Welcome to My Blog!
Before we dive into the content, I’d love for you to join me on my social media platforms where I share more insights, engage with the community, and post updates. Here’s how you can connect with me:
Facebook:https://www.facebook.com/profile.php?id=100087990137347
LinkedIn:https://www.linkedin.com/company/89825762/admin/dashboard/
YouTube:www.youtube.com/@carbonsteelsupply-kj9lw
TikTok:www.tiktok.com/@carbonsteelsupply
Now, let’s get started on our journey together. I hope you find the content here insightful, engaging, and valuable.
Introduction
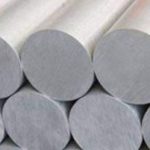
S7 tool steel is a popular air-hardening steel known for its toughness and shock resistance, making it an ideal choice for tools and dies that need to withstand high impact. However, to unlock its full potential, a precise heat treatment process is essential. In this comprehensive guide, we will explore every aspect of the S7 tool steel heat treat process, including the stages, temperatures, and common mistakes to avoid. With detailed explanations and tables, you’ll have all the information you need to optimize the performance of S7 tool steel.
What Is S7 Tool Steel and Why Is Heat Treatment Important?
S7 tool steel is a versatile, air-hardening material often used in applications that require high impact resistance, such as punches, chisels, and forming dies. It offers a unique balance of toughness and hardness, but these properties can only be achieved through a controlled heat treatment process. The tool steel heat treat process involves heating, quenching, and tempering, all of which are necessary to achieve the desired hardness and toughness.
Heat treatment for S7 tool steel ensures:
- Enhanced toughness: Allows the steel to absorb impact without cracking.
- Increased hardness: Improves wear resistance and longevity.
- Dimensional stability: Proper heat treatment maintains the tool’s dimensions during use.
The Heat Treatment Process for S7 Tool Steel
The S7 tool steel heat treat process involves several key stages: preheating, austenitizing, quenching, and tempering. Each stage must be conducted with precision to optimize the steel’s performance. Here’s a step-by-step breakdown:
Preheating
Preheating S7 tool steel is crucial to prevent thermal shock and reduce the risk of cracking. The recommended preheat temperature for S7 tool steel is between 1200°F and 1300°F (650°C – 705°C). This stage should be held for 30 minutes to ensure even temperature distribution.
Austenitizing
The austenitizing stage transforms the steel’s microstructure into austenite, a phase necessary for hardening. The typical austenitizing temperature for S7 tool steel is 1725°F (940°C). Holding the tool steel at this temperature for about 15 to 30 minutes allows the material to reach a uniform temperature throughout.
Quenching
S7 tool steel is an air-hardening material, meaning it should be cooled in still air. After reaching the austenitizing temperature, the steel should be removed from the heat source and allowed to cool naturally in the air. This process hardens the steel without introducing the stress typically associated with oil or water quenching.
Tempering
Tempering is essential to adjust the hardness and enhance the toughness of S7 tool steel after quenching. The tempering temperature varies depending on the required hardness. Here’s a table outlining the recommended tempering temperatures and corresponding hardness levels:
Tempering Temperature (°F) | Duration | Hardness (HRC) Range |
---|---|---|
400°F | 1-2 hours | 56-58 |
500°F | 1-2 hours | 54-56 |
600°F | 1-2 hours | 52-54 |
700°F | 1-2 hours | 50-52 |
800°F | 1-2 hours | 48-50 |
Interpreting the Table:
- Lower Temperatures (400°F – 500°F): These temperatures are used when maximum hardness is needed. This setting is ideal for cutting tools that require sharp edges and high wear resistance.
- Higher Temperatures (600°F – 800°F): Higher tempering temperatures reduce hardness but increase toughness, making the steel suitable for applications like impact tools and hammers.
Factors Affecting the S7 Tool Steel Heat Treat Process
Several factors can impact the effectiveness of the S7 tool steel heat treat process:
- Temperature Control: Maintaining precise temperatures throughout each stage is critical. Variations can lead to inconsistent hardness and impact resistance.
- Time Management: The duration at each stage, especially during austenitizing and tempering, affects the steel’s properties. Under- or over-tempering can result in reduced performance.
- Cooling Rate: While S7 tool steel is air-hardened, ensuring a consistent cooling environment is important to avoid uneven hardness.
Common Mistakes to Avoid in the Heat Treatment Process
To ensure optimal results, it’s important to avoid these common mistakes during the S7 tool steel heat treat process:
- Skipping the Preheat Stage: Directly heating S7 tool steel to the austenitizing temperature can cause cracks and other structural issues due to thermal shock.
- Overheating During Austenitizing: Exceeding the recommended austenitizing temperature (1725°F) can lead to grain growth, reducing the steel’s toughness.
- Improper Quenching Environment: While air quenching is preferred, cooling the steel too rapidly (e.g., using a fan) can lead to distortions and stress.
- Inconsistent Tempering Times: Ensure consistent and precise tempering durations to maintain the desired hardness and toughness.
Optimizing the Heat Treatment for Specific Applications
The S7 tool steel heat treat process can be optimized based on the intended application. Adjustments in the tempering temperature allow you to fine-tune the hardness and toughness levels to match specific requirements:
- For High Impact Tools: Tools like chisels and punches benefit from tempering at higher temperatures (700°F – 800°F) to increase toughness.
- For Cutting Tools: When making cutting tools such as shear blades, lower tempering temperatures (400°F – 500°F) are recommended to maximize hardness and edge retention.
- For Mold Components: Mold and die components, which require a balance of hardness and durability, are best tempered around 600°F.
Testing and Verifying the Hardness of S7 Tool Steel
After the heat treatment process, it is crucial to test and verify the hardness of S7 tool steel. Here are some of the most effective methods:
- Rockwell Hardness Test: The most common method, which measures hardness on the Rockwell C (HRC) scale. This method is used to ensure that the steel meets the required hardness levels based on its intended application.
- Microhardness Testing: For smaller components, microhardness testing provides precise readings, ensuring that the steel has uniform hardness throughout.
- Non-Destructive Testing (NDT): NDT methods like ultrasonic testing help identify internal flaws that may have developed during the heat treatment process without damaging the steel.
FAQ: Frequently Asked Questions About S7 Tool Steel Heat Treat
1. What is the ideal austenitizing temperature for S7 tool steel?
The ideal austenitizing temperature for S7 tool steel is 1725°F (940°C), and it should be held for 15-30 minutes.
2. Can S7 tool steel be quenched in oil or water?
No, S7 tool steel is an air-hardening steel, and oil or water quenching can cause severe stress and cracking.
3. How does tempering affect the properties of S7 tool steel?
Tempering adjusts the hardness and toughness of S7 tool steel, allowing you to fine-tune its properties based on the application. Lower temperatures increase hardness, while higher temperatures increase toughness.
4. Is it possible to reheat treat S7 tool steel if the hardness is not achieved?
Yes, if the desired hardness is not reached, S7 tool steel can be reheat treated. Ensure that the proper procedures are followed to avoid compromising the steel’s integrity.
5. How is hardness measured after heat treatment?
Hardness is typically measured using the Rockwell Hardness Test (HRC) to ensure that the steel meets the required specifications.
Conclusion
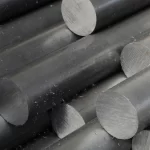
The S7 tool steel heat treat process is vital for achieving the desired balance of toughness and hardness that makes this steel so versatile and valuable. By understanding each stage—from preheating and austenitizing to quenching and tempering—you can optimize the steel’s properties to suit specific applications, whether it’s for cutting tools, impact tools, or mold components.
Proper control of temperatures, durations, and cooling environments is key to successful heat treatment. By avoiding common mistakes and testing the steel’s hardness post-treatment, you ensure that S7 tool steel performs optimally in demanding applications.