Introduction
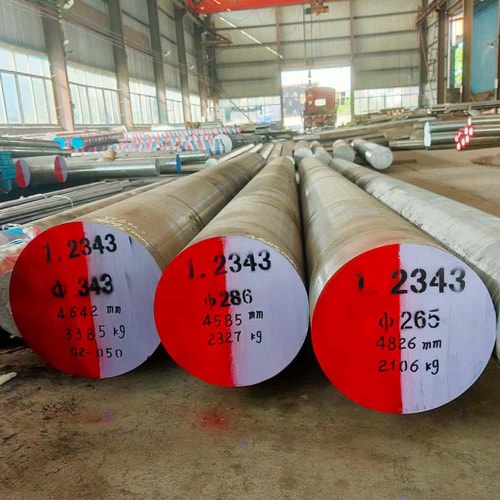
H11 tool steel hardness plays a critical role in determining the effectiveness and durability of tools used in various manufacturing processes. This blog will delve into how H11 tool steel hardness affects tool performance and longevity, exploring the intricacies involved and providing useful insights for industry professionals.
Understanding H11 Tool Steel
What is H11 Tool Steel?
H11 tool steel is a type of hot-work tool steel known for its excellent properties, making it suitable for high-temperature applications. Its chemical composition includes chromium, molybdenum, and vanadium, which contribute to the unique characteristics of H11 tool steel hardness.
Properties of H11 Tool Steel
Property | Value |
---|---|
Hardness | 48-52 HRC |
Density | 7.85 g/cm³ |
Tensile Strength | 1,450 MPa |
Toughness | High |
Thermal Conductivity | Moderate |
These properties are influenced significantly by H11 tool steel hardness, affecting its overall performance.
The Importance of Hardness in Tool Performance
How Hardness Affects Tool Performance
H11 tool steel hardness is pivotal in enhancing tool performance. Harder materials can endure greater loads and resist wear, making them ideal for heavy-duty applications. However, excessive hardness can lead to brittleness, potentially causing tool failure.
Ideal Hardness Range for H11 Tool Steel
The optimal hardness for H11 tool steel typically falls between 48-52 HRC. This range offers a balance of toughness and wear resistance, crucial for maintaining tool performance over time.
Hardness (HRC) | Performance Characteristics |
---|---|
48-50 | Balanced performance, high toughness |
50-52 | Increased wear resistance, potential brittleness |
How Hardness Influences Tool Longevity
Longevity Factors in Tool Steel
The longevity of tools made from H11 tool steel is essential for cost efficiency and productivity. Several factors related to H11 tool steel hardness influence tool longevity, including wear resistance, thermal stability, and toughness.
The Impact of Hardness on Wear Resistance
Higher levels of H11 tool steel hardness typically lead to improved wear resistance. Tools with optimal hardness can maintain their cutting edges longer, resulting in reduced replacement frequency and increased cost-effectiveness.
Hardness (HRC) | Expected Tool Life (Hours) |
---|---|
48-50 | 1,500 |
50-52 | 2,000 |
Applications of H11 Tool Steel
Common Uses in Industry
H11 tool steel is widely utilized in various high-temperature and high-stress applications, such as:
- Hot work tooling
- Die casting
- Forging dies
- Hot extrusion dies
These applications demand materials that can withstand extreme conditions while maintaining optimal performance, largely influenced by H11 tool steel hardness.
Performance in Specific Applications
In die casting, for example, maintaining H11 tool steel hardness around 50 HRC is critical. This hardness level provides a favorable balance between toughness and wear resistance, ensuring prolonged tool life and reliability in high-stress environments.
Hardness Testing Methods
Common Hardness Testing Techniques
To ensure that H11 tool steel meets the necessary hardness specifications, various testing methods are employed. The most common include:
- Rockwell Hardness Test
- Brinell Hardness Test
- Vickers Hardness Test
The choice of testing method may depend on the required precision and the specific application related to H11 tool steel hardness.
Test Method | Scale | Typical Applications |
---|---|---|
Rockwell | HRC | General tool hardness |
Brinell | HB | Large-scale applications |
Vickers | HV | Microhardness testing |
Factors Affecting H11 Tool Steel Hardness
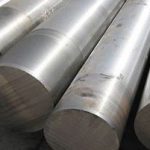
Heat Treatment Processes
Achieving the desired H11 tool steel hardness primarily involves precise heat treatment processes. Proper quenching and tempering are essential to ensure that the hardness level meets the required standards for effective tool performance.
Environmental Conditions
Environmental factors during manufacturing, such as humidity and contamination, can significantly affect H11 tool steel hardness. Proper handling and storage are vital in preserving the desired hardness and overall material integrity.
Conclusion
H11 tool steel hardness is a fundamental aspect that significantly influences tool performance and longevity. Understanding the optimal hardness range and its effects on wear resistance, toughness, and suitability for various applications is crucial for manufacturers. By adhering to best practices in heat treatment and maintenance, companies can enhance the durability and efficiency of their tools, ultimately leading to increased productivity and reduced operational costs.
FAQ
Q:What is the typical hardness of H11 tool steel?
A:The typical hardness of H11 tool steel ranges from 48-52 HRC.
Q:How does hardness affect tool life?
A:Higher H11 tool steel hardness usually results in increased wear resistance, contributing to a longer tool life.
Q:What are the common applications of H11 tool steel?
A:H11 tool steel is commonly used in die casting, forging, and hot extrusion dies.
Q:What hardness testing methods are used for H11 tool steel?
A:Common methods for testing H11 tool steel hardness include Rockwell, Brinell, and Vickers hardness tests.
Q:Can H11 tool steel become brittle?
A:Yes, excessive hardness can lead to brittleness in H11 tool steel, making tools susceptible to fracture.
Q:How does heat treatment affect H11 tool steel hardness?
A:Proper heat treatment is critical in achieving the desired H11 tool steel hardness, affecting the final performance of the tools.
Q:Why is hardness important in tool steel?
A:H11 tool steel hardness is vital as it influences wear resistance, toughness, and overall tool performance and longevity.