Introduction
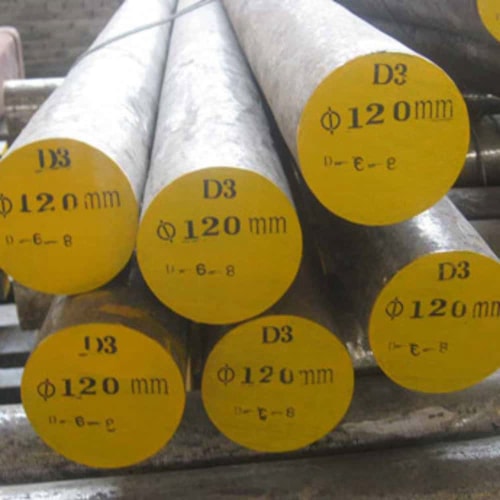
D3 tool steel stands as a testament to the engineering marvels of modern metallurgy. Its remarkable properties make it a prime choice for a wide array of industrial applications. In this blog post, we delve into the depths of D3 tool steel, exploring its composition, characteristics, applications, and much more.
Understanding D3 Tool Steel: Composition and Properties
D3 tool steel, also recognized as AISI D3, stands out as a high-performance cold-work tool steel renowned for its exceptional combination of properties. Its composition is carefully engineered to yield outstanding wear resistance, hardness, and toughness, essential qualities for enduring the rigorous demands of tooling applications.
Comprising approximately 2.1% carbon and 12% chromium, D3 steel forms a solid foundation for its remarkable attributes. Carbon contributes to its hardness and strength, while chromium enhances its corrosion resistance and wear properties. Moreover, D3 steel may contain varying proportions of other alloying elements like vanadium and molybdenum. These additional elements serve specific purposes, further elevating the steel’s performance characteristics.
Vanadium, for instance, refines the grain structure of the steel, promoting finer microstructures that enhance toughness and resistance to fatigue failure. Meanwhile, molybdenum contributes to hardenability, facilitating the formation of a uniform and deep-hardened layer during heat treatment. This combination of alloying elements synergistically enhances the overall properties of D3 steel, making it an indispensable material across a spectrum of tooling applications.
In the tooling industry, where precision, durability, and reliability are paramount, D3 steel shines as a preferred choice. Whether it’s for manufacturing punches, dies, industrial knives, or forming tools, D3 steel offers unparalleled performance, ensuring efficient operation and prolonged service life. Its ability to withstand abrasive wear, maintain sharp edges, and endure high-impact loads makes it indispensable in applications ranging from metal stamping to plastic molding.
Applications of D3 Tool Steel
The versatility of D3 tool steel extends across numerous applications, owing to its excellent combination of hardness, wear resistance, and machinability. Some common applications include:
- Cold Work Tooling: D3 steel finds extensive use in manufacturing cold work tooling, such as punches, dies, and cutting tools. Its high hardness and wear resistance make it ideal for shaping and forming operations at low temperatures.
- Industrial Knives: Due to its exceptional edge retention and toughness, D3 steel is a preferred choice for industrial knives used in cutting and shearing applications. From paper and plastic industries to food processing, D3 steel ensures precise and durable cutting performance.
- Blanking and Forming Dies: The superior wear resistance of D3 steel makes it an excellent candidate for blanking and forming dies in the manufacturing of intricate metal components. Its ability to maintain dimensional stability under high-stress conditions enhances the efficiency and longevity of the dies.
Advantages of D3 Tool Steel
The advantages of D3 tool steel are multifaceted, making it a standout material in the realm of tooling and machining. Some key benefits include:
- High Wear Resistance: D3 steel exhibits exceptional wear resistance, ensuring prolonged tool life even under demanding operating conditions.
- Good Machinability: Despite its high hardness, D3 steel offers good machinability, allowing for efficient shaping and finishing processes.
- Excellent Dimensional Stability: Components made from D3 steel maintain precise dimensions even under thermal cycling and heavy loads, minimizing the need for rework or adjustments.
Composition of D3 Tool Steel
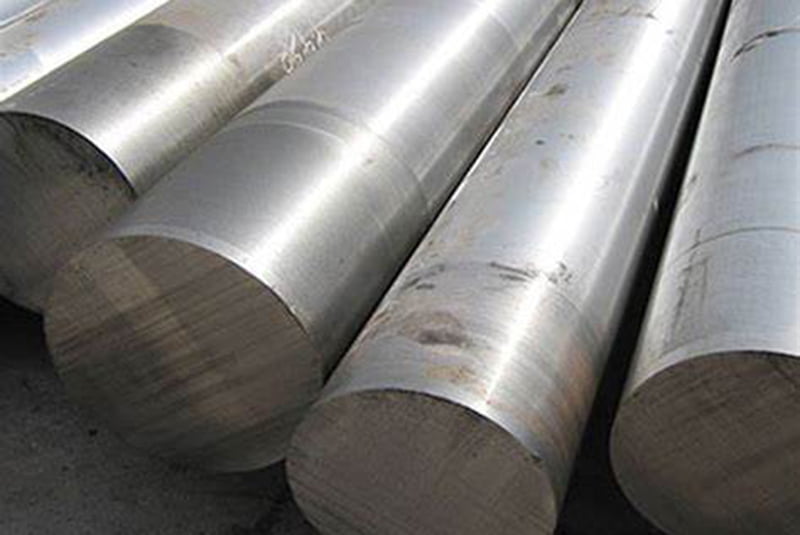
Element | Percentage (%) |
---|---|
Carbon | 2.1 |
Chromium | 12 |
Vanadium | 1.0 (optional) |
Molybdenum | 1.0 (optional) |
Conclusion
In conclusion, D3 tool steel emerges as a formidable contender in the realm of tooling materials, offering a unique blend of hardness, wear resistance, and machinability. Its versatility and reliability make it a preferred choice for a diverse range of industrial applications, from cold work tooling to precision machining. As technology continues to advance, D3 steel stands poised to remain at the forefront of innovation in the manufacturing sector.
FAQ
Q: Is D3 tool steel suitable for high-temperature applications?
A: While D3 tool steel excels in cold work applications, it is not recommended for use in high-temperature environments due to its relatively low heat resistance.
Q: How does D3 tool steel compare to other tool steels such as D2 and A2?
A: D3 tool steel offers higher wear resistance compared to D2 and A2 steels, making it suitable for applications requiring prolonged tool life under abrasive conditions.
Q: Can D3 tool steel be heat-treated for further enhancement of its properties?
A: Yes, D3 tool steel can undergo heat treatment processes such as annealing, hardening, and tempering to achieve desired mechanical properties and performance characteristics.