Introduction
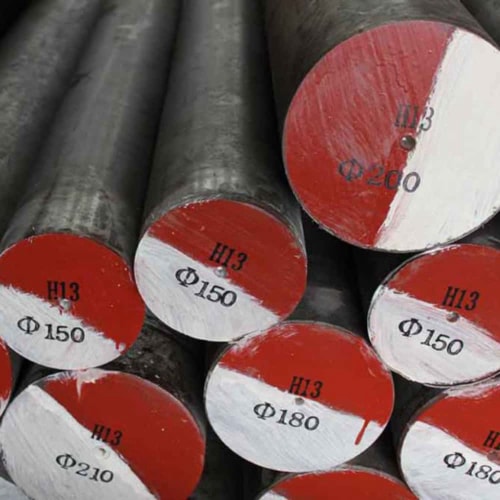
H13 steel, a chromium hot work tool steel, is a cornerstone in the manufacturing industry, renowned for its exceptional combination of hardness, toughness, and resistance to wear and heat. This unique blend of properties makes it an indispensable material for a wide range of applications, particularly in the production of molds and dies. In this comprehensive guide, we will delve deep into the intricate details of H13 tool steel, exploring its properties, applications, heat treatment processes, and factors influencing its performance.
Understanding H13 Steel
H13 steel is classified as a chromium hot work tool steel due to its high chromium content, typically ranging from 4 to 5%. This alloying element significantly contributes to the steel’s exceptional properties. Chromium forms a protective oxide layer on the steel’s surface, enhancing its corrosion resistance and oxidation resistance at elevated temperatures. Additionally, chromium solid-solution strengthens the steel’s matrix, improving its hardness and wear resistance.
Key Properties of H13 Tool Steel
- High Hardness: H13 steel can achieve remarkable levels of hardness, often exceeding Rockwell C 50. This exceptional hardness is attributed to its martensitic microstructure, which is formed during the heat treatment process. The high hardness makes H13 tool steel highly resistant to wear and abrasion, ensuring the longevity of tools and dies.
- Excellent Toughness: Despite its high hardness, H13 steel retains good toughness, enabling it to withstand impact loads without fracturing. This balance of hardness and toughness is crucial for applications that involve both cutting and forming operations.
- Heat Resistance: H13 steel exhibits excellent resistance to high temperatures, making it suitable for hot working processes such as forging, extrusion, and die casting. The chromium-rich oxide layer provides a protective barrier against oxidation and scaling at elevated temperatures.
- Good Wear Resistance: The combination of high hardness and toughness results in excellent wear resistance, enabling H13 tool steel to maintain its performance even under severe operating conditions. This is particularly important for tools and dies that are subjected to continuous contact with high-temperature, high-pressure materials.
- Dimensional Stability: H13 steel exhibits good dimensional stability, making it suitable for precision tooling applications. This property ensures that the tools and dies maintain their precise dimensions and tolerances throughout their service life, leading to improved product quality and reduced downtime.
Applications of H13 Steel
The unique combination of properties possessed by H13 tool steel makes it a versatile material with a wide range of applications across various industries. Some of the most common applications include:
- Mold and Die Manufacturing: H13 tool steel is extensively used in the production of injection molds, extrusion dies, and forging dies. Its high hardness, toughness, and heat resistance enable it to withstand the demanding conditions of these processes, ensuring the production of high-quality components.
- Plastic Molding: H13 tool steel is a preferred choice for plastic injection molds, especially for producing complex shapes and intricate details. Its excellent wear resistance and dimensional stability contribute to the production of precise and durable plastic parts.
- Metal Forming: H13 tool steel is used in metal forming tools such as stamping dies, drawing dies, and bending dies. Its high hardness and toughness allow it to withstand the high forces and pressures involved in these processes.
- Aerospace: H13 tool steel finds applications in the aerospace industry for manufacturing components that require high strength, heat resistance, and wear resistance. These components include turbine blades, engine components, and structural parts.
- Automotive: H13 tool steel is used in the automotive industry for producing engine components, transmission parts, and other critical components that require high performance and durability.
Heat Treatment of H13 Steel
The heat treatment process plays a crucial role in achieving the desired properties of H13 steel. The most common heat treatment processes for H13 steel include:
- Austenitizing: This process involves heating the steel to a temperature above its austenitizing temperature, typically between 1850°F and 1950°F (1010°C and 1066°C), and holding it at this temperature for a sufficient period to allow the formation of austenite, a single-phase solid solution.
- Quenching: After austenitizing, the steel is rapidly cooled, typically in oil or water, to transform the austenite into a martensitic microstructure. Martensite is a hard and brittle phase that imparts high hardness and wear resistance to the steel.
- Tempering: Tempering is a heat treatment process that involves reheating the quenched steel to a temperature below its austenitizing temperature, typically between 400°F and 1000°F (204°C and 538°C), and holding it at this temperature for a specific period. Tempering reduces the brittleness of the martensite and improves its toughness.
Typical Heat Treatment Cycles for H13 Steel
Heat Treatment Stage | Temperature (°F) | Time (hours) | Cooling Rate |
---|---|---|---|
Austenitizing | 1850-1950 | 1-2 | Rapid quench in oil or water |
Tempering | 400-1000 | 1-24 | Furnace cool |
Factors Affecting the Performance of H13 Steel
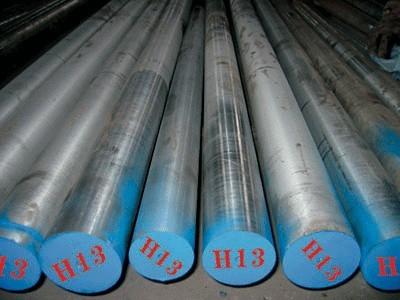
Several factors can influence the performance of H13 steel, including:
- Chemical Composition: The chemical composition of H13 tool steel, particularly the content of alloying elements such as chromium, vanadium, and molybdenum, significantly affects its properties. Variations in the chemical composition can lead to differences in hardness, toughness, and wear resistance.
- Heat Treatment: The specific heat treatment cycle, including the austenitizing temperature, quenching medium, and tempering temperature and time, plays a crucial role in determining the final properties of the steel.
- Cooling Rate: The cooling rate during quenching affects the microstructure and hardness of the steel. A rapid cooling rate promotes the formation of martensite, resulting in higher hardness.
- Machinability: H13 steel is generally difficult to machine due to its high hardness. However, proper machining techniques, such as using carbide cutting tools and appropriate cutting parameters, can improve machinability.
Conclusion
H13 steel is a high-performance tool steel that offers an exceptional combination of hardness, toughness, and heat resistance. Its versatility and durability make it an invaluable material for a wide range of applications, particularly in the manufacturing industry. By understanding the properties, applications, and heat treatment processes of H13 steel, engineers and manufacturers can optimize its performance and select the appropriate grade for specific applications.
FAQ
What is the difference between H13 and P20 steel?
While both H13 and P20 are tool steels, they have distinct properties and applications. H13 steel is generally harder and more wear-resistant, making it suitable for hot work applications such as forging and extrusion. P20 steel, on the other hand, is more ductile and machinable, making it suitable for cold work applications such as stamping and drawing.
Can H13 steel be welded?
Yes, H13 steel can be welded using appropriate welding techniques and filler metals. However, welding can affect the properties of the steel in the heat-affected zone, reducing its hardness and toughness.
How is H13 steel recycled?
H13 steel can be recycled through the same processes as other steel alloys. It is typically melted down and re-alloyed to produce new steel products.