Welcome to My Blog! 🌟
Before we dive into the content, I’d love for you to join me on my social media platforms. It’s where I share more insights, engage with our vibrant community, and post regular updates. Here’s how you can stay connected:
📘 Facebook: Connect with me on Facebook
Now, let’s embark on this journey together. I hope you find the content here insightful, engaging, and most importantly, valuable. Let’s explore, learn, and grow together! 🚀
Table of Contents
Introduction
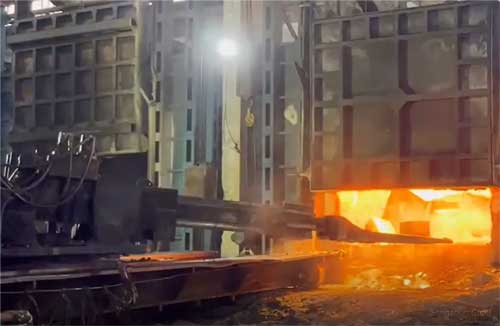
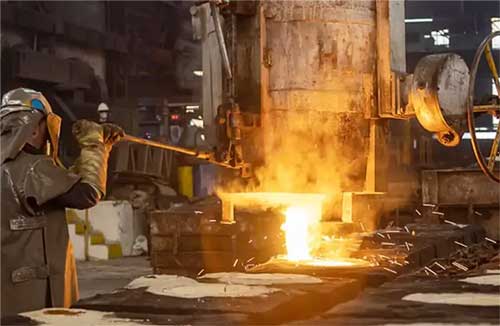
When it comes to high-performance tool steels, m42 steel often takes center stage. Known for its exceptional hardness and heat resistance, this material has become a favorite in industries that demand precision and durability. But is m42 steel truly worth the hype, or is it just another overrated material? In this comprehensive guide, we’ll dive deep into the properties, applications, advantages, and potential drawbacks of m42 steel to help you make an informed decision.
What is M42 Steel?
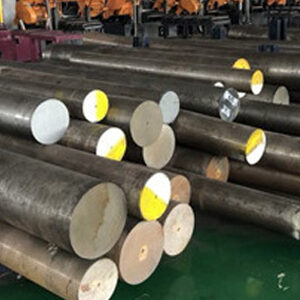
M42 steel is a high-speed tool steel that belongs to the cobalt-bearing family. It is renowned for its ability to maintain hardness even at elevated temperatures, making it ideal for cutting tools and other high-stress applications. The unique composition of m42 steel includes elements like cobalt, tungsten, and molybdenum, which contribute to its superior performance.
This steel is often used in manufacturing processes where tools are subjected to extreme conditions, such as high-speed machining or heavy-duty cutting. Its versatility and reliability have made it a popular choice among professionals.
Key Properties
To understand why this high-speed tool steel is so highly regarded, it’s essential to examine its key characteristics:
- High Hardness: This material boasts an impressive hardness level, often reaching up to 70 HRC (Rockwell Hardness Scale). This makes it suitable for applications that require sharp edges and long-lasting durability. Its exceptional hardness ensures that tools maintain their cutting efficiency even under demanding conditions.
- Heat Resistance: One of the standout features of this steel is its ability to retain hardness even at temperatures as high as 600°C (1112°F). This property makes it an excellent choice for high-speed machining and other applications where tools are exposed to extreme heat.
- Wear Resistance: Thanks to its unique composition, which includes cobalt, tungsten, and molybdenum, this material offers excellent resistance to wear and abrasion. This significantly extends the lifespan of tools, reducing the need for frequent replacements and maintenance.
- Toughness: Despite its impressive hardness, this steel maintains a good level of toughness. This balance reduces the risk of chipping or cracking under heavy use, making it a reliable choice for high-stress applications.
Applications
This high-performance material is widely used in various industries due to its exceptional properties. Here are some of the most common applications:
- Cutting Tools: It is a popular choice for manufacturing drill bits, end mills, and saw blades. Its ability to maintain sharpness and durability under high stress makes it ideal for these applications.
- Industrial Machinery: Components like gears and bearings made from this steel can withstand high stress and wear. This ensures that machinery operates efficiently and reliably over extended periods.
- Woodworking Tools: The hardness and sharpness of this material make it ideal for woodworking tools that require precision. Whether it’s chisels, planer blades, or carving tools, this steel delivers consistent performance.
- Aerospace Industry: The heat resistance of this material makes it suitable for aerospace applications where components are exposed to extreme temperatures. Its ability to maintain structural integrity under such conditions is highly valued in this industry.
Advantages
This high-speed tool steel offers several advantages that make it a top choice for professionals:
- Exceptional Performance: The combination of hardness, heat resistance, and wear resistance ensures that tools made from this material perform exceptionally well. Whether it’s cutting, drilling, or machining, this steel delivers reliable results.
- Longevity: Tools crafted from this steel have a longer lifespan compared to those made from other materials. This reduces the need for frequent replacements, saving both time and money in the long run.
- Versatility: This material can be used in a wide range of applications, making it a versatile choice for various industries. From manufacturing to woodworking, its adaptability is a significant advantage.
Potential Drawbacks
While this high-performance steel has many benefits, it’s important to consider its potential drawbacks:
- Cost: This material is more expensive than other tool steels, which may be a deterrent for some users. The higher cost is primarily due to its unique composition and the complex manufacturing process involved.
- Brittleness: Despite its toughness, this steel can be brittle under certain conditions, leading to chipping or cracking. Proper handling and usage are essential to minimize this risk.
- Complex Heat Treatment: Proper heat treatment is crucial for maximizing the performance of this material. However, the process can be complex and time-consuming, requiring specialized knowledge and equipment.
M42 Steel vs. Other Tool Steels
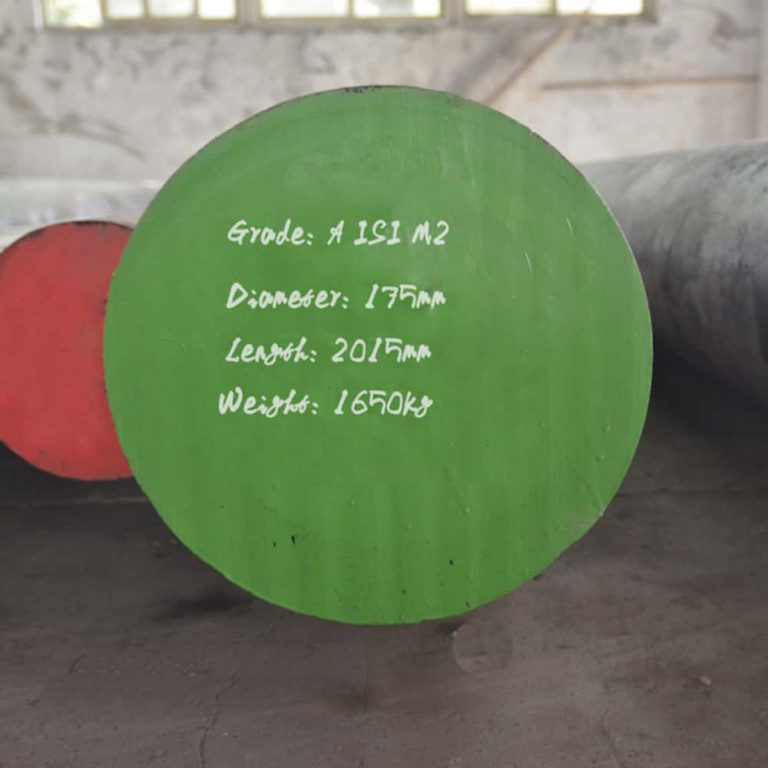
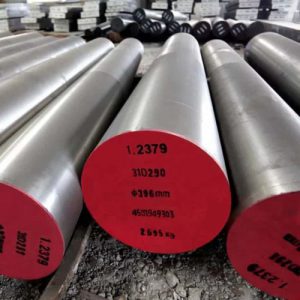
To better understand the value of m42 steel, let’s compare it to other popular tool steels. The table below highlights the key differences:
Property | M42 Steel | M2 Steel | D2 Steel |
---|---|---|---|
Hardness (HRC) | Up to 70 | Up to 65 | Up to 62 |
Heat Resistance | Excellent | Good | Moderate |
Wear Resistance | Excellent | Good | Good |
Cost | High | Moderate | Moderate |
As you can see, m42 steel outperforms other tool steels in terms of hardness and heat resistance, but it comes at a higher cost.
How to Care for M42 Steel Tools
To ensure the longevity and performance of tools made from m42 steel, proper care is essential. Here are some tips:
- Regular Sharpening: Keep the edges sharp to maintain optimal performance.
- Proper Storage: Store tools in a dry, cool place to prevent rust and corrosion.
- Avoid Overheating: While m42 steel is heat-resistant, excessive heat can still damage the material.
- Follow Manufacturer Guidelines: Always adhere to the manufacturer’s recommendations for use and maintenance.
Conclusion
So, is m42 steel worth the hype? The answer is a resounding yes—if you’re looking for a material that offers exceptional hardness, heat resistance, and durability. While it may come at a higher cost and require careful handling, the benefits of m42 steel far outweigh its drawbacks for professionals in demanding industries. Whether you’re in manufacturing, woodworking, or aerospace, m42 steel could be the ultimate solution for your high-performance tool needs.
FAQ
What makes m42 steel different from other tool steels?
This high-speed tool steel stands out due to its unique composition, particularly its high cobalt content. Cobalt is a key element that enhances the material’s hardness and heat resistance, making it superior to many other tool steels. While standard tool steels like M2 or D2 offer good performance, this material’s ability to retain hardness at temperatures as high as 600°C (1112°F) gives it a significant edge in demanding applications. Additionally, its wear resistance and toughness further distinguish it from alternatives, making it a preferred choice for professionals in industries that require precision and durability.
Is m42 steel suitable for DIY projects?
While this high-performance material is excellent for professional use, it may not be the best choice for casual DIYers. One of the primary reasons is its high cost, which can be prohibitive for hobbyists or those who don’t require industrial-grade tools. Additionally, its brittleness under certain conditions can pose challenges for users who may not have the expertise to handle it properly. For DIY projects, more affordable and user-friendly materials like carbon steel or stainless steel might be more practical options. However, for serious enthusiasts who value top-tier performance and are willing to invest in quality, this steel could still be a worthwhile consideration.
Can This Steel Be Used for Knives?
Yes, this high-speed tool steel is sometimes used for high-quality knives due to its exceptional sharpness and durability. Its high hardness allows for a fine, long-lasting edge, making it ideal for precision cutting tasks. However, its brittleness can be a drawback for knife applications, as it may be more prone to chipping compared to other knife steels like VG-10 or 154CM. Proper heat treatment and careful handling are essential to maximize its performance in knife-making. For those seeking a balance between sharpness and toughness, this material can be an excellent choice, especially for specialized knives used in professional settings.
How does m42 steel perform in high-speed machining?
This material excels in high-speed machining applications due to its ability to maintain hardness at elevated temperatures. When tools are subjected to the intense heat generated during high-speed cutting or drilling, many materials lose their hardness and wear out quickly. However, this steel’s heat resistance ensures that it retains its structural integrity and cutting efficiency even under extreme conditions. This makes it a go-to choice for industries like aerospace and automotive manufacturing, where precision and reliability are critical. Its performance in such applications is a testament to its superior engineering and material properties.
What is the best way to sharpen m42 steel tools?
To maintain the sharpness of tools crafted from this high-performance material, using a diamond or CBN (cubic boron nitride) sharpening stone is highly recommended. These materials are harder than the steel itself, making them effective at sharpening without causing damage. Traditional sharpening methods, such as using aluminum oxide stones, may not be sufficient due to the material’s high hardness. Additionally, it’s important to use consistent angles and gentle pressure during the sharpening process to avoid chipping or overheating the edges. Regular maintenance and proper sharpening techniques will ensure that tools made from this steel remain in peak condition for longer.