Welcome to My Blog!
Before we dive into the content, I’d love for you to join me on my social media platforms where I share more insights, engage with the community, and post updates. Here’s how you can connect with me:
Facebook:https://www.facebook.com/profile.php?id=100087990137347
LinkedIn:https://www.linkedin.com/company/89825762/admin/dashboard/
YouTube:www.youtube.com/@carbonsteelsupply-kj9lw
TikTok:www.tiktok.com/@carbonsteelsupply
Now, let’s get started on our journey together. I hope you find the content here insightful, engaging, and valuable.
Introduction
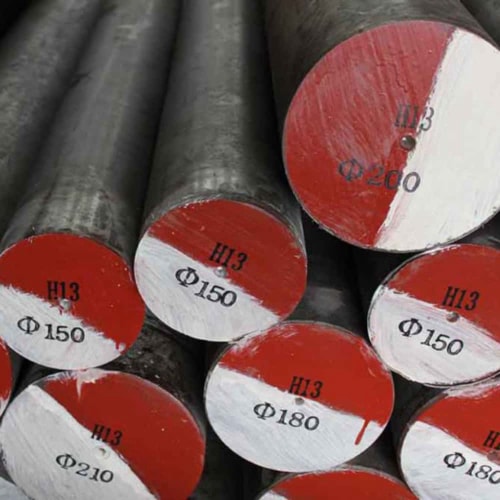
H13 tool steel is a versatile and widely used alloy in the tooling industry, especially for hot work applications. Known for its exceptional combination of hardness, toughness, and heat resistance, H13 tool steel is a crucial material in manufacturing processes like die casting, extrusion, and forging. This blog provides an in-depth look at H13 tool steel, its properties, industrial applications, and the best practices for its use and maintenance. By understanding these aspects, manufacturers and engineers can effectively leverage H13 tool steel for optimal performance.
What Is H13 Tool Steel?
H13 tool steel is a chromium-based alloy steel classified under the H-series of hot work tool steels. It is characterized by its high resistance to thermal fatigue, excellent toughness, and superior hardenability. H13 is composed of:
- Chromium (Cr): Enhances corrosion resistance and hardness.
- Molybdenum (Mo): Improves high-temperature strength and hardness.
- Vanadium (V): Increases wear resistance and toughness.
- Carbon (C): Provides the required hardness for tooling applications.
These elements contribute to the outstanding properties of H13 tool steel, making it ideal for hot work applications where thermal stability and resistance to cracking are critical.
Properties of H13 Tool Steel
H13 tool steel possesses several key properties that make it suitable for demanding industrial environments. Below are some of its main characteristics:
- High Toughness: H13 tool steel offers excellent toughness, which is essential for applications involving high mechanical stress.
- Thermal Fatigue Resistance: It can withstand repeated heating and cooling cycles, making it ideal for die-casting and extrusion dies.
- Wear Resistance: The vanadium content in H13 increases its resistance to abrasion, extending tool life.
- Good Machinability: Compared to other tool steels, H13 has good machinability, making it easier to shape and grind.
These properties make H13 tool steel a preferred choice for manufacturers seeking durability and performance under extreme temperatures.
Common Applications of H13 Tool Steel
H13 tool steel is widely used across various industries due to its ability to perform well under high-temperature and high-stress conditions. Some of its common applications include:
- Die Casting Dies: H13 tool steel is extensively used for die-casting molds due to its resistance to thermal fatigue and cracking.
- Extrusion Tools: In the extrusion industry, H13 is ideal for creating dies that can handle the stress and heat generated during metal extrusion.
- Forging Dies: H13 is also popular for hot forging dies, as it maintains its strength and hardness at high temperatures.
- Plastic Molding Tools: The material’s toughness and resistance to thermal cycling make it suitable for injection and blow molding processes.
These applications demonstrate the versatility and reliability of H13 tool steel in industrial environments where heat and stress are prevalent.
Heat Treatment of H13 Tool Steel
The heat treatment process of H13 tool steel is crucial to achieving its desired hardness, toughness, and resistance properties. Proper heat treatment ensures that the material can withstand the intense conditions encountered in its applications. The process typically includes the following stages:
- Preheating:
The steel is slowly heated to 750-800°C (1382-1472°F) to reduce the risk of thermal shock. - Austenitizing:
H13 is heated to 1010-1030°C (1850-1886°F) for a specific period based on thickness to transform its microstructure. - Quenching:
Quenching is performed using air or oil, depending on the desired outcome. This process helps achieve hardness while minimizing the risk of cracking. - Tempering:
Tempering is crucial for improving toughness while maintaining hardness. The temperature range for tempering H13 tool steel is 540-600°C (1004-1112°F).
Heat Treatment Stage | Temperature Range (°C) | Purpose |
---|---|---|
Preheating | 750-800 | Reduces thermal shock |
Austenitizing | 1010-1030 | Transforms structure to austenite |
Quenching | Air/Oil | Hardens the steel |
Tempering | 540-600 | Enhances toughness, reduces brittleness |
Properly following these steps ensures that H13 tool steel attains optimal properties for high-performance applications.
Benefits of Using H13 Tool Steel in Industrial Applications
H13 tool steel offers several advantages that make it a popular choice in various industries:
- Extended Tool Life: Due to its wear resistance and toughness, tools made from H13 steel have a longer operational lifespan, reducing replacement costs.
- Dimensional Stability: H13 maintains its shape and dimensions even under high temperatures, making it ideal for precision tooling.
- Versatility: Its properties allow it to be used in multiple applications, such as die casting, forging, and plastic molding, providing flexibility for manufacturers.
- Resistance to Cracking: The steel’s thermal fatigue resistance helps prevent cracking and failure during repeated heating and cooling cycles.
By leveraging these benefits, industries can improve productivity and minimize downtime, making H13 tool steel a cost-effective solution.
Best Practices for Machining and Maintaining H13 Tool Steel
To maximize the performance and lifespan of H13 tool steel, it is important to follow certain best practices:
- Use Appropriate Cutting Fluids: Using the right cutting fluids during machining helps manage heat and extends tool life.
- Proper Storage: Protect H13 tool steel from moisture and corrosive environments during storage to prevent surface rust and degradation.
- Regular Inspection and Maintenance: Frequent checks and maintenance of tools made from H13 ensure that any wear or damage is addressed promptly, preventing premature failure.
- Avoid Overheating During Machining: Excessive heat during machining can alter the steel’s properties, so controlling the speed and cooling is essential.
Following these best practices ensures that H13 tool steel remains reliable and effective in its applications.
Frequently Asked Questions (FAQ)
Q1: What is the typical hardness range for H13 tool steel?
A1: After proper heat treatment, H13 tool steel typically achieves a hardness range of 44-55 HRC, depending on the tempering temperature and specific application requirements.
Q2: Can H13 tool steel be used in cold work applications?
A2: While H13 is primarily designed for hot work applications due to its thermal resistance, it can also be used in cold work applications where toughness and moderate hardness are required.
Q3: How does tempering affect H13 tool steel?
A3: Tempering H13 tool steel reduces brittleness while maintaining hardness, thereby improving its toughness. This process is essential for making the steel suitable for high-stress applications.
Q4: Is H13 tool steel resistant to corrosion?
A4: H13 has moderate corrosion resistance due to its chromium content, but it is not as resistant as stainless steels. Applying a protective coating or storing it in a dry environment can help minimize corrosion.
Conclusion
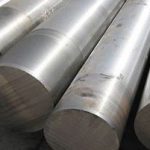
H13 tool steel is a versatile and reliable material widely used in hot work applications. Its combination of toughness, thermal fatigue resistance, and wear resistance makes it ideal for die casting, forging, and extrusion. By understanding its properties, applications, and heat treatment process, manufacturers can maximize the benefits of H13 tool steel, enhancing the longevity and performance of their tools. Following best practices for machining and maintenance further ensures that H13 tool steel delivers consistent and efficient results, making it an indispensable tool in modern manufacturing.