Introduction
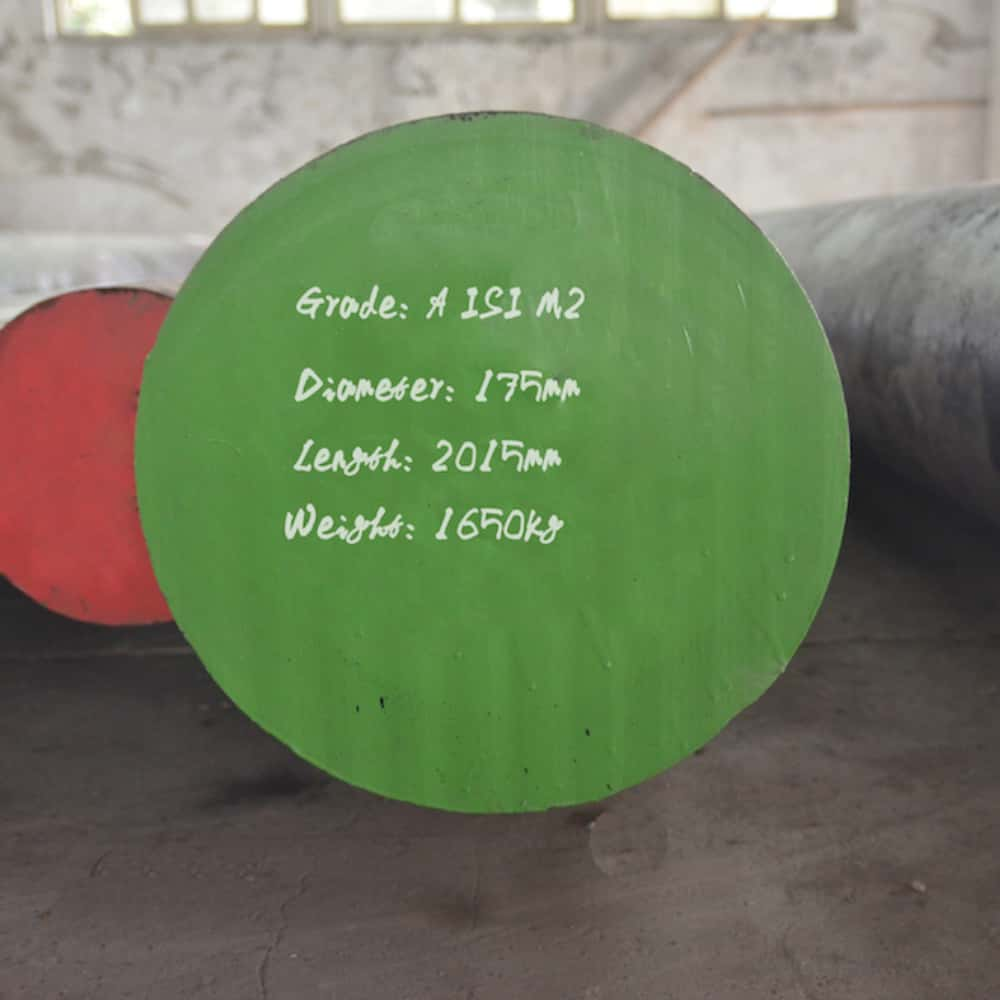
M2 tool steel, renowned for its exceptional hardness, wear resistance, and toughness, is a preferred material in the manufacturing of cutting tools, drills, and other high-speed machining applications. This guide aims to provide comprehensive insights into identifying and selecting high-quality M2 tool steel products to ensure optimal performance and durability in industrial settings.
Properties of M2 Tool Steel
M2 tool steel exhibits several key properties that make it suitable for demanding applications:
- High Hardness: M2 tool steel is renowned for its impressive hardness, typically ranging between 60 and 65 HRC on the Rockwell C scale. This hardness not only ensures superior edge retention and wear resistance but also maintains dimensional stability under high temperatures. Even when subjected to intense heat generated during high-speed machining operations, M2 tool steel retains its hardness, preserving the tool’s cutting effectiveness and prolonging its operational lifespan.
- Excellent Wear Resistance: The exceptional wear resistance of M2 tool steel is attributed to its microstructure and alloy composition. Its fine grain structure, combined with elements like tungsten and molybdenum, forms hard carbides that resist abrasion and friction. This capability allows tools made from M2 steel to maintain sharp cutting edges and withstand prolonged use without significant wear. Such wear resistance is crucial in industrial applications where tools encounter harsh conditions, ensuring consistent performance and reducing downtime for tool replacement.
- Good Toughness: Despite its high hardness and wear resistance, M2 tool steel exhibits good toughness, which is vital for withstanding impact loads and preventing fracture. This toughness is achieved through careful alloying and heat treatment processes that balance hardness with resilience. It enables M2 tool steel to endure sudden shocks and vibrations during machining operations without compromising structural integrity or risking tool failure. This combination of hardness and toughness makes M2 tool steel a preferred choice for applications requiring both cutting precision and durability in challenging environments.
Chemical Composition
Understanding the precise chemical composition of M2 tool steel is essential for ensuring consistent quality and performance:
Element | Percentage (%) |
---|---|
Carbon (C) | 0.78 – 0.88 |
Manganese (Mn) | 0.15 – 0.40 |
Silicon (Si) | 0.20 – 0.45 |
Chromium (Cr) | 3.75 – 4.50 |
Vanadium (V) | 1.75 – 2.20 |
These elements contribute to the steel’s hardness, wear resistance, and toughness, with careful control necessary during manufacturing to achieve desired properties.
Manufacturing Standards
Quality assurance begins with adherence to recognized manufacturing standards such as AISI (American Iron and Steel Institute) M2 or equivalent international standards. Certifications and compliance with these standards ensure consistency and reliability in M2 tool steel products.
Identification Techniques
Ensuring the authenticity and quality of M2 tool steel involves rigorous identification processes:
- Material Certification: Suppliers should provide certificates detailing chemical composition, mechanical properties, and conformity with relevant standards.
- Physical Tests: Conducting hardness tests (e.g., Rockwell or Vickers) verifies the steel’s hardness level, critical for its performance.
- Microstructure Examination: Analysis of the steel’s microstructure under a microscope ensures uniformity and absence of defects.
Selection Criteria
Selecting the right M2 tool steel product depends on several factors:
- Application Requirements: Consider the specific demands of the application, such as cutting speed, material hardness, and operating conditions.
- Supplier Reputation: Opt for reputable suppliers known for consistent quality and adherence to standards.
- Cost-Effectiveness: Balance initial cost with long-term performance and tool life to optimize investment.
Maintenance and Care
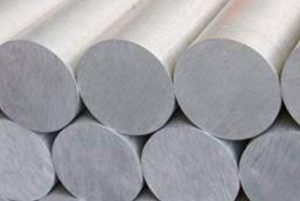
Maintaining M2 tool steel tools is essential for maximizing their lifespan and performance:
- Proper Storage: Store tools in a dry environment to prevent corrosion and maintain edge sharpness.
- Regular Maintenance: Schedule routine inspections, re-sharpening, and lubrication to sustain cutting efficiency.
- Temperature Management: Avoid overheating during use to preserve the steel’s hardness and mechanical properties.
Conclusion
Identifying and selecting quality M2 tool steel products involves understanding its properties, verifying compliance with standards, and assessing suitability based on application-specific requirements. By following proper identification, selection, and maintenance practices, manufacturers can ensure optimal tool performance and longevity in diverse industrial applications.
FAQ
Q:What are the primary applications of M2 tool steel?
A:M2 tool steel is extensively used in manufacturing high-speed cutting tools, drills, taps, and milling cutters due to its high hardness and wear resistance.
Q:How does M2 tool steel compare to other tool steels like D2 or A2?
A:Compared to D2 and A2 tool steels, M2 offers superior hardness and hot hardness, making it suitable for applications requiring high-speed cutting and machining.
Q:Can M2 tool steel be hardened?
A:Yes, M2 tool steel can be hardened through heat treatment processes to achieve the desired hardness level for specific applications.
Q:What are some common heat treatment methods for M2 tool steel?
A:Typical heat treatment methods include annealing, hardening, tempering, and cryogenic treatment to optimize the steel’s properties for different applications.
Q:How can I ensure I am purchasing genuine M2 tool steel?
A:Verify material certifications, conduct physical tests, and purchase from reputable suppliers known for quality and reliability.