Introduction
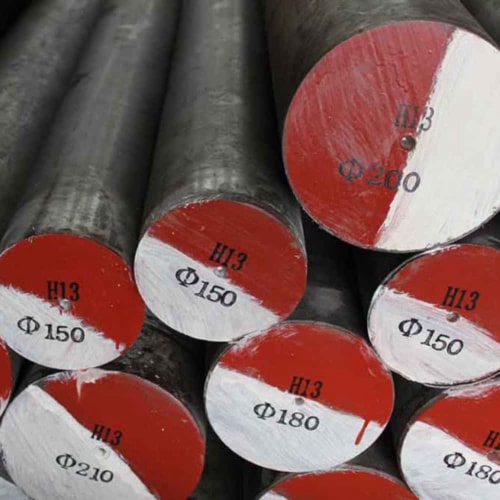
H13 tool steel is renowned for its exceptional hardness and thermal conductivity, making it a preferred material in high-performance applications such as die casting and forging. Achieving and maintaining optimal H13 tool steel hardness levels is crucial for ensuring its durability and effectiveness in these demanding environments. This blog explores in detail the various factors that influence the hardness of H13 tool steel, emphasizing how these factors can be controlled and optimized to enhance material properties.
Understanding H13 Tool Steel Hardness
To comprehend the significance of H13 tool steel hardness, it is essential to understand its impact on mechanical properties. Hardness refers to a material’s ability to resist indentation, scratching, or deformation under load. In the context of H13 steel, high hardness translates to improved wear resistance, toughness, and the ability to maintain sharp cutting edges or mold details at elevated temperatures, which are critical for its role in tooling and forming applications.
Factors Influencing H13 Tool Steel Hardness Levels
- Chemical Composition and Hardenability: The chemical composition of H13 steel, including carbon (0.32% to 0.45%), chromium (4.75% to 5.50%), and molybdenum (1.10% to 1.75%), significantly influences its hardness. Higher carbon content promotes the formation of carbides, increasing overall hardness. Chromium and molybdenum contribute to the steel’s hardenability, ensuring uniform hardness throughout the material.
- Heat Treatment: Heat treatment processes such as annealing, quenching, and tempering play a crucial role in determining the final hardness of H13 tool steel. Proper quenching transforms the microstructure to martensite, known for its high hardness, while tempering at specific temperatures enhances toughness without compromising hardness.
- Processing Conditions: Manufacturing processes, including forging and casting, impact the microstructure and subsequent hardness of H13 steel. Control over cooling rates during solidification and heat treatment stages is essential for achieving desired hardness levels across different sections of the material.
- Surface Finish and Polishing: Surface quality influences perceived and actual hardness of H13 tool steel. A smooth, defect-free surface reduces stress concentrations and enhances the material’s resistance to wear and deformation, thereby improving overall hardness.
- Environmental Factors: Operating conditions such as temperature variations and exposure to corrosive environments can alter the microstructure and mechanical properties, including hardness, of H13 steel over time. Understanding these factors is crucial for predicting and maintaining hardness levels in practical applications.
Experimental Data and Case Studies
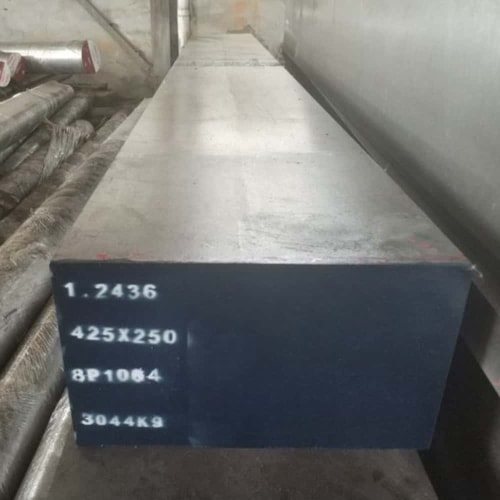
To illustrate the impact of these factors on H13 tool steel hardness, consider the following experimental findings:
Parameter | Impact on H13 Tool Steel Hardness |
---|---|
Carbon Content | Higher carbon content increases overall hardness |
Heat Treatment | Proper quenching and tempering enhance hardness and toughness |
Surface Finish | Smooth finishes correlate with improved wear resistance |
Alloying Elements | Chromium and molybdenum enhance hardenability and hardness |
These findings underscore the importance of precise control over chemical composition, heat treatment processes, and manufacturing conditions to achieve optimal H13 tool steel hardness.
Conclusion
Optimizing H13 tool steel hardness is critical for maximizing its performance and longevity in hot work applications. By understanding and controlling factors such as chemical composition, heat treatment, processing conditions, surface finish, and environmental influences, engineers and manufacturers can ensure that H13 steel meets stringent hardness requirements while maintaining superior mechanical properties.
FAQ
Q: How does carbon content affect H13 tool steel hardness?
A: Higher carbon content increases the formation of carbides, enhancing overall hardness and wear resistance in H13 steel.
Q: What role does heat treatment play in achieving high hardness in H13 steel?
A: Heat treatment processes like quenching and tempering are essential for transforming the microstructure of H13 steel to achieve martensitic phases, crucial for high hardness and toughness.
Q: How can surface finish impact H13 tool steel hardness?
A: A smooth surface finish minimizes stress concentrations and improves hardness and resistance to wear and deformation in H13 tool steel.