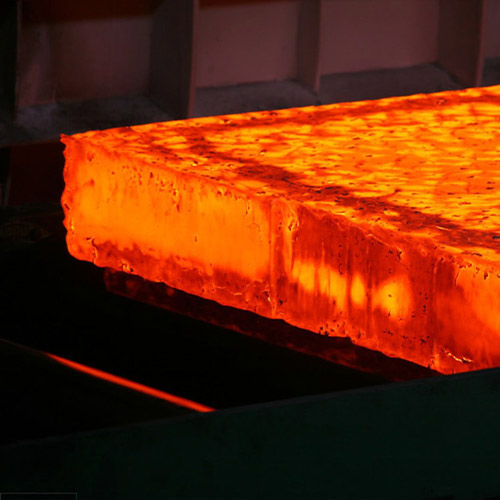
Quenching And Tempering
In the QT heat treatment process, the quenching stage is carried out first. In this phase, the material is heated to a specific high temperature and then quickly cooled by immersion in water, oil or other cooling medium. This rapid cooling process makes the material very hard, but also increases its brittleness.
This is followed by a tempering process in which the material is heated to a lower temperature and held at this temperature for a period of time. The purpose of tempering is to reduce the brittleness caused by quenching, while retaining some of the hardness and strength, so that the material has better toughness while maintaining high hardness.
The temperatures and durations of the two stages of the QT process – quenching and tempering – are precisely controlled to ensure that the material achieves the desired mechanical properties. The yield strength, tensile strength, toughness as well as impact and fatigue resistance of the material are significantly improved by this heat treatment, making the material more adaptable to high-intensity applications.
Third Party Testing
Metal Material Inspection
As a professional third-party testing organization with an advanced metal material testing laboratory, Qilu Tool Steel is committed to providing comprehensive metal property testing services to our customers. Our testing services cover a wide range of performance tests for metal materials, ensuring that every batch of materials meets high quality standards. Through accurate experimental analysis and rigorous testing processes, we help our clients ensure the reliability and suitability of their materials to meet the needs of different applications.
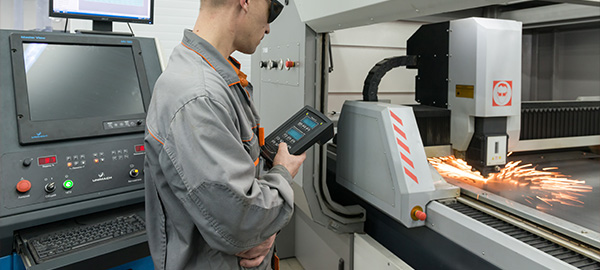
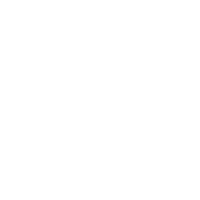
Metal Material Inspection Time
Testing of metallic materials typically takes 1 to 7 business days to complete, depending on the complexity of the project and the testing requirements. However, if time is of the essence, we also offer expedited services to ensure quicker completion of testing. Test engineers will evaluate and determine the exact test cycle time based on the specifics and difficulty of the project to ensure high quality and accurate results.
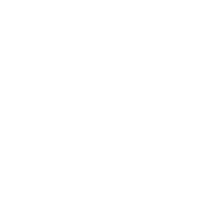
Cost of Metal Material Testing
The cost of metal material testing can vary depending on the type and complexity of the project. Our engineers will assess the testing program required for your specific needs and provide you with a detailed quote. The cost of each project takes into account material properties, test content and workload to ensure that you are provided with a fair and reasonable price.
Inspection Items
Chemical Composition Analysis
This work involves the quantitative analysis of various elements in steel such as carbon (C), manganese (Mn), silicon (Si), molybdenum (Mo), chromium (Cr), nickel (Ni), cobalt (Co), etc., which have a significant influence on the properties of steel.
For accurate chemical analysis, commonly used detection methods include Atomic Absorption Spectrometry (AAS), X-ray Fluorescence Spectrometry (XRF) and Inductively Coupled Plasma Mass Spectrometry (ICP-MS). These techniques are capable of accurately measuring the content of each element in steel.
Through this process, we are able to ensure that the chemical composition of the steel complies with industry standards and customer requirements, thus guaranteeing its performance and reliability in real-world applications.
Mechanical Properties Testing
Are you overly dependent on a single country or supplier?
Tests include:
Tensile strength: assesses the strength of a material when subjected to a maximum tensile load.
Yield strength: measures the stress at which a material begins to undergo permanent deformation.
Elongation: Reflects the material’s ductility during stretching.
Area Reduction: Measures the extent to which a material’s cross-section changes before it breaks.
Hardness: Assesses the resistance of a material’s surface to localized indentation.
Impact Toughness: tests the ability of a material to resist impact, especially at low temperatures.
Methods used include:
Tensile testing: Used to measure each mechanical property of a material during stretching.
Impact testing: Used to evaluate the toughness of a material under instantaneous loading.
Hardness testing: Measures the ability of a material to resist indentation. Commonly used test methods include Brinell hardness, Rockwell hardness, etc. Purpose: The purpose of these tests is to provide a complete picture of the material’s resistance to indentation.
Purpose: The purpose of these tests is to comprehensively evaluate the performance of a material under different stresses and environmental conditions to ensure its suitability for specific engineering applications.
Ultrasonic Testing
Do you need on-the-ground support in the global supply market?
Ultrasonic Inspection:
Utilizing the propagation properties of ultrasonic waves in materials, ultrasonic inspection is an effective non-destructive testing method for identifying defects within materials, such as cracks, inclusions, bubbles, and more.
Testing Process:
Transverse Wave Scanning: By propagating transverse waves through the material, defects are detected on the surface and near-surface areas of the material.
Longitudinal Wave Scanning: Longitudinal waves penetrate deep into the material and are used to detect deeper defects or inhomogeneities.
Purpose: The main purpose of ultrasonic testing is to identify and locate micro-defects within the material, thus ensuring the integrity and reliability of the material and preventing potential quality problems from affecting its subsequent applications.
Structural Analysis
These include static and dynamic stress analysis, fatigue analysis and fracture analysis:
These analyses help to evaluate the performance and durability of materials and structures under actual loads. Static stress analysis focuses on the deformation and stress distribution of materials under static loading, while dynamic stress analysis focuses on the response of the structure under transient or cyclic loading.
Methods used include:
Finite Element Analysis (FEA): This is a computer simulation technique used to analyze the stresses, deformations, and response of a structure under varying loads.FEA can be used for static, dynamic, and fatigue analyses to help predict how a structure will perform in actual use.
Experimental Stress Analysis: Physical testing to verify the stress distribution of a structure under loading, usually measured using strain gauges or other transducers.
Fatigue Life Prediction: Evaluating the fatigue performance and expected life of a material or structure under cyclic loading through simulation and experimentation.
Purpose: The purpose of these analytical methods is to evaluate the response and durability of structures under varying stress conditions, helping engineers to predict potential structural failures, optimize designs and improve product reliability and service life.
Heat Treatment
Checking the organization and properties of steel after a heat treatment process such as quenching, tempering and normalizing is an important step to ensure that it meets the design requirements.
The main tests include:
Metallographic analysis: Observe the organization of the steel through microscope to analyze the phase change, grain structure and its uniformity of the material during the heat treatment process.
Hardness test: Measure the hardness of the steel to assess its wear resistance and compression resistance, usually using Brinell hardness, Rockwell hardness and other methods.
Grain size assessment: Analyzing the grain size of the material through microscopy to ensure that the steel has the required mechanical properties after heat treatment.
Purpose: The purpose of these tests is to verify the success of the heat treatment process and to ensure that the steel can achieve the desired performance objectives after heat treatment, such as increased hardness, enhanced strength, improved toughness, etc., in order to meet the requirements of actual use.
Magnetic Particle Testing
Magnetic Particle Inspection:
Magnetic Particle Inspection is a non-destructive testing method that specializes in detecting surface and near-surface defects, such as cracks and holes, in magnetic materials.
The testing process includes:
Magnetizing the workpiece: first, the workpiece is magnetized by applying a magnetic field to make it magnetic.
Applying magnetic powder: Next, fine magnetic powder (usually iron powder) is applied, which accumulates on the surface of the workpiece and near-surface defects.
Observation of accumulated powder: The accumulation of powder is inspected by the naked eye or specialized equipment. Surface cracks or defective areas will be clearly visible as they are aggregated by the magnetic powder.
Purpose:
The main purpose of this method is to find and mark defects on and under the surface of magnetic materials, such as cracks, joint defects or corrosion spots, to ensure the quality and reliability of the material and to avoid failures caused by hidden defects.
Dimensional Testing
Dimensional Measurement and Inspection:
Accurately measuring the size, shape and location of a part is a critical step in ensuring that the product meets design requirements and quality standards.
The testing process includes:
Linear Dimension Measurement: Use calipers, micrometers and other tools to accurately measure basic dimensions such as length, width and height of the part.
Geometric tolerance checking: Check whether the shape of the part meets the design requirements, including straightness, parallelism, perpendicularity, roundness, etc.
Thread Measurement: Measure the outer diameter, inner diameter, and pitch of threads to ensure that their accuracy meets standards.
Gear Measurement: Including gear tooth shape, tooth pitch, number of teeth, tooth width and other parameters to ensure that the gears can be transmitted smoothly.
Testing Tools:
Tools used include calipers, micrometers, depth gauges, coordinate measuring machines and other high-precision instruments to ensure the accuracy of the measurements.
Purpose:
The purpose of this test is to confirm that the dimensions and shapes of the parts are in accordance with the design drawings and engineering requirements, and to ensure that the parts produced fit accurately, function properly, and meet the customer’s quality standards.
Visual Testing
Visual Inspection:
Visual inspection is a basic non-destructive testing method used to check the surface of a material for visible defects or problems.
The testing process includes:
Use of Auxiliary Tools: Surface details can be examined more clearly with the aid of a magnifying glass, camera, or other magnifying tools. Direct observation by the naked eye is also possible, as needed.
Inspecting for surface defects: The focus of the inspection includes surface scratches, pits, oxidized skin, weld defects, etc. to ensure that there are no visible defects on the surface.
Record and Evaluate: record any defects found and evaluate their impact on material performance.
Purpose:
The main purpose of visual inspection is to identify obvious surface defects or processing problems so that potential quality problems can be detected in time and corrective action taken accordingly. This helps to improve the appearance quality of the product as well as the accuracy and safety of subsequent processing.
Customized Testing
Customized Testing:
Unique testing based on customer needs or industry standards to ensure that a material or product meets the requirements of a specific application.
Test types include:
Specialized Corrosion Testing: Evaluates the corrosion resistance of materials by simulating the corrosive effects of different environmental conditions (e.g., salt spray, heat and humidity, etc.).
Environmental Adaptability Testing: Tests the performance of materials under extreme environmental conditions (e.g., high temperature, low temperature, humidity changes, etc.) to ensure their long-term stability in specific environments.
Application-specific performance testing: According to the requirements of specific industries, performance tests such as abrasion resistance, high temperature resistance, fatigue resistance, etc., are conducted to ensure that the products can fulfill their expected roles in actual use.
Purpose:
The main purpose of customized testing is to ensure that the material or product not only meets general standards, but also meets customer-specific needs or industry specifications to ensure its reliability and long-term performance in specific applications.
Metal Material Inspection Report Process
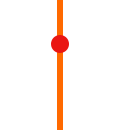
Communicate with engineers to determine the requirements of metal material testing
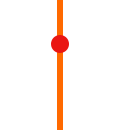
Fill in the test order form and confirm payment
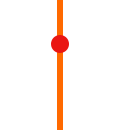
Send samples, conduct laboratory tests and release test results
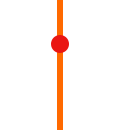
Generate metal material test report according to the test content
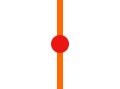