Introduction
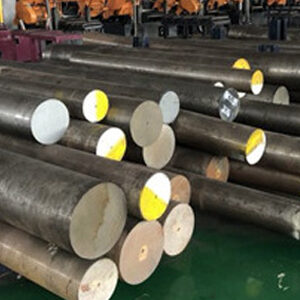
Heat treating O1 tool steel at home can be a rewarding process, providing you with the ability to customize the hardness and durability of your tools to suit your specific needs. In this comprehensive guide, we’ll walk you through the steps to achieve optimal results when heat treating O1 tool steel in your own workshop.
Understanding O1 Tool Steel
Before delving into the intricacies of the heat treatment process, it’s imperative to grasp the fundamental characteristics of O1 tool steel. Renowned for its exceptional properties, O1 is categorized as a general-purpose oil-hardening tool steel. This alloy is highly esteemed for its remarkable wear resistance, toughness, and machinability, making it a preferred choice across various industrial sectors.
O1 tool steel finds widespread application in the fabrication of a myriad of precision components, owing to its versatility and reliability. Its inherent qualities render it ideal for crafting cutting tools, punches, dies, and other intricate parts requiring high precision and durability. Whether in the realms of manufacturing, engineering, or craftsmanship, O1 tool steel stands as a stalwart material, offering unparalleled performance and longevity.
This alloy’s ability to withstand wear and abrasion while maintaining structural integrity makes it indispensable in demanding environments. From machining operations to metalworking processes, O1 tool steel consistently delivers exceptional results, earning it a distinguished reputation among professionals and enthusiasts alike.
In essence, comprehending the inherent attributes and applications of O1 tool steel lays a solid foundation for mastering the art of heat treatment. By harnessing its unique properties through precise heat treatment techniques, artisans and engineers can unlock its full potential, unleashing a realm of possibilities in their respective fields of expertise.
Preparation and Safety Measures
Before embarking on the heat treatment journey, prioritizing safety measures and assembling the requisite equipment are paramount. This ensures a smooth and secure process, safeguarding both the practitioner and the surrounding environment. Let’s delve into each aspect in detail:
Safety Gear: To shield oneself from potential hazards during the heat treatment process, it’s imperative to don appropriate safety gear. This includes:
- Heavy-duty gloves: Protect hands from burns and potential splinters.
- Safety glasses: Safeguard eyes from flying debris or sparks.
- Heat-resistant clothing: Wear clothing made from fire-retardant materials to minimize the risk of burns or injuries.
Tools and Equipment: Equipping oneself with the necessary tools and equipment is essential for executing a successful heat treatment procedure. These include:
- Heat source: Depending on the scale of the operation and personal preference, utilize either a propane torch or a forge to achieve the required temperatures for heat treatment.
- Quenching medium: Select an appropriate quenching medium, such as oil or water, based on the specific requirements of the steel being treated.
- Temperature-measuring devices: Utilize precision instruments like a pyrometer or temperature-indicating sticks to monitor and maintain the desired heat levels accurately.
Preparing the Work Area: Creating a conducive work environment minimizes the likelihood of accidents and enhances efficiency during the heat treatment process. Here are some key considerations:
- Adequate ventilation: Ensure proper ventilation to disperse fumes and gases emitted during heating and quenching processes.
- Fire safety measures: Have fire extinguishing equipment readily accessible in case of emergencies.
- Clean and organized workspace: Clear clutter and ensure a tidy workspace to minimize tripping hazards and facilitate smooth movement during the procedure.
Heat Treatment Process for O1 Tool Steel
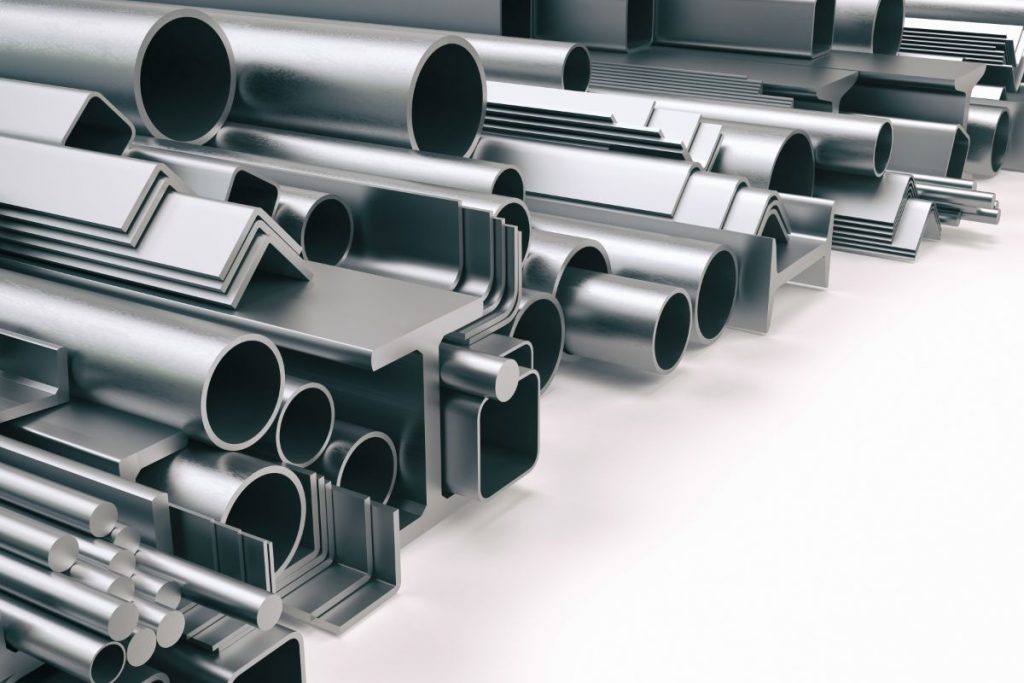
The heat treatment process for O1 tool steel encompasses three crucial stages, each playing a distinct role in optimizing the material’s properties. Let’s delve deeper into each step:
Annealing: Annealing is the initial stage of the heat treatment process, aimed at refining the microstructure of O1 tool steel. During annealing, the steel is heated to a specific temperature, typically between 1400°F and 1600°F (760°C and 870°C), and held at this temperature for a predetermined period. This allows the internal stresses accumulated during machining or previous processing to be relieved, promoting uniformity and reducing the risk of distortion or cracking.
As the steel gradually cools down in the furnace or kiln, its molecular structure undergoes a transformation, becoming more homogeneous and ductile. This softens the steel, making it more machinable and easier to work with, thereby enhancing its formability and facilitating subsequent processing steps.
Hardening: Following annealing, the hardened stage of the heat treatment process involves transforming the O1 tool steel into its hardened state to achieve maximum hardness and wear resistance. This is achieved through a carefully controlled heating and quenching process:
- Heating: The steel is heated to a critical temperature known as the austenitizing temperature, typically around 1450°F to 1600°F (790°C to 870°C), depending on the specific composition of the steel and desired hardness level. This temperature is held for a specified duration to ensure uniformity throughout the steel’s structure.
- Quenching: Once the steel reaches the austenitizing temperature, it is rapidly quenched in a suitable medium, such as oil or water, to cool it down quickly and lock in the desired hardness. The choice of quenching medium depends on factors such as the steel’s composition, thickness, and intended application.
The rapid cooling during quenching transforms the austenite phase into martensite, a hard and brittle phase that imparts maximum hardness to the steel. However, the steel at this stage is overly brittle and prone to cracking, necessitating the final stage of the heat treatment process: tempering.
Tempering: Tempering is the critical stage where the hardened steel is reheated to a specific temperature and then cooled to enhance its toughness, ductility, and overall mechanical properties. This process involves:
- Reheating: The hardened steel is heated to a precise temperature range, typically between 350°F and 600°F (175°C and 315°C), depending on the desired balance of hardness and toughness. The exact tempering temperature is determined based on factors such as the intended application and required mechanical properties.
- Cooling: Once the steel reaches the designated tempering temperature, it is allowed to cool naturally or quenched in air to gradually reduce its hardness and brittleness. This controlled cooling process enables the transformation of martensite into a more stable and ductile structure, thereby improving the steel’s toughness and resilience while retaining adequate hardness for its intended application.
Optimizing Heat Treatment Parameters
Achieving the desired hardness and performance characteristics of O1 tool steel depends on various factors, including:
Heating rate and soaking time: Controlling the rate at which the steel is heated and the duration of time it is held at the austenitizing temperature.
Quenching method and medium: Selecting the appropriate quenching medium (such as oil, water, or air) and ensuring uniform cooling to prevent distortion or cracking.
Tempering temperature and duration: Determining the tempering temperature and holding time to achieve the desired balance of hardness and toughness.
Factor | Description |
---|---|
Heating Rate and Soaking Time | Controlling the rate at which the steel is heated and the duration of time it is held at the austenitizing temperature. |
Quenching Method and Medium | Selecting the appropriate quenching medium (such as oil, water, or air) and ensuring uniform cooling to prevent distortion or cracking. |
Tempering Temperature and Duration | Determining the tempering temperature and holding time to achieve the desired balance of hardness and toughness. |
FAQ
Can I heat treat O1 tool steel without a forge?
Yes, you can use a propane torch or even a kitchen oven for heat treating O1 tool steel at home, although a forge provides more precise temperature control.
What is the ideal hardness for O1 tool steel after heat treatment?
The ideal hardness depends on the specific application of the tool. Generally, O1 tool steel is hardened to a Rockwell hardness of around 60-62 HRC for cutting tools and 55-58 HRC for impact tools.
How do I know if my O1 tool steel has been properly hardened and tempered?
You can perform hardness testing using a Rockwell hardness tester or a file test. Properly hardened and tempered O1 tool steel should have a uniform hardness throughout the material and should resist deformation when subjected to impact.
Can I reheat treat O1 tool steel if I’m not satisfied with the initial results?
Yes, O1 tool steel can be reheat treated if necessary. However, it’s essential to carefully anneal the steel before rehardening and tempering to avoid the risk of cracking or other metallurgical issues.
Are there any safety risks associated with heat treating O1 tool steel at home?
Yes, heat treating O1 tool steel involves working with high temperatures and potentially hazardous materials. It’s crucial to follow proper safety procedures, wear appropriate protective gear, and work in a well-ventilated area to minimize the risk of accidents or injuries.
Conclusion
Mastering the art of heat treating O1 tool steel at home requires patience, practice, and attention to detail. By following the guidelines outlined in this guide and experimenting with different parameters, you can achieve optimal results and unlock the full potential of O1 tool steel for your projects.