Introduction
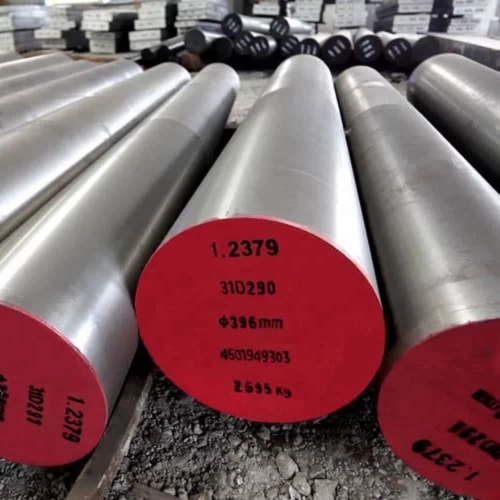
Cold work tool steel is a versatile material that finds applications across various industries due to its exceptional properties. From manufacturing to automotive and beyond, its durability, hardness, and resistance to wear make it indispensable. In this blog post, we delve into the diverse applications and advantages of cold work tool steel, shedding light on its importance in modern engineering.
Understanding Cold Work Tool Steel
Cold work tool steel is a type of high-carbon steel that is specifically designed to withstand mechanical stress at low temperatures. It contains elements such as chromium, tungsten, and vanadium, which contribute to its hardness and wear resistance. Unlike hot work tool steel, which is designed for higher temperature applications, cold work tool steel retains its properties even in environments where heat is not a factor.
Applications Across Industries
Cold work tool steel finds widespread use in various industries, thanks to its unique combination of properties. Here are some key applications:
- Manufacturing Sector: In the manufacturing industry, cold work tool steel is used for producing dies, punches, and cutting tools. Its high hardness and abrasion resistance ensure longevity and precision in machining processes.
- Automotive Industry: Cold work tool steel plays a vital role in the automotive sector for manufacturing components such as molds for plastic injection, stamping dies, and cutting tools for metal forming processes.
- Construction and Infrastructure: In construction, cold work tool steel is utilized for producing tools and equipment for concrete forming, such as molds and formwork systems. Its toughness and durability are crucial for withstanding the rigors of construction environments.
- Aerospace and Defense: In aerospace and defense applications, cold work tool steel is employed in the production of critical components like aircraft structural parts, missile components, and precision instruments. Its strength and reliability are paramount for ensuring safety and performance in demanding conditions.
- Medical Devices: Cold work tool steel is also used in the medical field for manufacturing surgical instruments and implants. Its biocompatibility, corrosion resistance, and ease of sterilization make it suitable for medical applications where precision and hygiene are essential.
Advantages of Cold Work Tool Steel
The advantages of cold work tool steel stem from its unique properties, which include:
- High Hardness: Cold work tool steel exhibits excellent hardness, making it suitable for applications requiring wear resistance and dimensional stability.
- Good Toughness: Despite its high hardness, cold work tool steel maintains good toughness, allowing it to withstand impact and shock loading without fracturing.
- Wear Resistance: Cold work tool steel is highly resistant to abrasion and wear, prolonging the lifespan of tools and components in demanding environments.
- Edge Retention: Tools made from cold work tool steel retain their sharpness and cutting edge for extended periods, reducing the need for frequent sharpening or replacement.
- Ease of Machining: Cold work tool steel can be machined and fabricated using conventional methods, making it suitable for a wide range of manufacturing processes.
Case Study: Comparison of Cold Work Tool Steel Grades
To illustrate the versatility of cold work tool steel, let’s compare the properties of two commonly used grades: D2 and O1.
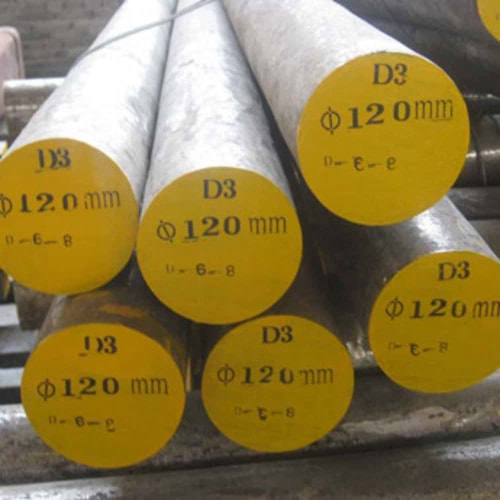
Property | D2 Steel | O1 Steel |
---|---|---|
Hardness (HRC) | 58-62 | 60-65 |
Wear Resistance | Excellent | Good |
Toughness | Moderate | High |
Edge Retention | Very Good | Excellent |
Corrosion Resistance | Fair | Good |
Conclusion
Cold work tool steel is a fundamental material in modern engineering, offering unparalleled hardness, toughness, and wear resistance. Its versatility makes it indispensable across a wide range of industries, from manufacturing to aerospace and medical applications. Understanding the properties and applications of cold work tool steel is essential for engineers and designers seeking to optimize performance and reliability in their projects.
FAQ
Q:What are the main differences between cold work and hot work tool steel?
A:Cold work tool steel is designed to withstand mechanical stress at low temperatures, whereas hot work tool steel is intended for higher temperature applications. Cold work tool steel retains its properties even in environments where heat is not a factor, while hot work tool steel exhibits superior resistance to thermal fatigue and deformation at elevated temperatures.
Q:Can cold work tool steel be welded?
A:Yes, cold work tool steel can be welded using conventional welding techniques. However, preheating and post-weld heat treatment may be necessary to minimize the risk of cracking and ensure optimal mechanical properties in the welded joint.