Introduction
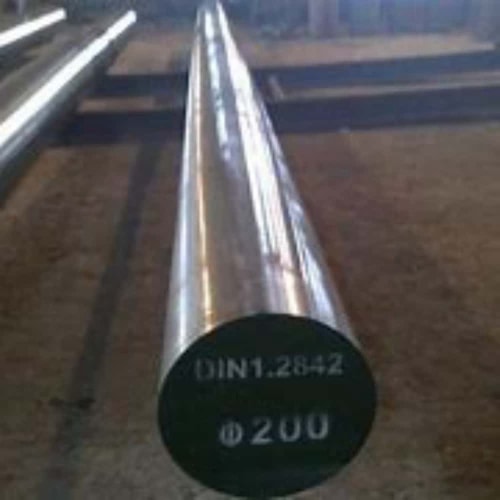
O2 tool steel is highly valued in industries requiring robust hardness and wear resistance. This type of steel, known for its high carbon and chromium content, finds extensive use in manufacturing cutting tools, blanking dies, and precision instruments. Achieving and maintaining optimal hardness in O2 tool steel is crucial for ensuring tool longevity and performance. This blog delves into the critical role that heat treatment plays in enhancing O2 tool steel hardness, exploring key concepts, methods, and practical considerations.
Understanding O2 Tool Steel Hardness
O2 tool steel belongs to the category of oil-hardening tool steels, renowned for their excellent hardness properties. The hardness of O2 tool steel directly influences its ability to withstand abrasive wear, deformation, and mechanical stresses during use. This makes it suitable for applications where tools are subjected to high impact and abrasive forces, such as cutting, shaping, and forming operations.
Importance of Heat Treatment
Heat treatment is indispensable for optimizing the hardness of O2 tool steel. This process involves controlled heating, soaking at specific temperatures, and rapid cooling (quenching) to achieve desired mechanical properties. The primary objectives of heat treatment include refining the microstructure, enhancing hardness, improving toughness, and relieving internal stresses. Proper heat treatment ensures uniformity in hardness throughout the material, thereby enhancing the overall performance and durability of tools made from O2 tool steel.
Heat Treatment Methods for O2 Tool Steel
Several heat treatment methods are employed to achieve different hardness levels and mechanical properties in O2 tool steel:
- Annealing: This process involves heating the steel to a temperature within the range of 760-800°C (1400-1470°F), followed by slow cooling in a furnace. Annealing softens the steel, making it easier to machine and reducing internal stresses.
- Normalizing: Normalizing improves the machinability and refines the grain structure of O2 tool steel. The steel is heated to a temperature between 840-870°C (1540-1600°F) and then cooled in still air. This process enhances uniformity in microstructure and prepares the steel for subsequent heat treatment operations.
- Hardening: Hardening increases the hardness and wear resistance of O2 tool steel. The steel is heated to a critical temperature range of 780-820°C (1435-1500°F), depending on the desired hardness, and then rapidly cooled (quenched) in oil or air. Quenching results in the formation of martensite, a hard crystalline structure that contributes to the steel’s hardness.
- Tempering: Tempering follows the hardening process to reduce brittleness and improve toughness. The hardened steel is heated to a temperature between 150-300°C (300-570°F) for a specific duration and then cooled. Tempering allows for the adjustment of hardness and ensures the steel retains adequate strength and ductility for its intended application.
Practical Considerations and Techniques
Achieving consistent hardness and mechanical properties in O2 tool steel requires careful control of heat treatment parameters:
Typical Heat Treatment Parameters for O2 Tool Steel Hardness
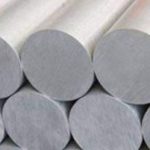
Process | Temperature Range (°C) | Heating Rate (°C/h) | Soaking Time (hours) | Quenching Medium |
---|---|---|---|---|
Annealing | 760-800 | 10-20 | 1-2 | Furnace |
Normalizing | 840-870 | 20-40 | 1 | Air |
Hardening | 780-820 (critical temp) | 20-40 | 30 minutes | Oil or Air |
Tempering | 150-300 | – | 1-2 | Furnace or Air |
Successful heat treatment also involves considerations such as heating rate, soaking time, quenching medium, and tempering temperature. These parameters are critical for achieving the desired combination of hardness, toughness, and dimensional stability in O2 tool steel.
Conclusion
In conclusion, heat treatment is essential for enhancing the hardness and overall performance of O2 tool steel. By carefully selecting and applying appropriate heat treatment methods, manufacturers can optimize the mechanical properties of O2 tool steel to meet the specific demands of their applications. Understanding the relationship between heat treatment parameters and steel hardness is fundamental for achieving consistent quality and reliability in industrial tooling and manufacturing processes.
FAQ
Q: How does heat treatment affect O2 tool steel hardness?
A: Heat treatment alters the microstructure of O2 tool steel, influencing its hardness, toughness, and wear resistance properties. Proper heat treatment enhances the steel’s ability to withstand mechanical stresses and abrasive wear.
Q: What are the common challenges in heat treating O2 tool steel?
A: Common challenges include achieving uniform hardness throughout the material, minimizing distortion during quenching, and controlling dimensional changes.
Q: Why is hardness important in O2 tool steel applications?
A: Hardness directly impacts the cutting performance, wear resistance, and longevity of tools and components made from O2 tool steel, ensuring reliable operation in demanding industrial environments.