Introduction
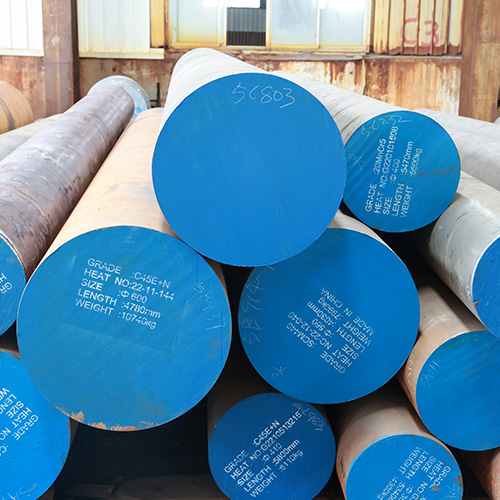
Hot work tool steels are integral to the die casting industry, providing essential properties such as thermal stability and mechanical strength necessary for withstanding high-temperature environments. This blog delves into the diverse applications of hot work tool steels in die casting, highlighting their advantages, specific uses, and considerations for selection.
Properties of Hot Work Tool Steels
Hot work tool steels are characterized by a combination of high hardness, excellent toughness, and good thermal conductivity. These properties enable them to maintain dimensional stability and withstand thermal fatigue, making them ideal for die casting applications where tools are exposed to extreme temperature variations.
Table summarizes the key properties of some commonly used hot work tool steels:
Steel Grade | Hardness (HRC) | Thermal Conductivity (W/m·K) | Toughness (J) |
---|---|---|---|
H13 | 48-52 | 26.0 | 30 |
H11 | 52-56 | 25.0 | 35 |
H21 | 50-54 | 24.5 | 28 |
H10 | 48-52 | 27.5 | 32 |
These steels are carefully selected based on their ability to maintain hardness and strength at high temperatures, which is crucial for prolonged die life and efficient production in die casting operations.
Hot work tool steel applications in die casting
Hot work tool steels find extensive applications throughout various components of die casting molds:
- Die Inserts: Die inserts, which form the cavities and cores of die casting molds, require materials that can withstand the thermal and mechanical stresses of repeated heating and cooling cycles. Hot work tool steels such as H13 are commonly used due to their high hardness and thermal stability.
- Core Pins: Core pins are used to create internal features in die cast parts. These pins must endure high pressures and temperatures during the casting process, making hot work tool steels like H11 an ideal choice for their combination of toughness and wear resistance.
- Cavities and Cores: The main components of die casting molds, cavities, and cores benefit from the wear resistance and thermal fatigue resistance of hot work tool steels. Their ability to maintain dimensional stability under extreme conditions ensures precise and consistent part production.
- Extrusion Dies: In addition to die casting, hot work tool steels are also employed in extrusion dies for materials such as aluminum and magnesium alloys. The high thermal conductivity and wear resistance of these steels facilitate the efficient shaping of extruded profiles.
Advantages of Using Hot Work Tool Steels
The advantages of hot work tool steels in die casting applications include:
- High Thermal Stability: They retain their hardness and mechanical properties even at elevated temperatures, ensuring consistent performance over extended production runs.
- Wear Resistance: Hot work tool steels exhibit excellent wear resistance, reducing the need for frequent tool maintenance and replacement.
- Dimensional Stability: They minimize dimensional changes in die casting molds during thermal cycling, maintaining tight tolerances and part quality.
- Machinability: These steels are relatively easy to machine and polish, allowing for the creation of complex die shapes with smooth surfaces.
Considerations for Selection
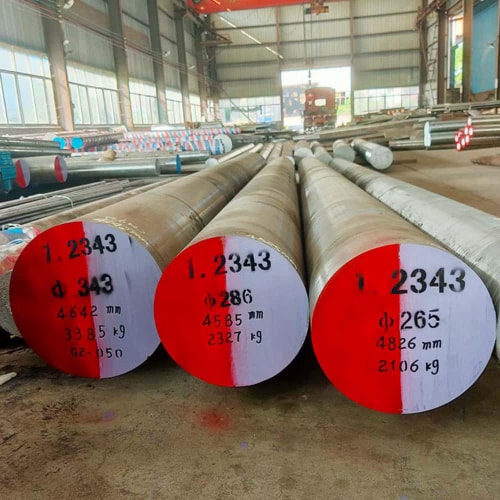
When selecting hot work tool steels for die casting applications, several factors should be considered:
- Operating Temperature: Choose steels with a high resistance to thermal softening and oxidation at the operating temperatures of the die casting process.
- Material Compatibility: Ensure compatibility with the molten metal being cast to prevent chemical reactions that could degrade the tool steel.
- Surface Finish Requirements: Select steels that can achieve the desired surface finish of the die cast parts without excessive polishing or post-processing.
Each type of hot work tool steel offers unique properties suited to specific die casting applications, requiring careful consideration to optimize tool performance and longevity.
Conclusion
Hot work tool steels are indispensable in the die casting industry, providing the durability and performance needed for the production of high-quality die cast parts. Their ability to withstand extreme temperatures and mechanical stresses ensures reliable operation of die casting molds, contributing to enhanced productivity and cost efficiency in manufacturing processes.
FAQ
Q: What are the main types of hot work tool steels used in die casting?
A: Common types include H13, H11, H21, and H10, each selected for their specific combination of hardness, toughness, and thermal conductivity.
Q: How do hot work tool steels compare to cold work tool steels in die casting applications?
A: Hot work tool steels are designed to withstand high temperatures encountered in die casting, while cold work tool steels are used for operations at lower temperatures with different mechanical properties.
Q: What are some maintenance tips for prolonging the life of hot work tool steels in die casting?
A: Regular inspection, proper lubrication, and controlled heating and cooling cycles are essential for extending the life of hot work tool steels in die casting applications.