Hot work tool steel is renowned for its exceptional heat resistance, making it invaluable in applications subjected to high temperatures and mechanical stress. A crucial aspect of hot work tool steel’s performance is its hardenability—the ability to attain and maintain a desired hardness through heat treatment. Understanding the factors that influence the hardenability of hot work tool steel is essential for optimizing its properties for specific industrial applications. In this comprehensive article, we will explore the science behind hardenability, the key factors that affect it, and how engineers and metallurgists can manipulate these factors to achieve desired outcomes in hot work tool steel.
1. Introduction to Hardenability in Hot Work Tool Steel
1.1 What is Hardenability?
Hardenability is a critical material property that determines the depth and uniformity of hardness achievable in a steel alloy when subjected to a specific heat treatment process, typically involving heating and quenching. In the context of hot work tool steel, hardenability influences the material’s ability to maintain its hardness, strength, and wear resistance under high-temperature conditions.
1.2 Importance of Hardenability in Hot Work Tool Steel
In industries where hot work tool steel is extensively used, such as die casting, forging, and extrusion, the ability to achieve and control hardness is paramount. Hardenability directly impacts the performance and longevity of tools and components subjected to extreme temperatures and mechanical stresses.
1.3 Role of Heat Treatment
Heat treatment is a fundamental process for optimizing the hardenability of hot work tool steel. It involves controlled heating and cooling to achieve the desired microstructure and mechanical properties. Understanding the factors that influence hardenability is essential for tailoring heat treatment processes to specific applications.
2. Factors Affecting Hardenability
2.1 Alloying Elements
The composition of hot work tool steel, including alloying elements such as chromium, tungsten, molybdenum, and vanadium, significantly influences hardenability. These elements form carbides and contribute to the steel’s ability to undergo phase transformations during heat treatment.
2.2 Carbon Content
The carbon content in hot work tool steel plays a crucial role in hardenability. Higher carbon content can lead to increased hardness, but excessive carbon can also result in brittleness. Achieving the right balance is essential for optimal hardenability.
2.3 Grain Size
The grain size of the steel’s microstructure affects how it responds to heat treatment. Finer grains generally result in improved hardenability, as they allow for more uniform and controlled phase transformations during quenching.
2.4 Cooling Rate
The rate at which hot work tool steel is cooled during quenching is a critical factor in hardenability. Faster cooling rates can lead to greater hardness, but overly rapid cooling can also introduce stress and the risk of cracking.
2.5 Heat Treatment Techniques
The specific heat treatment techniques employed, including heating temperature, soak time, and quenching media, can be tailored to manipulate hardenability. Precise control of these parameters is essential for achieving desired hardness profiles.
3. The Science of Hardenability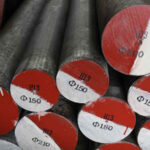
3.1 Phase Transformations
Hardenability is closely related to the phase transformations that occur during heat treatment. The steel undergoes changes in its microstructure, transitioning from austenite to different phases like ferrite, pearlite, and martensite, depending on the cooling rate and alloy composition.
3.2 Formation of Martensite
Martensite, a supersaturated solid solution, is a key phase in hardened steel. Its formation is critical for achieving high hardness and strength. The cooling rate determines the extent of martensite formation.
3.3 Impact on Mechanical Properties
Hardenability significantly influences the mechanical properties of hot work tool steel, including hardness, strength, toughness, and wear resistance. Controlling these properties allows engineers to tailor the material for specific applications.
4. Manipulating Hardenability for Specific Applications
4.1 Tailoring Hot Work Tool Steel for Different Industries
Understanding the hardenability of hot work tool steel enables manufacturers to customize the material for various industrial applications, including die casting, forging, extrusion, and plastic molding.
4.2 Achieving Optimal Hardness
Optimizing the hardness of hot work tool steel is essential for ensuring the longevity and performance of tools and components in high-temperature environments. Proper heat treatment processes and alloy selection are key factors.
4.3 Challenges in Manipulating Hardenability
While manipulating hardenability offers numerous benefits, it also presents challenges, such as achieving uniform hardness across complex shapes and mitigating the risk of cracking during quenching. Engineers must carefully address these issues in their designs and processes.
5. Hardenability Testing Methods
5.1 Jominy End-Quench Test
The Jominy end-quench test is a common method for evaluating hardenability. It involves heating a standardized test specimen, followed by quenching one end. The resulting hardness profile provides insights into the steel’s hardenability.