M4 High Speed Steel
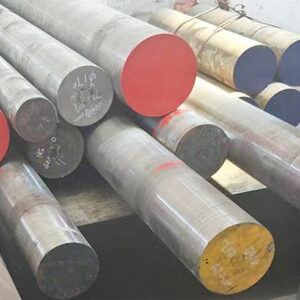
M4 High speed steel
M4 high-speed steel is a high-performance alloy tool steel widely used in the manufacture of cutting tools and molds. Its main characteristics are excellent wear resistance, hot hardness and oxidation resistance. The chemical composition of M4 steel includes a high content of molybdenum (Mo), which makes it extremely resistant to wear and high-temperature strength, and can maintain high hardness at high temperatures. It also contains a certain proportion of tungsten (W) and cobalt (Co), which further enhances its resistance to thermal fatigue and corrosion.
Chemical composition 7365_573951-28> |
Value 7365_e9d92b-91> |
C 7365_dd2ede-c3> |
1.25% – 1.40% 7365_5d0c51-6a> |
Si 7365_00a6bc-72> |
0.20% – 0.45% 7365_e9fe36-ff> |
Mn 7365_494423-15> |
0.15% – 0.40% 7365_d56a55-c7> |
S 7365_3370ee-ab> |
≤0.030% 7365_e9af33-5e> |
P 7365_3d0eb6-32> |
≤0.030% 7365_8e00bd-ae> |
Cr 7365_83ea1d-b8> |
3.75% – 4.75% 7365_1ab482-01> |
Mo 7365_c74c5b-97> |
4.25% – 5.50% 7365_fdac26-fa> |
V 7365_52923f-98> |
3.75% – 4.50% 7365_6e6a78-92> |
W 7365_2302d1-2c> |
5.25% – 6.50% 7365_739e01-8e> |
Another dimension according to your requirements Surface condition:
— Black, annealed Rough Machined, Turned, or as per given requirements.
Mechanical properties:
-Hardness
Exercise hardness: After heat treatment, the hardness of M4 high-speed steel can reach HRC 64-66.
High temperature hardness: In high temperature environments, M4 high -speed steel can still maintain high hardness, such as HRC 50.5 at 600°C.
-Strength
Tensile strength: CPM M4 high -speed steel’s tensile strength is as high as 2500 MPa.
Symbol strength: Although the specific value is not clear, its yield strength is also at a high level.
-Toughness
M4 high -speed steel has high toughness, which is due to the role of the element, which can refine the grains, so that it has a certain impact ability while high hardness.
-Abrasion resistance
M4 high -speed steel’s high -carbon and high -pyreces content makes it have excellent abrasion resistance and is suitable for materials that are difficult to process.
Application
1.Cutting tools: suitable for manufacturing milling cutters, drills, turning tools, inserts, etc., for high-speed cutting, high-temperature cutting and heavy-load cutting.
2.Mold manufacturing: suitable for manufacturing cold forging dies, precision stamping dies, powder pressing dies, deep drawing dies, punching dies, etc., especially suitable for dies that withstand vibration and impact loads.
3.Mechanical parts: suitable for manufacturing mechanical parts that require high wear resistance or toughness.
Customer Testimonials
High Performance, Durable
“M4 high-speed steel has significantly improved our tool life. Its excellent stability and wear resistance mean fewer replacements and reduced costs. It’s become our go-to for high-performance tools.”
Precision Cutting, Improved Efficiency
“We rely on M4 steel for its superior hardness and heat resistance, which boosts cutting efficiency and ensures precise machining. It perfectly meets our production needs, enabling us to achieve higher productivity.”
Reliable Quality, Trustworthy
“The quality of M4 high-speed steel is exceptional. Its corrosion resistance makes it ideal for high-stress machining applications, greatly enhancing both the efficiency of our factory and the quality of our products.”