D6/1.2436 Tool Steel
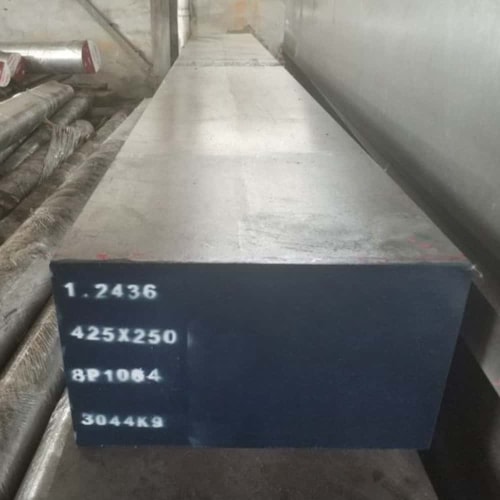
D6/1.2436 Tool Steel
D6 (1.2436) is a high-performance tool steel widely used in the manufacturing of molds, dies, and precision tools. It is a cold-work tool steel known for its excellent wear resistance, high hardness, and outstanding toughness. This steel grade is typically used in applications requiring durability and resistance to high abrasion under high pressure.
D6 (1.2436) tool steel is commonly used in industries where durability, toughness, and wear resistance are key factors. It is available in various forms such as bars, plates, and customized shapes to suit specific requirements.
Product Parameter Table
Chemical composition :
Element 7401_6d6b17-93> |
D6 7401_18357f-84> |
1.2436 7401_75499e-07> |
C 7401_8cac77-43> |
2.0-2.2 7401_b28b5f-02> |
2.0-2.3 7401_d0bc8d-ee> |
Si 7401_9b2f79-22> |
0.2-0.4 7401_b13d28-73> |
0.3-0.6 7401_dd6942-6e> |
Mn 7401_952a7d-03> |
0.03max 7401_f77959-e1> |
0.03max 7401_39abec-34> |
S 7401_cf85eb-d0> |
0.03max 7401_fbdc4c-d8> |
0.03max 7401_642ca2-b2> |
P 7401_cd8552-2e> |
0.2-0.4 7401_0d6a48-5d> |
0.1-0.4 7401_b88912-26> |
Cr 7401_21fd91-47> |
11.5-12.5 7401_64d15d-43> |
11.0-13.0 7401_4f4f0c-df> |
W 7401_39cded-28> |
0.6-0.9 7401_dce9fd-6c> |
0.6-0.8 7401_51b527-3a> |
Mechanical properties :
Tensile Strength Mpa 7401_7638c7-05> |
Yield Strength Mpa 7401_26626f-ef> |
Elongation % 7401_5f46ed-06> |
Reduction Area Z(%) 7401_1e6f8d-1d> |
Charpy Impact 7401_38c67d-5c> |
≥1320 MPa 7401_a4075a-b9> |
≥735 MPa 7401_9f3f5a-7b> |
30%~32% 7401_6c36bd-e6> |
24% 7401_67c6b8-7d> |
13 J 7401_8ec532-56> |
Round steel:
Rolling size range: 10-260mm
Forging size range: 70-800mm
Square steel:
Thickness size range: 10-500mm, width size range: 200-810mm
Forged rings:
Outer diameter size can reach up to 1000mm
Application
1. Cutting Tools
Blades and Knives: D6 is widely used for industrial cutting tools, such as blades and knives, where excellent edge retention and wear resistance are required. It is particularly effective in cutting materials that are tough or abrasive.
Shear Blades: The steel’s ability to resist wear and maintain sharpness makes it an ideal choice for shear blades used in metalworking, plastics processing, and paper industries.
2. Stamping Dies
Forming and Cutting Dies: D6 is commonly used in manufacturing stamping dies for industries like automotive, aerospace, and heavy machinery. Its high wear resistance ensures that it can withstand repeated stamping and forming actions without significant degradation.
Coining Dies: It is also used in coining dies for producing detailed, high-precision metal parts, particularly in high-volume production.
3. Molds and Dies
Injection Molds: D6 tool steel is used for injection molds, especially those involving high-pressure molding processes. Its hardness and toughness make it suitable for molding plastics and metals where high abrasion resistance is essential.
Die Casting Dies: Due to its ability to resist wear under high temperatures and pressures, D6 is also used for die casting tools, particularly in the production of complex parts in industries like automotive and aerospace.
4. Cold Work Tools
Extrusion Dies: D6 is employed in extrusion dies, where it must resist high pressures and abrasions while maintaining dimensional accuracy during the extrusion process of metals, plastics, and rubber.
Bending Dies: D6 is used in tools for bending and forming metal in cold working processes, where resistance to deformation and wear is critical for maintaining tool life and ensuring precision.
5. Punches and Dies
Piercing and Blanking Tools: D6 is a common material for punches and blanking dies, particularly in applications requiring high strength and resistance to impact. It is used in industries such as automotive, where high-precision punching and blanking are essential for producing metal parts.
6. Woodworking Tools
Planer Blades: In the woodworking industry, D6 is used for planer blades and other cutting tools due to its toughness and wear resistance, which are needed to maintain sharp edges and smooth cuts during high-volume woodworking operations.
7. Food Processing Tools
Cutting and Slicing Tools: D6 is also used in the food processing industry for knives and slicers used to cut tough food materials. Its durability and wear resistance make it suitable for applications where tool longevity is important.
8. Aerospace and Automotive Components
Precision Dies and Components: In the aerospace and automotive industries, D6 tool steel is used for manufacturing high-precision dies and components that need to withstand wear, high pressures, and temperatures while maintaining dimensional accuracy.
9. Plastic Molding Tools
Compression Molds: D6 is used in compression molding tools for plastics, where its ability to maintain shape under high heat and pressure is crucial. The steel’s wear resistance ensures long-lasting performance in molding operations that involve tough materials.
Customer Testimonials
Good Toughness and Impact Resistance
Despite its high hardness, D6/1.2436 steel exhibits good toughness and impact resistance. This is particularly important for our tools that are subjected to high impact forces during operation. The steel’s ability to withstand such forces without cracking or deforming has significantly improved the reliability and durability of our products, making them suitable for demanding applications.
Low Distortion and High-Quality Surface Finish
One of the key advantages of D6/1.2436 steel is its low distortion during heat treatment. This ensures that our tools and molds maintain a high-quality surface finish, which is essential for producing precision parts. The minimal distortion also means that we can achieve tighter tolerances in our manufacturing processes, leading to higher quality and more consistent products.
Versatility in Applications
D6/1.2436 steel’s versatility is a major plus. It is suitable for a wide range of applications, from cutting tools and stamping dies to cold work molds and thread rolling dies. Its high wear resistance and good toughness make it an ideal choice for long-run tooling applications where precision and durability are critical. This has allowed us to use a single material for multiple applications, simplifying our material management and procurement processes.