Welcome to My Blog!
Before we dive into the content, I’d love for you to join me on my social media platforms where I share more insights, engage with the community, and post updates. Here’s how you can connect with me:
Facebook:https://www.facebook.com/profile.php?id=100090797846538
Now, let’s get started on our journey together. I hope you find the content here insightful, engaging, and valuable.
Table of Contents
Introduction
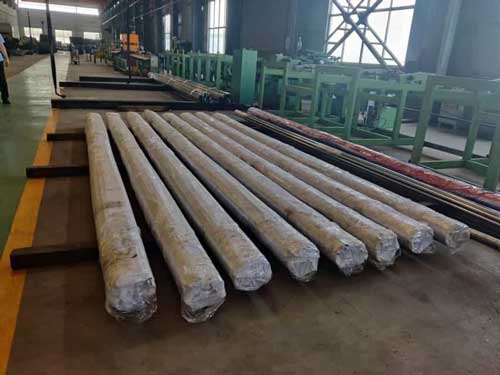
What Are Tool Steel Grades?
Tool steel grades are classifications that describe the composition, properties, and best uses of the material. Tool steels are primarily used to manufacture tools, molds, and dies due to their high hardness, resistance to abrasion, and ability to withstand high temperatures.
Why Do Grades of Tool Steel Matter?
- Performance: The grade determines the material’s ability to handle wear and tear.
- Application: Certain grades are better suited for specific tools or conditions.
- Longevity: Choosing the right grade can extend the lifespan of your tools.
Common Categories of Tool Steel Grades
- Water-Hardening (W-Grade): Known for affordability and ease of use.
- Cold-Work (O, A, D Grades): Ideal for low-temperature applications.
- Shock-Resistant (S-Grade): Designed to handle high-impact tasks.
- Hot-Work (H-Grade): Suitable for high-temperature environments.
- High-Speed (T, M Grades): Made for cutting and machining.
Exploring Key Grades of Tool Stee
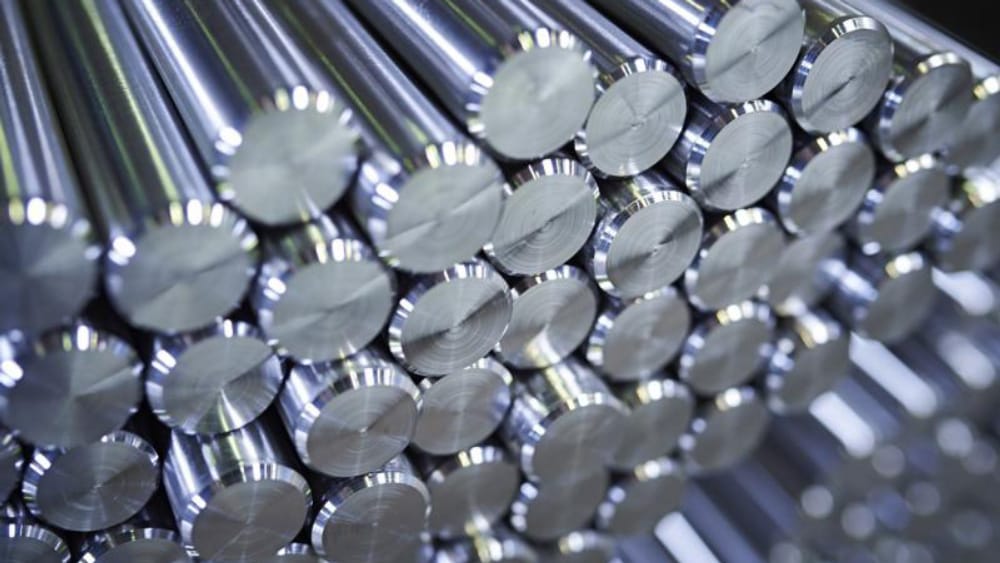
Water-Hardening Tool Steel (W-Grade)
- Characteristics: Excellent machinability, high surface hardness, low cost.
- Applications: Cutting tools, knives, and hand tools.
Cold-Work Tool Steel (O, A, D Grades)
- Oil-Hardening (O-Grade): Great wear resistance, affordable, used in shearing blades.
- Air-Hardening (A-Grade): Balanced performance, easy to harden.
- High Carbon, High Chromium (D-Grade): Exceptional wear resistance, suitable for high-stress applications.
Shock-Resistant Tool Steel (S-Grade)
- Characteristics: High impact resistance, excellent toughness.
- Applications: Hammers, punches, and chisels.
Hot-Work Tool Steel (H-Grade)
- Characteristics: Withstands high temperatures, excellent thermal fatigue resistance.
- Applications: Forging dies, extrusion dies, and casting molds.
High-Speed Tool Steel (T, M Grades)
- Characteristics: Retains hardness at high temperatures, ideal for machining tools.
- Applications: Drill bits, saw blades, and lathe tools.
Grades of Tool Steel: Comparison Table
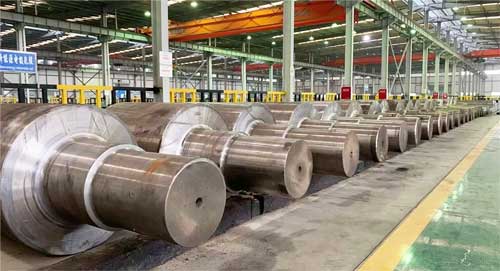
Grade | Key Properties | Applications |
---|---|---|
W-Grade | Affordable, surface hardness | Hand tools, knives |
O-Grade | Wear resistance, oil-hardened | Shearing blades, gauges |
A-Grade | Air-hardened, dimensional stability | Stamps, precision tools |
D-Grade | High wear resistance, high stress use | Dies, punches |
S-Grade | Shock-resistant, tough | Hammers, chisels |
H-Grade | Heat-resistant, thermal fatigue resistant | Forging and extrusion dies |
T-Grade | Retains hardness at high temperatures | Cutting tools, drills |
M-Grade | High-speed machining capability | Lathe tools, saw blades |
Factors to Consider When Choosing the Right Grade of Tool Steel
Application Requirements
Consider the tool’s purpose—cutting, shaping, or enduring high impact. For example, high-speed steel is ideal for cutting tools, while shock-resistant steel is better for hammers.
Environmental Conditions
If the tool will be exposed to extreme temperatures, opt for H-Grade or T-Grade steel. For low-temperature applications, cold-work steels are a better fit.
Wear and Tear
If the tool will experience significant abrasion, D-Grade or high-chromium tool steel is recommended for its superior wear resistance.
Machinability and Hardening Process
Some grades, like W-Grade, are easier to machine and harden, making them suitable for quick production.
Budget Constraints
While some grades like W-Grade are cost-effective, premium grades like T-Grade or M-Grade offer higher performance for specialized tasks.
Maintenance and Care for Tool Steel
- Proper Storage: Store in a dry, controlled environment to prevent rust.
- Regular Inspections: Check for cracks, chips, or wear, and address them promptly.
- Sharpening: Maintain cutting tools by sharpening edges to extend their usability.
- Lubrication: Use appropriate lubricants to reduce friction and enhance performance.
Conclusion
Choosing the right grade of tool steel is essential to optimizing performance and extending tool life. By understanding the properties and applications of various grades of tool steel, you can make informed decisions that align with your needs. From water-hardening steels for simple tools to high-speed steels for precision machining, there is a grade of tool steel for every purpose.
FAQ
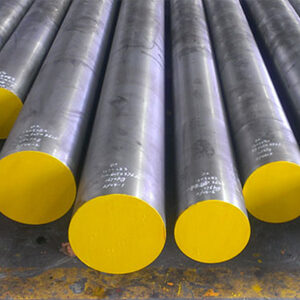
What is the most durable grade of tool steel?
D-Grade tool steel is highly durable due to its wear resistance and toughness, making it ideal for high-stress applications.
Can tool steel be welded?
Yes, but it requires specialized techniques and careful preheating to avoid cracking due to high hardness levels.
Which grade of tool steel is best for cutting tools?
High-speed steels, such as T-Grade and M-Grade, are designed for cutting and machining applications.
What is the main difference between cold-work and hot-work tool steels?
Cold-work steels are designed for applications in lower temperatures, while hot-work steels can withstand high temperatures without losing their properties.
Is tool steel prone to rust?
Tool steels with higher carbon content, like W-Grade, can rust if not stored properly. However, grades with added chromium, like D-Grade, offer better corrosion resistance.
How do I know which grade to choose for a specific application?
Consider factors like temperature, impact resistance, wear, and budget. Consult material experts or reference the properties of each grade for guidance.
Are all tool steels heat-treated?
Yes, heat treatment is an essential process for tool steels to achieve their desired hardness and performance characteristics.
Can tool steels be recycled?
Yes, tool steels are recyclable and can be repurposed into new tools or components, contributing to sustainable practices