Welcome to My Blog! 🌟
Before we dive into the content, I’d love for you to join me on my social media platforms. It’s where I share more insights, engage with our vibrant community, and post regular updates. Here’s how you can stay connected:
📘 Facebook: Connect with me on Facebook
Now, let’s embark on this journey together. I hope you find the content here insightful, engaging, and most importantly, valuable. Let’s explore, learn, and grow together! 🚀
Table of Contents
Introduction
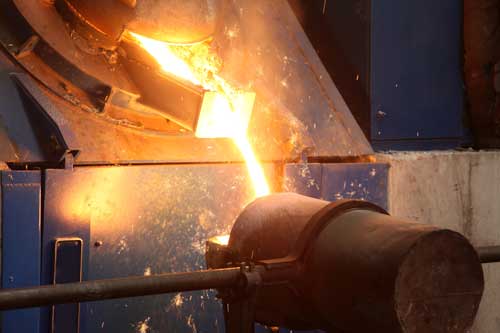
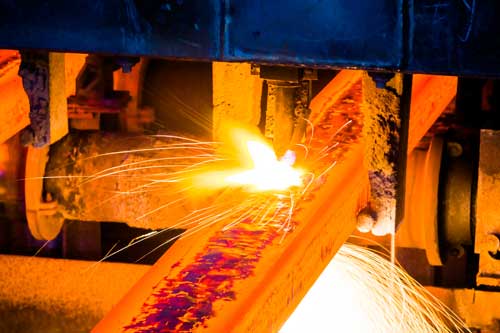
In the competitive world of manufacturing, efficiency is the key to success. With industries constantly striving to reduce costs, improve output, and maintain high-quality standards, the choice of materials plays a pivotal role in achieving these goals. Among the various materials available, P20 mold steel has emerged as a game-changer, offering unparalleled advantages in production processes. Its unique properties and versatility have made it a go-to material for manufacturers across sectors, from automotive to electronics and medical devices.
This blog delves into the reasons behind the growing popularity of P20 mold steel and explores how it can boost production efficiency by up to 40%. We’ll take a closer look at its defining characteristics, the industries it benefits, and the best practices for optimizing its use. Whether you’re a seasoned manufacturer or new to the field, understanding the potential of P20 mold steel can help you make informed decisions that drive productivity and profitability.
What is P20 Mold Steel?
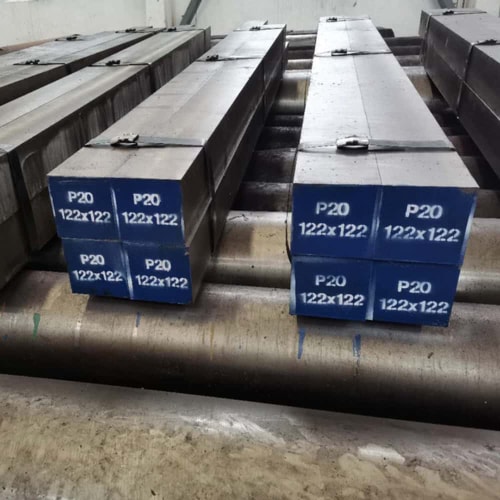
P20 mold steel is a pre-hardened plastic mold steel known for its exceptional hardness, toughness, and polishability. It is widely used in industries such as automotive, electronics, and medical devices due to its ability to withstand high-stress environments. Its uniform hardness and excellent machinability make it a preferred choice for manufacturers aiming to enhance productivity.
Key Properties of P20 Mold Steel
High-performance mold steel, such as the widely used P20 grade, is celebrated for its exceptional properties that make it a top choice in various manufacturing and molding applications. Below are the key attributes that contribute to its efficiency and effectiveness:
- High Hardness: This type of steel exhibits a surface hardness of 50-55 HRC (Rockwell Hardness Scale), ensuring remarkable durability and resistance to wear and tear. Such high hardness is crucial for maintaining the integrity of molds over extended periods, even under high-stress conditions.
- Excellent Machinability: One of the standout features is its pre-hardened state, which allows for direct machining without the need for additional heat treatment. This characteristic significantly reduces production time and simplifies the manufacturing process, making it highly efficient for industrial applications.
- Superior Polishability: Capable of achieving a mirror-like finish, this steel is essential for producing high-quality molds. Its superior polishability ensures that the final products have a smooth and flawless surface, reducing the need for post-processing and enhancing the overall aesthetics of the molded parts.
- Thermal Conductivity: The high thermal conductivity facilitates faster cooling and heating cycles during the molding process. This property not only speeds up production but also helps in maintaining consistent mold temperatures, which is critical for achieving uniform product quality.
- Chemical Composition: The chemical composition includes elements like Carbon (C: 0.28-0.40%), Silicon (Si: 0.20-0.80%), Manganese (Mn: 0.60-1.00%), Molybdenum (Mo: 0.30-0.55%), Chromium (Cr: 1.40-2.00%), and Nickel (Ni: 0.80-1.20%). These elements collectively contribute to the steel’s strength, toughness, and resistance to corrosion, making it highly reliable for demanding applications.
Applications of P20 Mold Steel
This versatile material finds applications across a wide range of industries. Its unique properties make it suitable for various high-performance and precision-driven tasks:
- Automotive: In the automotive sector, it is extensively used for manufacturing critical components such as car body parts, doors, and brake systems. Its durability and ability to withstand high pressures make it ideal for producing reliable and long-lasting automotive parts.
- Electronics: The electronics industry benefits from its use in the production of casings, connectors, and other precision components. Its superior polishability ensures that electronic parts have a high-quality finish, which is essential for both functionality and aesthetics.
- Medical Devices: It is employed in the medical field for creating surgical instruments and implants. Its biocompatibility, combined with its strength and corrosion resistance, makes it a trusted material for producing medical devices that meet stringent quality and safety standards.
- Consumer Goods: The consumer goods industry utilizes it for molding high-quality plastic products such as toys, appliances, and household items. Its ability to produce smooth and detailed finishes ensures that consumer products are both attractive and durable.
- Heavy Duty Molds: Due to its enhanced performance characteristics, it is particularly suitable for large-sized and high-end plastic molds. Its ability to endure prolonged use without significant wear makes it an excellent choice for heavy-duty applications in various industries.
How High-Performance Mold Steel Enhances Production Efficiency
This type of steel plays a pivotal role in boosting production efficiency by offering several advantages that streamline manufacturing processes and improve overall output quality:
- Reduced Downtime: The durability and high hardness minimize the need for frequent replacements or repairs, thereby reducing downtime. This ensures that production lines remain operational for longer periods, leading to increased productivity.
- Faster Processing: The high thermal conductivity accelerates the cooling and heating cycles during the molding process. This results in faster processing times, allowing manufacturers to produce more parts in a shorter period.
- Cost Savings: Since it is supplied in a pre-hardened state, it eliminates the need for additional heat treatment. This not only saves time but also reduces energy consumption and associated costs, contributing to overall cost efficiency in production.
- Improved Product Quality: The superior polishability ensures that the final products have a high-quality finish. This reduces the need for rework or additional finishing processes, leading to better product quality and customer satisfaction.
- Extended Mold Life: Properly maintained, this steel can last up to 500,000 cycles, significantly extending the life of the molds. This reduces the frequency of mold replacements, thereby lowering long-term production costs and enhancing operational efficiency.
Best Practices for Using P20 Mold Steel
To maximize the benefits of P20 mold steel, follow these guidelines:
- Proper Material Selection: Choose the right grade of P20 mold steel based on specific manufacturing needs.
- Precision Machining: Ensure accurate machining to avoid defects like cracks or deformities.
- Regular Maintenance: Conduct timely maintenance to preserve the material’s sharpness and performance.
- Optimal Processing Parameters: Use appropriate cooling rates and temperatures to prevent issues like warping.
- Nitriding Treatment: For applications requiring extended mold life, consider nitriding to achieve surface hardness of 650-700HV, enhancing durability.
Table: Comparison of P20 Mold Steel with Other Materials
Property | P20 Mold Steel | H13 Mold Steel | 1.2738 Mold Steel |
---|---|---|---|
Hardness (HRC) | 50-55 | 48-52 | 52-56 |
Machinability | Excellent | Good | Moderate |
Polishability | Superior | Good | Good |
Thermal Conductivity | High | Moderate | Moderate |
Cost Efficiency | High | Moderate | Low |
Case Studies: Real-World Efficiency Gains
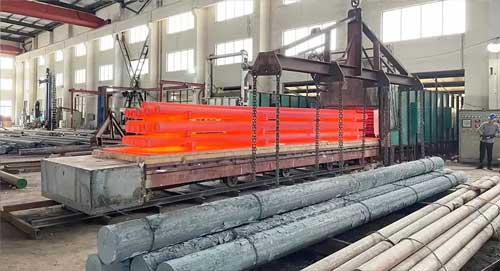
Several manufacturers have reported significant efficiency improvements after switching to P20 mold steel:
- Automotive Industry: A car parts manufacturer reduced production time by 35% and maintenance costs by 20%.
- Electronics Sector: A consumer electronics company achieved a 40% increase in output by optimizing cooling cycles.
- Medical Devices: A surgical instrument producer improved product quality and reduced defects by 25%.
- Progressive Die Stamping: A manufacturer using P20 steel for automotive parts reported a tool life of 250,000 to 500,000 shots, significantly reducing downtime.
Conclusion
P20 mold steel is a powerhouse material that significantly enhances production efficiency. Its unique properties, versatility, and cost-effectiveness make it an indispensable tool for manufacturers across industries. By adopting best practices and leveraging its advantages, businesses can achieve up to a 40% boost in productivity, ensuring a competitive edge in the market.
By understanding and utilizing P20 mold steel effectively, manufacturers can unlock new levels of efficiency and quality in their production processes. Whether it’s automotive, electronics, or medical devices, P20 mold steel proves to be a reliable and efficient choice for modern manufacturing needs.
FAQ
Q1: Can P20 mold steel be heat-treated?
A1: P20 mold steel is typically supplied in a pre-hardened state, which means it has already undergone the necessary heat treatment processes to achieve its optimal hardness and mechanical properties. This pre-hardened condition eliminates the need for additional heat treatment, making it highly convenient for manufacturers. However, in some specific cases where further customization is required, P20 mold steel can undergo additional heat treatment processes such as annealing, quenching, and tempering. These processes can further refine its properties to meet specific application demands. Nonetheless, for most standard applications, the pre-hardened state is perfectly adequate, saving both time and resources.
Q2: What industries benefit most from P20 mold steel?
A2: Automotive, electronics, medical devices, and consumer goods industries see the most significant benefits.
Q3: How does P20 mold steel compare to H13 mold steel?
A3: P20 mold steel offers better machinability and polishability, making it more suitable for precision molds.
Q4: What is the lifespan of P20 mold steel?
A4: The lifespan of P20 mold steel is notably impressive, especially when it is properly maintained. Under optimal conditions and with regular upkeep, P20 mold steel can last up to 500,000 production cycles. This extended lifespan is attributed to its high hardness, durability, and resistance to wear and tear. Proper maintenance practices, such as regular cleaning, lubrication, and timely inspections, can significantly enhance its longevity. Additionally, avoiding excessive mechanical stress and ensuring that the mold is used within its designed parameters can further extend its service life. This durability not only reduces the frequency of mold replacements but also contributes to long-term cost savings and consistent production quality.
Q5: Can P20 mold steel be used for high-temperature applications?
A5: While P20 mold steel performs exceptionally well in moderate temperature applications, it is not ideally suited for extreme high-temperature environments. Its properties are optimized for applications where temperatures remain within a moderate range, ensuring consistent performance and durability. For high-temperature applications, such as die-casting or forging, materials like H13 mold steel are more appropriate due to their superior thermal resistance and ability to withstand thermal fatigue. H13 mold steel can endure the intense heat and thermal cycling associated with such processes without compromising its structural integrity. Therefore, while P20 mold steel is an excellent choice for precision molds and moderate temperature conditions, alternative materials should be considered for high-temperature scenarios to ensure optimal performance and longevity.