Welcome to My Blog! 🌟
Before we dive into the content, I’d love for you to join me on my social media platforms. It’s where I share more insights, engage with our vibrant community, and post regular updates. Here’s how you can stay connected:
📘 Facebook: Connect with me on Facebook
Now, let’s embark on this journey together. I hope you find the content here insightful, engaging, and most importantly, valuable. Let’s explore, learn, and grow together! 🚀
Table of Contents
Introduction
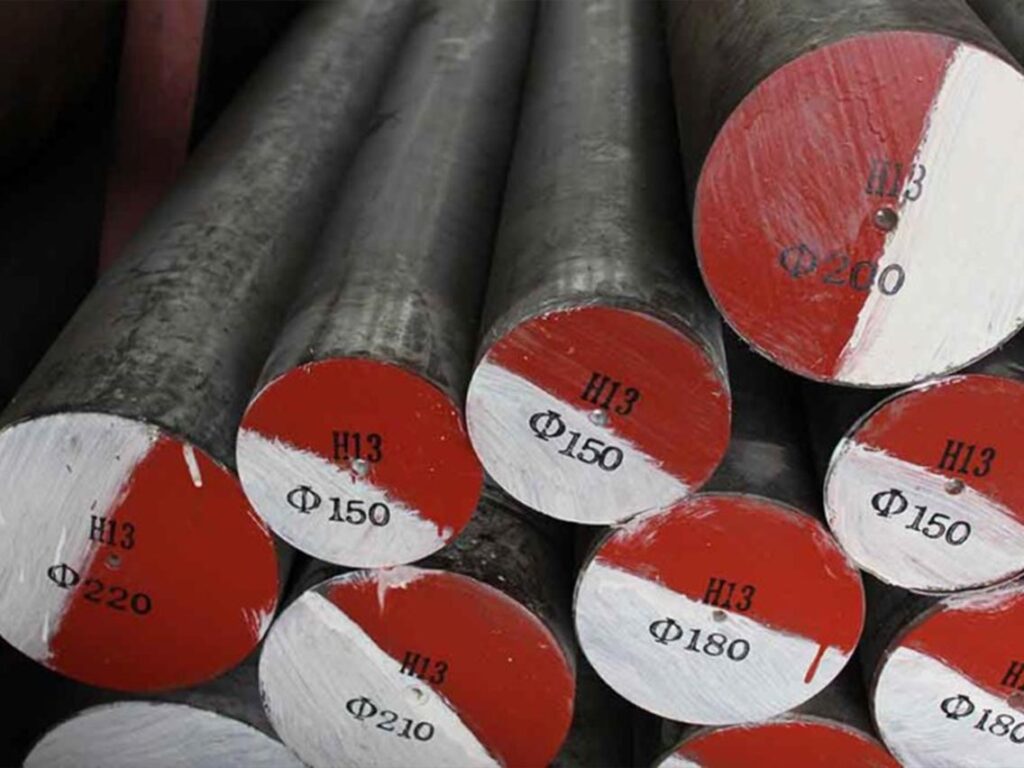
H13 mold steel, a premium tool steel renowned for its high toughness, wear resistance, and thermal stability, is widely used in industries such as automotive, aerospace, and plastic molding. However, subpar quality or improper testing can lead to catastrophic failures—from mold breakdowns that halt production lines to safety hazards in end products. This blog explores three indispensable tests to ensure H13 mold steel meets rigorous standards, helping manufacturers avoid costly disasters and maintain operational reliability.
Hardness Testing: Unveiling the Core Strength of H13 Mold Steel
Why Hardness is Non-Negotiable for H13 Mold Steel
Hardness is a fundamental indicator of H13 mold steel’s ability to resist wear, deformation, and impact. In mold manufacturing, inconsistent hardness can cause uneven material distribution, leading to premature failure or reduced product precision. For H13 steel, which is often heat-treated to optimize its mechanical properties, accurate hardness testing is the first line of defense against performance inconsistencies.
Common Hardness Testing Methods for H13 Mold Steel
- Rockwell Hardness Test (HRC): The most widely used method for H13 steel, measuring indentation depth under specific loads. Ideal for heat-treated H13 with a target hardness range of 48-52 HRC.
- Brinell Hardness Test (HB): Suitable for as-cast or annealed H13, providing a broader indentation for more uniform readings.
- Vickers Hardness Test (HV): Offers high precision for thin sections or surface coatings, critical for complex mold designs.
Industry Standards and Acceptance Criteria
Test Method | Standard Reference | Target Range for H13 | Tolerance |
---|---|---|---|
Rockwell HRC | ASTM E18 | 48-52 HRC | ±1.5 HRC |
Brinell HB | ASTM E10 | 200-250 HB | ±10 HB |
Vickers HV | ASTM E92 | 470-520 HV | ±15 HV |
Pitfalls to Avoid in Hardness Testing
- Inconsistent heat treatment prior to testing, which can skew results.
- Improper surface preparation, such as rust or oxidation, affecting indentation accuracy.
- Using incorrect indenter types or load values for the specific H13 application.
Impact Toughness Testing: Ensuring H13 Mold Steel Resists Sudden Stress
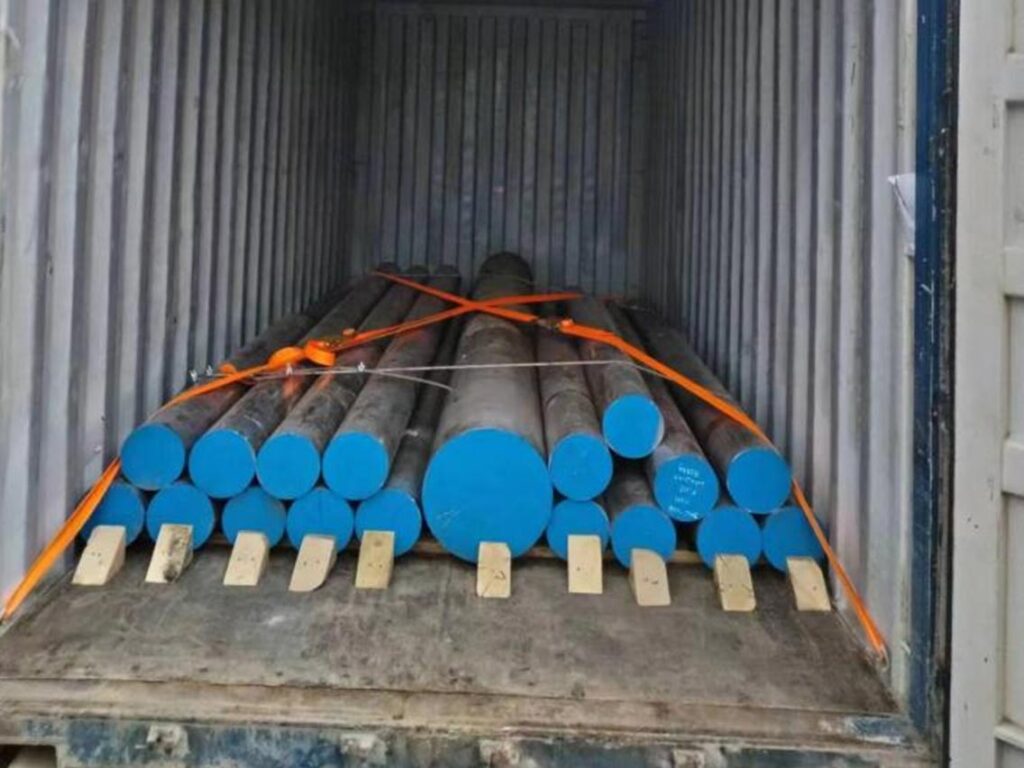
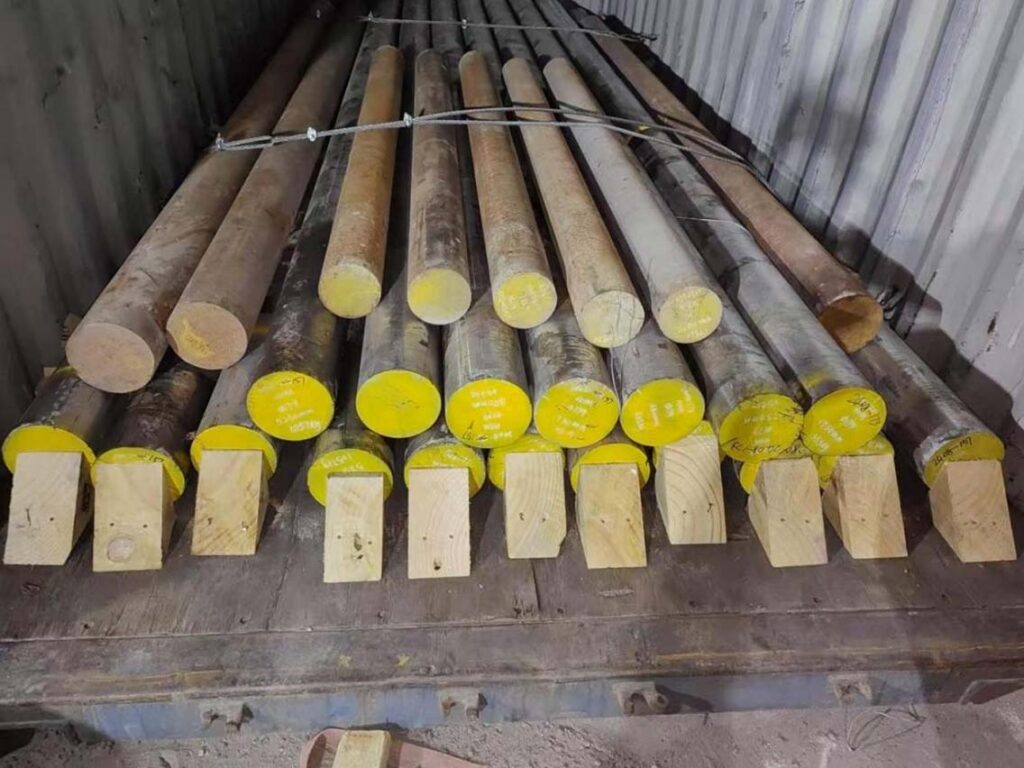
The Link Between Impact Toughness and Mold Longevity
In the dynamic realm of manufacturing, H13 mold steel serves as a workhorse, enduring intense and often unpredictable forces during casting and molding processes. Impact toughness, defined as the amount of energy a material can absorb before fracturing, is not merely a technical specification—it’s a linchpin for maintaining operational continuity. When H13 mold steel lacks sufficient toughness, it becomes vulnerable to catastrophic breakage, especially under cyclic loading conditions common in high-volume production lines.
Imagine a die-casting operation churning out hundreds of automotive components daily. Each cycle subjects the H13 mold to rapid temperature fluctuations and mechanical stress. Without adequate impact toughness, micro-cracks can form and propagate over time, leading to mold failure. This not only halts production but also triggers a domino effect of costs: from emergency mold repairs and replacement to potential delays in meeting customer deadlines, which can damage long-term business relationships.
Charpy and Izod Tests: Benchmarks for H13’s Impact Resistance
- Charpy V-Notch Test: Involves striking a notched H13 specimen with a pendulum, measuring the energy absorbed at fracture. Recommended for H13 steel at room temperature, with a minimum acceptable value of 20-25 Joules.
- Izod Impact Test: Similar to Charpy but uses a vertical specimen, suitable for evaluating notch sensitivity in H13 components with complex geometries.
Factors Influencing Impact Toughness Results
- Heat treatment parameters, especially tempering temperature—over-tempering can reduce toughness, while under-tempering may increase brittleness.
- Microstructural defects, such as carbide segregation or excessive grain growth, which weaken H13’s impact resistance.
- Testing temperature: H13’s toughness may decrease in sub-zero environments, requiring specific cold-weather evaluations for certain applications.
Real-World Consequences of Neglecting Impact Testing
The consequences of overlooking impact testing can be severe, as illustrated by a 2023 case study. A mid-sized plastic molding company, aiming to cut costs, skipped impact testing on newly procured H13 molds. Within six months, they experienced 12 mold failures, resulting in $350,000 in direct losses. These losses included emergency mold repairs, replacement costs, and production downtime.
Post-mortem analysis revealed that improper quenching during the steel’s heat treatment process had led to insufficient impact toughness. The rapid cooling rate during quenching had created excessive residual stresses and a brittle microstructure, making the molds prone to cracking under normal operating loads. This incident not only highlighted the financial toll of neglecting impact testing but also the importance of a holistic quality control approach that encompasses material testing, heat treatment monitoring, and process optimization.
Moreover, the ripple effects extended beyond immediate financial losses. The company’s reputation suffered as missed delivery deadlines frustrated key clients. Rebuilding trust required additional investments in quality assurance and customer service, underscoring the far-reaching implications of compromising on impact testing for H13 mold steel.
Microstructural Analysis: The Key to H13 Mold Steel Consistency
Why Microstructure Dictates H13’s Performance
The microstructure of H13 mold steel—comprising carbides, martensite, and retained austenite—directly influences its mechanical properties. Uniform carbide distribution, fine grain size, and minimal defects are essential for consistent hardness, toughness, and wear resistance. Microstructural analysis helps identify manufacturing flaws early in the process.
Techniques for Evaluating H13’s Microstructure
- Optical Microscopy: Standard method for examining grain size, carbide distribution, and phase composition. H13 should exhibit fine, evenly dispersed carbides in a martensitic matrix.
- Scanning Electron Microscopy (SEM): Provides higher resolution to detect nanoscale defects, such as carbide clustering or intergranular corrosion.
- X-Ray Diffraction (XRD): Analyzes phase composition, ensuring retained austenite levels in heat-treated H13 are within the optimal range (typically <5%).
Microstructural Defects and Their Impact on H13
Defect Type | Cause | Effect on H13 Performance |
---|---|---|
Carbide banding | Inconsistent casting | Reduced anisotropy, increased wear susceptibility |
Coarse grain size | Excessive austenitizing temperature | Lower toughness and fatigue strength |
Retained austenite excess | Inadequate tempering | Dimensional instability and reduced hardness |
Quality Control Steps for Microstructural Integrity
- Regular sampling of H13 billets during production to verify microstructure.
- Implementing strict heat treatment protocols to avoid carbide coarsening.
- Collaborating with steel suppliers to ensure raw material consistency through microstructural certification.
Applications: How Quality-Tested H13 Mold Steel Enhances Industry Performance
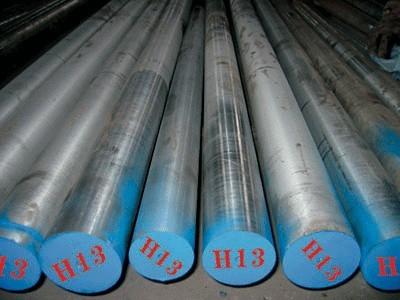
Automotive Molding: Precision and Durability
In automotive die casting, H13 molds must withstand high temperatures and repeated impacts. Quality-tested H13 steel reduces the need for frequent mold replacements, enabling manufacturers to produce up to 50,000 parts per mold without degradation—significantly improving production efficiency.
Aerospace Tooling: Safety-Driven Standards
Aerospace components require H13 tools with impeccable quality to avoid failures that could compromise flight safety. Rigorous testing ensures H13 molds used in turbine part manufacturing meet ASTM A681 standards, minimizing the risk of material defects in critical components.
Plastic Injection Molding: Surface Finish and Repeatability
For high-precision plastic parts (e.g., medical devices), H13 molds must maintain surface finish and dimensional accuracy. Quality-tested H13 steel reduces wear-related defects, allowing consistent production of parts with Ra surface roughness below 0.8μm for over 100,000 cycles.
FAQ
What is the ideal hardness range for H13 mold steel?
H13 steel is typically heat-treated to 48-52 HRC for most mold applications. However, specific industries may adjust this range: e.g., plastic molding often prefers 50-52 HRC for wear resistance, while die casting may opt for 48-50 HRC to balance toughness and hardness.
Can H13 mold steel be retested if initial results fail?
Yes, but retesting requires identifying the root cause of failure first. For example, if hardness is insufficient, re-tempering the H13 component under controlled conditions may resolve the issue. However, repeated heat treatment can degrade microstructure, so retesting is limited to 1-2 cycles.
How often should H13 molds be tested for quality?
Routine testing depends on usage:
- New H13 molds: 100% testing before first use.
- In-production molds: Periodic testing every 5,000-10,000 cycles, or whenever performance degradation is suspected.
- Critical applications (e.g., aerospace): Non-destructive testing (NDT) after each production batch.
Are there alternative tests for H13 mold steel quality?
Yes, supplementary tests include:
- Tensile testing to measure yield and ultimate tensile strength.
- Fatigue testing to evaluate resistance to cyclic loading.
- Corrosion testing for H13 used in harsh environments.
These tests complement the core three (hardness, impact, microstructure) for comprehensive quality assurance.
Conclusion
Investing in rigorous hardness testing, impact toughness evaluation, and microstructural analysis is non-negotiable for H13 mold steel users. By implementing these three key tests, manufacturers can prevent catastrophic failures, reduce maintenance costs, and ensure consistent product quality. Remember: the cost of testing pales in comparison to the losses incurred from a failed H13 mold—whether in production downtime, replacement expenses, or reputational damage. Make quality testing a cornerstone of your H13 mold steel strategy, and avoid the disasters that come with oversight.
To recap, the three tests form a trifecta of quality assurance:
- Hardness testing confirms H13’s wear resistance.
- Impact toughness testing prevents sudden failure under stress.
- Microstructural analysis ensures material consistency from billet to finished mold.
By integrating these into your quality control protocol, you’ll maximize the lifespan and reliability of H13 mold steel, driving operational success in any industry.