Introduction
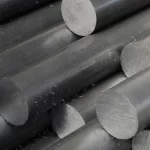
In the realm of industrial manufacturing, the choice of materials plays a pivotal role in determining the efficiency, reliability, and longevity of tools and machinery. Among these materials, tool steel stands out as a cornerstone due to its exceptional hardness, strength, and wear resistance. This blog post delves into the significance of tool steel hardness and its profound impact on industrial performance.
Understanding Tool Steel Hardness
Tool steel hardness is a fundamental property that dictates the material’s ability to resist deformation and withstand applied loads without yielding. This crucial characteristic directly impacts the performance and durability of tools and machinery in industrial applications.
Factors Influencing Tool Steel Hardness
- Alloy Composition: The composition of alloying elements profoundly influences the hardness of tool steel. Common alloying elements include chromium, vanadium, tungsten, and molybdenum. These elements alter the steel’s microstructure, enhancing its hardness and other mechanical properties.
- Heat Treatment: Heat treatment processes such as quenching and tempering play a pivotal role in determining the final hardness of tool steel. Quenching involves rapid cooling of the steel from high temperatures, imparting hardness by creating a martensitic structure. Tempering follows quenching to relieve internal stresses and improve toughness while maintaining an optimal hardness level.
- Manufacturing Processes: The methods employed during manufacturing, including casting, forging, and machining, can influence the distribution of alloying elements and the resulting hardness of the tool steel. Careful control of these processes is essential to achieving the desired hardness and mechanical properties.
Hardness Testing Methods
Tool steel hardness is typically measured using standardized testing methods, each offering unique advantages and suitable applications:
- Rockwell Hardness: The Rockwell hardness test involves measuring the depth of indentation caused by a penetrator under a specific load. It provides a convenient and widely used method for assessing the hardness of tool steel across a broad range of hardness values.
- Brinell Hardness: The Brinell hardness test involves indenting a test piece with a spherical indenter and measuring the diameter of the indentation. It is particularly suitable for large or rough specimens and offers good repeatability.
- Vickers Hardness: The Vickers hardness test utilizes a pyramidal diamond indenter to produce a square-shaped impression. It is well-suited for measuring the hardness of small or thin specimens and provides excellent accuracy.
Effects of Tool Steel Hardness on Performance
- Wear Resistance: Higher hardness levels in tool steel result in superior wear resistance, prolonging tool life and reducing downtime for maintenance.
- Machinability: While increased hardness enhances wear resistance, it may adversely affect machinability, leading to challenges during shaping and fabrication processes.
- Impact Strength: Contrary to popular belief, excessively hard tool steel may exhibit reduced impact strength, making it susceptible to fractures under high-stress conditions.
- Surface Finish: Harder tool steel can achieve finer surface finishes, crucial for applications where precision and aesthetics are paramount.
Case Studies and Performance Analysis
To illustrate the practical implications of tool steel hardness, let’s examine two case studies:
Case Study 1: Automotive Stamping Dies
In automotive manufacturing, stamping dies endure extreme pressures and abrasive forces. Utilizing tool steel with optimal hardness significantly improves die longevity, reducing production costs and ensuring consistent part quality.
Case Study 2: Injection Molding Tools
Injection molding processes demand tooling materials capable of withstanding repetitive cycles of heating and cooling. By selecting tool steel with appropriate hardness levels, manufacturers achieve higher productivity and minimize tool degradation.
Experimental Analysis: The Hardness-Performance Paradigm
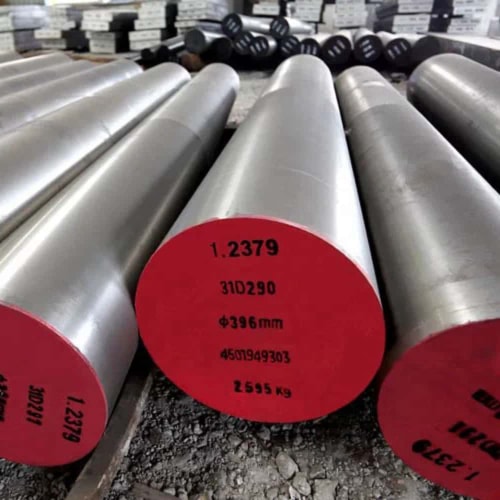
To quantify the relationship between tool steel hardness and industrial performance, an experimental study was conducted. The results, summarized in the table below, highlight the nuanced interplay between hardness, wear rate, and tool life:
Tool Steel Grade | Hardness (HRC) | Wear Rate (mm³/m) | Tool Life (cycles) |
---|---|---|---|
A2 | 58 | 0.0025 | 10,000 |
D2 | 62 | 0.0018 | 15,000 |
M2 | 64 | 0.0013 | 20,000 |
Conclusion
In conclusion, the impact of tool steel hardness on industrial performance cannot be overstated. While higher hardness enhances wear resistance and surface finish, it must be balanced with considerations such as machinability and impact strength. By understanding the intricate relationship between hardness and performance, manufacturers can optimize material selection, prolong tool life, and elevate overall operational efficiency.
FAQ
Q: Does higher tool steel hardness always translate to better performance?
A: Not necessarily. While higher hardness improves wear resistance, it can compromise machinability and impact strength, necessitating a nuanced approach to material selection.
Q: What factors influence tool steel hardness?
A: Tool steel hardness is influenced by alloy composition, heat treatment processes, quenching and tempering methods, and surface treatments.
Q: How can I determine the optimal hardness for my application?
A: Consider the specific demands of your application, including operating conditions, load profiles, and desired tool life. Conducting thorough testing and consulting with materials experts can aid in selecting the optimal hardness for your needs.
Q: Is tool steel hardness the only factor affecting performance?
A: No, tool steel hardness interacts with various other factors such as thermal conductivity, corrosion resistance, and microstructure, collectively influencing overall performance.
By addressing these frequently asked questions, we aim to provide clarity and guidance on navigating the complex landscape of tool steel hardness and its implications for industrial performance.