M2/1.3343 Tool Steel
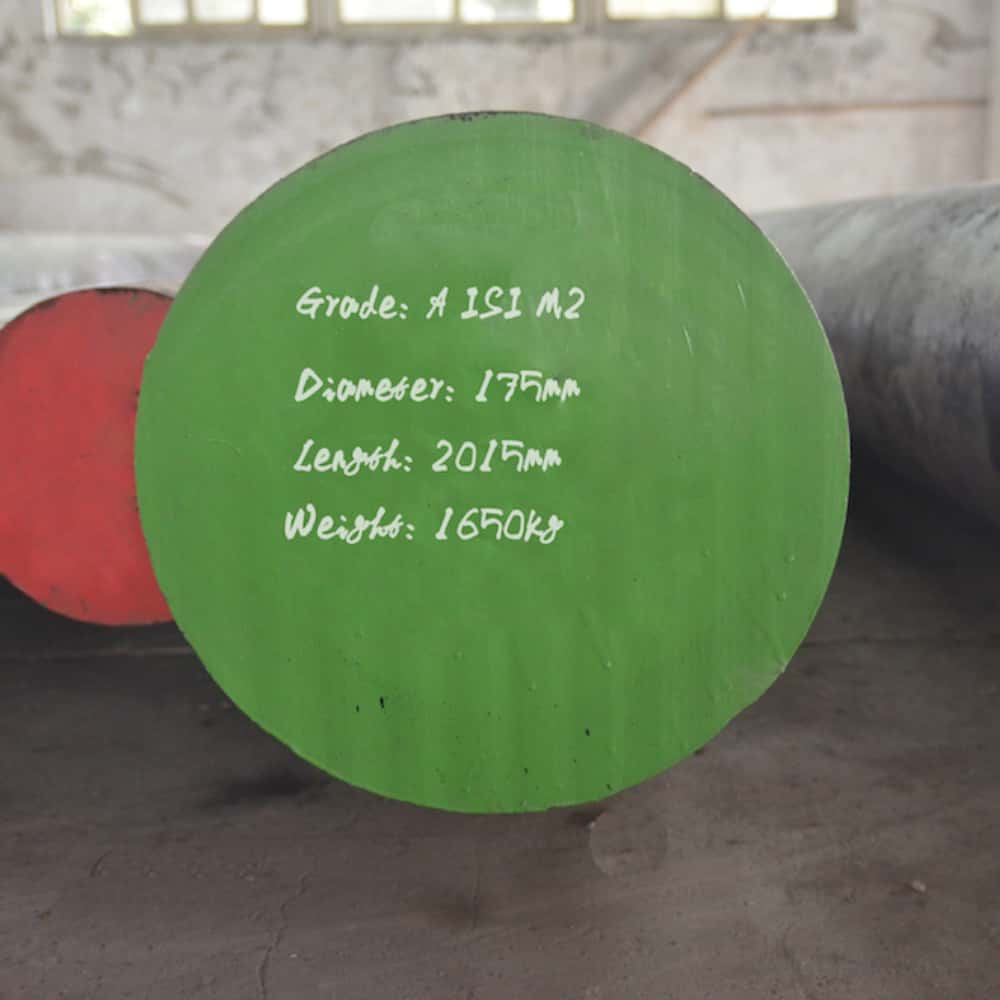
M2/1.3343 Tool Steel
AISI M2 Tool Steel is molybdenum based high-speed steel in tungsten–molybdenum series. The M2 chemical composition gives a good combination of well-balanced toughness, wear resistance and red hardness properties. Widely used for cutting tools such as twist drills, taps, milling cutters, saws, knives etc. Also commonly used in cold work punches and dies and cutting applications involving high speed and light cuts.M2 High Speed Steel is by far the most popular high speed steel replacing high speed steel grade T1 in most applications because of its superior properties and relative economy.
Chemical composition 7297_9078fb-c8> |
Value 7297_77c693-b4> |
C 7297_e955b2-39> |
0.78%~0.88% 7297_bb7885-77> |
Mn 7297_795619-25> |
0.15%~0.40% 7297_272a13-b7> |
Si 7297_4042d0-5b> |
0.20%~0.45% 7297_eac919-3f> |
S 7297_a66785-f6> |
≤0.030% 7297_381111-75> |
P 7297_8647f5-e1> |
≤0.030% 7297_85b326-49> |
Cr 7297_0eda30-4e> |
3.75%~4.50% 7297_c9ec91-45> |
Mo 7297_f070f7-10> |
4.50%~5.50% 7297_0a9d27-aa> |
V 7297_8d36e8-43> |
1.75%~2.20% 7297_212145-a0> |
W 7297_edf031-c0> |
5.50%~6.75% 7297_c627a0-75> |
Ni 7297_cca337-b6> |
≤0.30% 7297_b287af-1c> |
M2 Steel Round Bar:
-diameter 2 mm–200 mm
Steel Plate:
-thickness 2-200 mm x width 200-610 mm
Mechanical property:
-Hardness
Factory hardness: ≤255HB.
Hardness after quenching: The hardness after quenching can reach 62-66HRC.
High temperature hardness: At 600℃, the hardness can still be maintained at 48.5HRC.
-Strength
Tensile strength: about 1800 MPa.
Flexural strength: 3.5-4.0 GPa.
-Toughness
Impact toughness: 0.18-0.32 MJ/m².
Overall toughness: M2 high-speed steel has higher toughness, better than some high-hardness high-speed steels (such as M4), and is suitable for bearing impact loads.
-Wear performance
M2 high-speed steel has high wear resistance and is suitable for manufacturing cutting tools and molds.
-Thermal stability
M2 high-speed steel has good red hardness, that is, it can still maintain high hardness at high temperatures and is suitable for high-temperature cutting environments
Application
1.Cutting tool manufacturing: commonly used to manufacture drills, milling cutters, taps, gear cutters, saw blades and other cutting tools, which can efficiently cut a variety of metal materials.
2.Cold working die manufacturing: can be used to manufacture cold stamping dies, cold extrusion dies, etc. Its high hardness and wear resistance can ensure that the mold maintains accuracy and shape during long-term use.
3.Other fields: can also be used to manufacture measuring tools, cutting tools, etc. Its excellent performance can meet the requirements of high precision and high wear resistance.
Customer Testimonials
Reliable Performance in High-Temperature Applications
“We’ve been using M2 tool steel for several months now, and its performance has exceeded our expectations. The material maintains its hardness even under high temperatures, making it ideal for our precision tools. We’re very satisfied with its reliability and overall quality.”
Excellent Durability and Consistency
“M2 high-speed steel has become our go-to choice for manufacturing cutting tools. The consistency and durability of the steel ensure minimal wear and long service life. We highly recommend it for any high-performance tooling applications.”
Improved Production Efficiency
“The M2 tool steel we purchased has proven to be an excellent investment. It offers outstanding wear resistance and is easy to machine into the required shapes. Our production efficiency has improved significantly since we switched to this material.”