Introduction
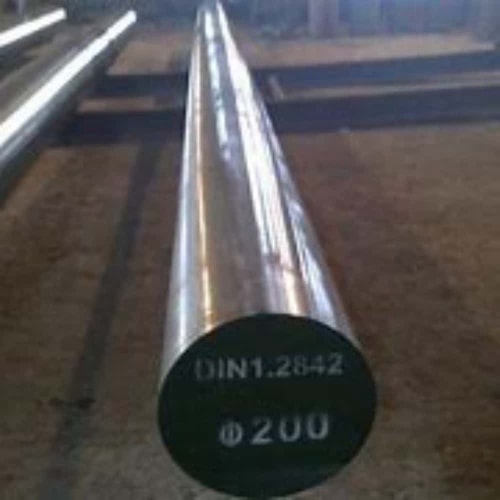
O2 tool steel, renowned for its exceptional wear resistance and toughness, finds extensive applications across various industries. In this comprehensive guide, we delve into the characteristics, applications, and advantages of O2 tool steel, shedding light on its importance in modern manufacturing processes.
Understanding O2 Tool Steel
O2 tool steel, distinguished by its high-carbon and high-chromium composition, stands as a formidable material in the realm of tool steels. Its chemical makeup, consisting of 0.85% carbon, 1.0% manganese, 1.0% silicon, and 0.5% chromium, lays the foundation for its exceptional properties.
The high carbon content contributes significantly to O2 steel’s hardness and wear resistance, crucial attributes for tools subjected to abrasive wear and high impact loads. This inherent hardness allows O2 steel to maintain its cutting edge and dimensional stability over prolonged periods, ensuring consistent performance in various machining and forming applications.
Moreover, the addition of chromium enhances the steel’s resistance to corrosion and oxidation, further bolstering its durability and longevity. This feature makes O2 steel particularly suitable for applications exposed to harsh environments or elevated temperatures, where corrosion resistance is essential for prolonged tool life.
Additionally, manganese and silicon play vital roles in refining the grain structure of O2 steel, promoting uniformity and enhancing its machinability. The presence of these alloying elements facilitates ease of fabrication and precision machining, enabling manufacturers to produce intricate components with minimal effort.
Applications in the Manufacturing Industry
O2 tool steel’s exceptional hardness and wear resistance render it indispensable across a diverse array of manufacturing applications. Its superior properties make it a top choice for industries where precision, durability, and reliability are non-negotiable. Let’s delve deeper into some key applications:
Cutting Tools: O2 steel finds extensive use in the fabrication of cutting tools such as drills, milling cutters, and taps. Its high hardness ensures prolonged edge retention even under the most demanding cutting conditions, leading to increased efficiency and reduced tool wear. Whether in high-speed machining or precision cutting operations, O2 steel enables manufacturers to achieve precise and consistent results, thereby enhancing productivity and reducing production costs.
Blanking Dies: In the realm of metal stamping and forming, O2 tool steel is favored for the production of blanking dies. These dies are subjected to repetitive punching and shearing actions, necessitating exceptional wear resistance and toughness. O2 steel’s robust properties enable blanking dies to maintain their sharpness and integrity over prolonged use, resulting in consistent part quality and reduced downtime. Whether in automotive, aerospace, or consumer electronics, O2 steel plays a vital role in ensuring efficient and reliable blanking operations.
Forming Dies: Forming dies, utilized in processes such as forging, bending, and extrusion, demand materials capable of withstanding high pressures and impact loads. O2 tool steel’s combination of hardness and toughness makes it an ideal candidate for forming dies, where dimensional accuracy and durability are paramount. By withstanding the rigors of forming operations, O2 steel ensures the production of precise and defect-free components across various industries, ranging from heavy machinery to medical devices.
Punches and Press Tools: The manufacturing of punches, press tools, and dies often requires materials capable of enduring repetitive mechanical stresses without succumbing to wear or deformation. O2 steel’s exceptional wear resistance and dimensional stability make it a preferred choice for such applications. Whether in metalworking, plastics molding, or die casting, O2 steel enables the production of high-quality components with tight tolerances and consistent performance, thereby enhancing operational efficiency and product reliability.
Advantages of O2 Tool Steel
- High Wear Resistance: O2 tool steel exhibits superior wear resistance, ensuring prolonged tool life even under extreme conditions.
- Excellent Toughness: Its excellent toughness allows O2 tool steel to withstand high impact loads without failure, making it suitable for heavy-duty applications.
- Good Machinability: With its fine grain structure and machinability, O2 steel facilitates easy fabrication and precision machining processes.
Case Studies and Performance Data
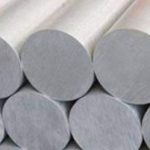
To highlight the practical applications of O2 tool steel, let’s examine a few case studies showcasing its performance in different industrial settings:
Application | Industry | Performance |
---|---|---|
Cutting Tools | Automotive | Extended tool life, reduced machining costs |
Blanking Dies | Aerospace | Superior wear resistance, consistent part quality |
Forming Dies | Manufacturing | Enhanced durability, reduced downtime |
Conclusion
In conclusion, O2 tool steel stands as a versatile and reliable material, offering a myriad of benefits across diverse industries. Its exceptional properties, including high wear resistance, toughness, and machinability, make it an indispensable asset in modern manufacturing processes.
FAQ
Q: What are the main characteristics of O2 tool steel?
A: O2 tool steel is characterized by its high carbon content, chromium addition, exceptional wear resistance, toughness, and machinability.
Q: What are the common applications of O2 tool steel?
A: O2 tool steel finds applications in cutting tools, blanking dies, forming dies, punches, and various other industrial tools and components.
Q: How does O2 tool steel compare to other tool steel grades?
A: Compared to other tool steel grades, O2 tool steel offers superior wear resistance and toughness, making it suitable for demanding applications where extended tool life and durability are essential.
In summary, O2 tool steel emerges as a versatile material with a wide range of applications, showcasing its significance in modern manufacturing processes. Its unique combination of properties makes it a preferred choice for engineers and manufacturers striving for performance and reliability.