Introduction
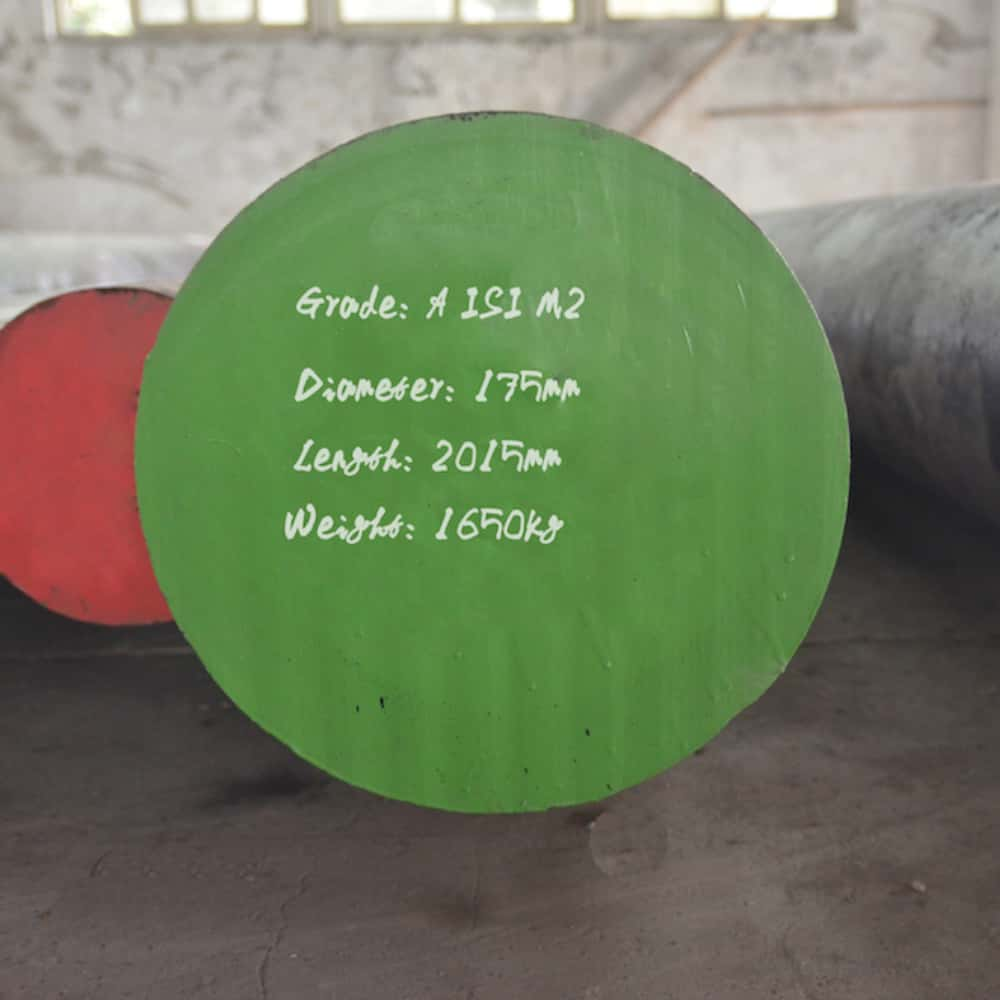
High Speed Steel M2, often simply referred to as M2, is a true titan among steel alloys. Renowned for its exceptional hardness, wear resistance, and toughness, M2 has earned its place as a cornerstone in manufacturing industries worldwide. From cutting tools that effortlessly slice through the toughest materials to dies that shape metals with precision, M2’s versatility and durability are unmatched. In this comprehensive exploration, we will delve deep into the multifaceted world of high speed steel M2, uncovering its properties, applications, and the numerous advantages it brings to the table.
The Composition and Properties: A Symphony of Elements
high speed steel M2 is not merely a steel alloy; it’s a carefully orchestrated blend of elements, each contributing to its extraordinary performance. Primarily composed of iron, carbon, tungsten, molybdenum, vanadium, and chromium, this alloying composition results in a symphony of properties that set M2 apart:
- Unmatched Hardness: M2 can be hardened to extraordinary levels, making it capable of withstanding the rigors of cutting through even the most challenging materials.
- Exceptional Wear Resistance: The fine-grained structure of M2 imparts exceptional wear resistance, ensuring that tools and components maintain their sharpness and precision for extended periods.
- Remarkable Toughness: Despite its incredible hardness, M2 exhibits remarkable toughness, reducing the risk of chipping or breaking, even under demanding conditions.
- Red Hardness: M2 retains its hardness at elevated temperatures, enabling high-speed machining operations without compromising performance.
- Good Machinability: M2 is relatively easy to machine, making it a cost-effective option for a wide range of applications.
Applications: M2’s Versatility Shines
The exceptional properties of high speed steel M2 make it a versatile material, finding applications in a diverse range of industries. Some of the most prominent applications include:
- Cutting Tools: M2 is the backbone of cutting tool manufacturing, powering drills, milling cutters, reamers, and taps that effortlessly machine metals, plastics, and composites.
- Dies: M2 is extensively used in the production of stamping dies, drawing dies, and extrusion dies, shaping metals with precision and efficiency.
- Punches: M2-crafted punches are indispensable in various metalworking operations, delivering clean and accurate cuts.
- Other Applications: Beyond cutting tools and dies, M2 finds its way into components like knives, shears, and surgical instruments, where its durability and precision are highly valued.
The Advantages: Why Choose M2?
The decision to use high speed steel M2 is often driven by a compelling set of advantages:
- Unparalleled Durability: M2 offers exceptional durability, making it a cost-effective choice in the long run.
- Versatility Redefined: M2’s versatility allows it to excel in a wide range of applications, from heavy-duty industrial tasks to intricate precision work.
- Precision Perfected: M2’s excellent wear resistance ensures that components maintain their precision and accuracy over time.
- Heat Resistance: M2’s ability to withstand high temperatures makes it suitable for demanding applications where heat is a significant factor.
A Comparative Analysis: M2 vs. Other High Speed Steels
To gain a deeper understanding of M2’s position within the high speed steel family, let’s compare it with other renowned alloys:
Steel Grade | Composition | Hardness | Toughness | Typical Applications |
---|---|---|---|---|
M2 | High carbon, tungsten, molybdenum, vanadium, chromium | Very high | Good | Cutting tools, dies, punches |
M4 | Similar to M2, but with higher vanadium content | Very high | Good | High-speed machining, heavy-duty cutting |
T1 | High carbon, tungsten, molybdenum, chromium | High | Good | General-purpose cutting tools |
M7 | High carbon, tungsten, molybdenum, vanadium, chromium | Very high | Good | High-temperature applications, aerospace |
Heat Treatment: Unleashing M2’s Full Potential
The heat treatment process is a critical step in unlocking M2’s full potential. It involves a series of carefully controlled thermal cycles:
- Annealing: This initial step softens the steel, making it easier to machine.
- Hardening: The steel is heated to a specific temperature and then rapidly cooled (quenched) to achieve maximum hardness.
- Tempering: A controlled reheating process follows, reducing brittleness and improving toughness.
Factors to Consider: Making Informed Decisions
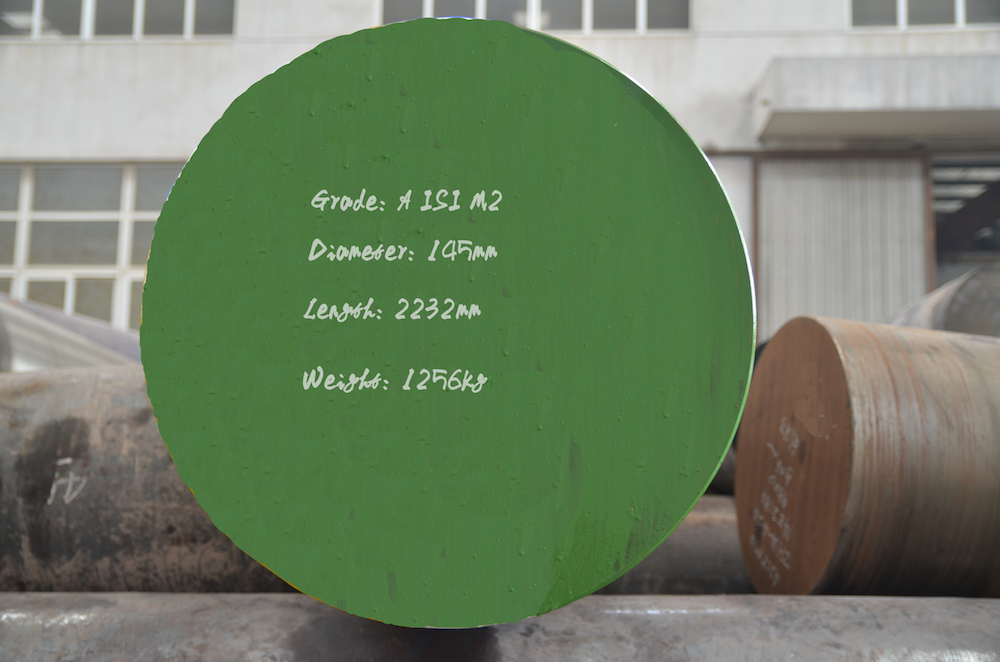
When selecting high speed steel M2 for a specific application, several factors should be carefully considered:
- Required Hardness: The desired level of hardness will dictate the appropriate heat treatment process.
- Wear Resistance: The level of wear resistance needed will influence the choice of M2 or a different alloy.
- Toughness: The required toughness will impact the selection of the heat treatment process and the specific grade of M2.
- Cost: The cost of M2 will vary depending on the grade, quantity, and supplier.
Conclusion
High speed steel M2 stands as a testament to the ingenuity of metallurgy. Its exceptional properties, versatility, and durability have made it an indispensable material in countless industries. By understanding the characteristics and benefits of M2, engineers and manufacturers can harness its power to create high-performance components that meet the demands of today’s technologically advanced world.
FAQ
Q: What is high speed steel M2?
A: High speed steel M2 is a type of alloy steel known for its exceptional hardness, wear resistance, and toughness. It is widely used in manufacturing industries for cutting tools, dies, and other components that require durability and precision.
Q: How does high speed steel M2 compare to other steel alloys?
A: M2 offers superior hardness, wear resistance, and toughness compared to many other steel alloys. It can withstand high temperatures and maintain its cutting edge, making it a preferred choice for demanding applications.
Q: How is high speed steel M2 heat treated?
A: High speed steel M2 undergoes a multi-step heat treatment process involving annealing, hardening, and tempering to achieve its optimal properties.