Introduction
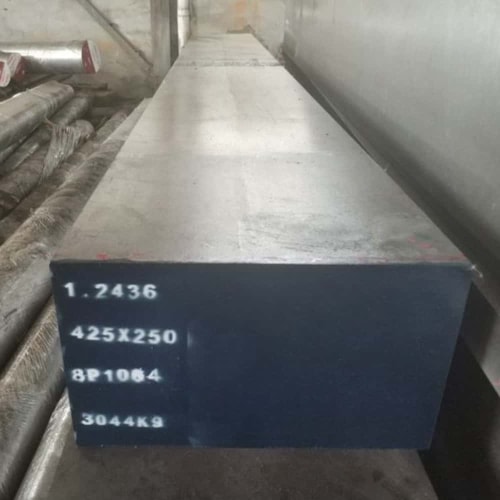
Cold work tool steel is a versatile material known for its durability and resilience in various industrial applications. In this blog, we’ll delve into the diverse applications and advantages of cold work steel, exploring its properties and how they contribute to its effectiveness in different contexts.
Understanding Cold Work Tool Steel
Cold work tool steel is a type of high-carbon steel designed to withstand repeated stress and wear at low temperatures. Its composition typically includes elements such as chromium, tungsten, and vanadium, which enhance its hardness and toughness. This combination of properties makes it ideal for applications where materials need to maintain their strength and shape under pressure, such as in cutting, forming, and stamping operations.
Applications of Cold Work Tool Steel
Cutting Tools
Cold work tool steel is widely used in the manufacturing of cutting tools such as knives, drills, and saw blades. Its high hardness and wear resistance allow these tools to maintain their sharpness and precision over extended periods, increasing productivity and reducing downtime.
Molds and Dies
In the plastic and metal forming industries, cold work steel is essential for producing molds and dies. Its ability to withstand high pressure and repeated impacts ensures the longevity and accuracy of these critical components, enabling the mass production of various products with consistent quality.
Blanking and Punching
Cold work steel plays a crucial role in blanking and punching operations, where sheets of metal are cut or shaped into desired forms. Its toughness and edge retention allow for clean cuts and precise shapes, even when working with challenging materials such as stainless steel or hardened alloys.
Woodworking Tools
Woodworking tools like chisels, planes, and gouges rely on cold work tool steel for their cutting edges. The material’s hardness and edge retention make it well-suited for shaping and carving wood with precision and control, facilitating the creation of intricate designs and smooth finishes.
Cold Forming
In the automotive and aerospace industries, cold work steel is used in cold forming processes to shape metal components without heating them to high temperatures. This method reduces energy consumption and material waste while maintaining the mechanical properties of the finished parts, making it an efficient and cost-effective manufacturing solution.
Advantages of Cold Work Tool Steel
- High Hardness: Cold work tool steel exhibits exceptional hardness, allowing it to resist deformation and wear even under heavy loads.
- Toughness: Despite its hardness, cold work tool steel retains sufficient toughness to withstand impacts and shocks without fracturing or chipping.
- Wear Resistance: The alloying elements in cold work tool steel enhance its wear resistance, prolonging the lifespan of tools and components in demanding applications.
- Edge Retention: Tools made from cold work tool steel maintain sharp edges for extended periods, reducing the need for frequent sharpening or replacement.
- Dimensional Stability: Cold work steel maintains dimensional stability even under fluctuating temperatures, ensuring consistent performance in diverse operating conditions.
Cold Work Tool Steel Comparison Table
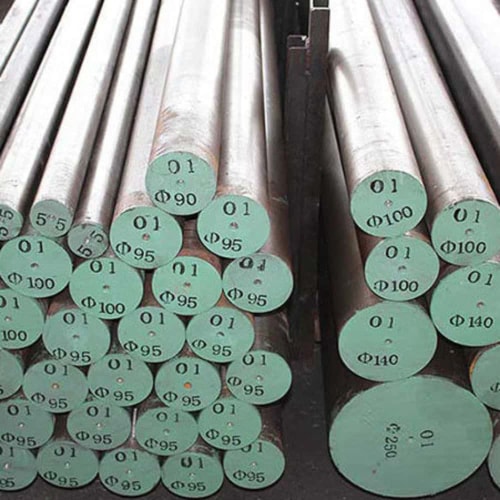
Property | Cold Work Tool Steel | High-Speed Steel | Hot Work Tool Steel |
---|---|---|---|
Hardness (HRC) | High | Moderate to High | Moderate to High |
Toughness | High | Low to Moderate | Moderate |
Wear Resistance | High | Moderate | Moderate |
Heat Resistance | Low | Moderate | High |
Edge Retention | Excellent | Moderate | Moderate |
Cost | Moderate to High | Moderate | Moderate to High |
Conclusion
Cold work tool steel offers a wide range of applications and advantages, making it indispensable in various industries where durability, precision, and performance are paramount. Its combination of high hardness, toughness, and wear resistance ensures reliable performance in cutting, forming, and shaping operations, contributing to increased efficiency and productivity.
FAQ
Q: What are the primary alloying elements in cold work tool steel?
A: Chromium, tungsten, and vanadium are commonly used alloying elements in cold work steel, contributing to its hardness and toughness.
Q: How does cold work tool steel differ from other types of tool steel?
A: Cold work steel is specifically designed to withstand stress and wear at low temperatures, making it suitable for applications where materials need to maintain their strength and shape without excessive heating.
Q: What factors should be considered when selecting cold work tool steel for a specific application?
A: Factors such as hardness, toughness, wear resistance, heat resistance, and cost should be evaluated to ensure that the chosen material meets the requirements of the application while providing optimal performance and durability.